Heat treatment is a critical process in manufacturing, and its quality is influenced by several factors. These include uniform temperature distribution, proper gas circulation, cycle times and temperatures, and proactive maintenance planning. Ensuring these elements are optimized can significantly enhance the quality of the final product, reduce downtime, and minimize maintenance costs.
Key Points Explained:
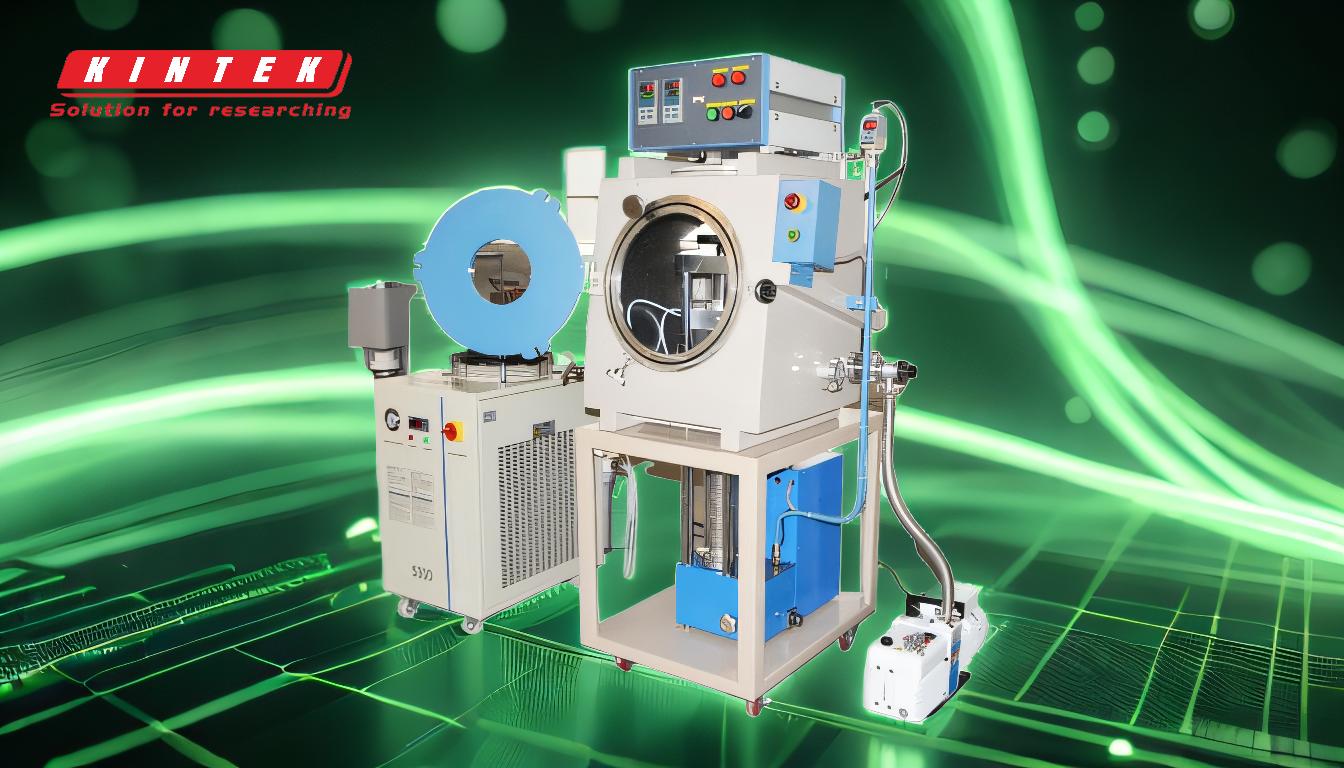
-
Uniform Temperature Distribution:
- Importance: Uniform temperature distribution throughout the hot zone is crucial for consistent heat treatment results. Uneven heating can lead to variations in material properties, causing defects such as warping or cracking.
- Implementation: To achieve uniform temperature distribution, it is essential to use well-designed furnaces with proper insulation and heating elements. Regular calibration and maintenance of temperature sensors and controllers are also necessary.
-
Proper Gas Circulation:
- Importance: Proper gas circulation, including the control of partial pressure and quench gas, is vital for achieving the desired material properties. Inadequate gas flow can result in incomplete or uneven heat treatment.
- Implementation: Ensure that the furnace has an efficient gas circulation system. This includes using appropriate gas mixtures and maintaining the correct flow rates. Regular checks and maintenance of gas delivery systems are also important.
-
Cycle Times and Temperatures:
- Importance: The cycle times and temperatures chosen for heat treatment directly affect the final product quality. Incorrect settings can lead to under or over-treatment, resulting in suboptimal material properties.
- Implementation: Develop and follow precise heat treatment schedules based on material specifications and desired outcomes. Use advanced control systems to monitor and adjust cycle times and temperatures accurately.
-
Proactive Maintenance Planning:
- Importance: Anticipating potential problems that could lead to extensive maintenance or downtime is beneficial. Preventive maintenance can help avoid unexpected equipment failures and ensure consistent heat treatment quality.
- Implementation: Implement a comprehensive maintenance schedule that includes regular inspections, cleaning, and replacement of worn-out parts. Use predictive maintenance techniques, such as vibration analysis and thermal imaging, to identify potential issues before they become critical.
By focusing on these key factors, manufacturers can significantly improve the quality of heat treatment processes, leading to better final products and reduced operational costs.
Summary Table:
Factor | Importance | Implementation |
---|---|---|
Uniform Temperature Distribution | Ensures consistent results; prevents defects like warping or cracking. | Use well-designed furnaces, proper insulation, and regular calibration. |
Proper Gas Circulation | Achieves desired material properties; prevents incomplete heat treatment. | Ensure efficient gas systems, use correct gas mixtures, and maintain flow rates. |
Cycle Times and Temperatures | Directly impacts product quality; incorrect settings cause under/over-treatment. | Follow precise schedules and use advanced control systems for accuracy. |
Proactive Maintenance Planning | Reduces downtime; prevents equipment failures and ensures consistent quality. | Implement regular inspections, cleaning, and predictive maintenance techniques. |
Optimize your heat treatment process today—contact our experts for tailored solutions!