Induction heating, while efficient and precise, comes with several disadvantages that can impact its practicality and cost-effectiveness. The high cost of equipment is a significant barrier, making it less accessible for smaller operations. Additionally, the need for precise alignment and uniform air gaps can complicate setup and maintenance. The limited penetration depth of the magnetic field restricts its use to specific applications, and the potential for high temperature gradients can lead to damage in molds or materials. Furthermore, induction furnaces lack refining capacity, requiring charge materials to be free of oxides and of known composition, which can limit their versatility and increase operational complexity.
Key Points Explained:
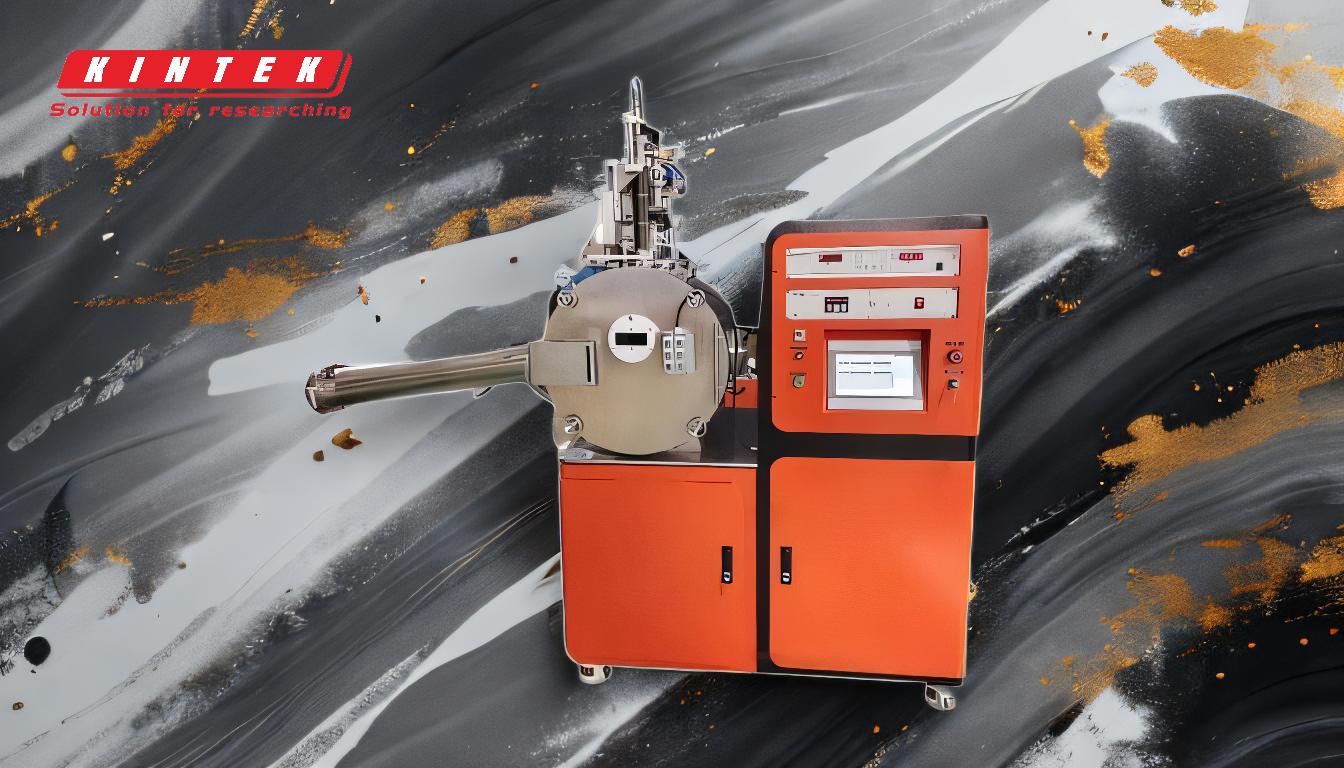
-
High Cost of Equipment:
- Induction heating systems are generally more expensive than traditional heating methods. The initial investment includes not only the induction heating equipment but also the necessary power supplies and cooling systems. This high cost can be prohibitive for small to medium-sized enterprises, making it less accessible compared to other heating technologies.
-
Precise Alignment and Uniform Air Gaps:
- Induction heating requires precise alignment between the induction coil and the workpiece. Any misalignment can lead to inefficient heating and potential damage to the equipment. Additionally, maintaining uniform air gaps is crucial for consistent heating, which can be challenging and time-consuming, especially in complex or irregularly shaped workpieces.
-
Limited Penetration Depth of the Magnetic Field:
- The magnetic field generated by induction heating has a limited penetration depth, which means it is only effective for heating the surface or near-surface regions of a material. This limitation restricts its use to applications where deep, uniform heating is not required, such as surface hardening or localized heating.
-
Potential for High Temperature Gradients:
- Induction heating can create high temperature gradients within the material being heated. These gradients can lead to thermal stresses, which may cause warping, cracking, or other forms of damage, particularly in molds or delicate components. Managing these gradients requires careful control of the heating process, which can add to the complexity and cost.
-
Lack of Refining Capacity in Induction Furnaces:
- Induction furnaces, unlike some other types of furnaces, do not have the ability to refine the material being melted. This means that the charge materials must be free of oxides and of a known composition before being introduced into the furnace. Any impurities or unknown elements in the charge can lead to inconsistencies in the final product. Additionally, some alloying elements may be lost due to oxidation during the melting process, requiring them to be re-added, which can increase material costs and complicate the production process.
In summary, while induction heating offers many advantages, such as efficiency and precision, it also comes with significant disadvantages that must be carefully considered. The high cost of equipment, the need for precise setup, limited penetration depth, potential for thermal damage, and lack of refining capacity in induction furnaces are all factors that can impact the practicality and cost-effectiveness of using induction heating in various applications.
Summary Table:
Disadvantage | Description |
---|---|
High Cost of Equipment | Induction heating systems are expensive, including equipment, power supplies, and cooling systems. |
Precise Alignment and Air Gaps | Requires exact alignment and uniform air gaps, complicating setup and maintenance. |
Limited Penetration Depth | Effective only for surface or near-surface heating, limiting its use in deep heating applications. |
High Temperature Gradients | Can cause thermal stresses, leading to warping or cracking in materials. |
Lack of Refining Capacity | Charge materials must be free of oxides and of known composition, increasing operational complexity. |
Considering induction heating for your operations? Contact us today to discuss your needs and explore alternatives!