Heat treatment is a critical process in metallurgy that enhances the mechanical properties of metals, such as strength, hardness, and durability. The three most important factors in material heat treatment are the temperature to which the metal is heated, the duration it is held at that temperature (soaking time), and the method and rate of cooling. These variables are carefully controlled based on the material type and the desired outcome, ensuring uniform temperature distribution, proper gas circulation, and optimal cycle times. Understanding these factors is essential for achieving high-quality results and avoiding potential issues like maintenance or downtime.
Key Points Explained:
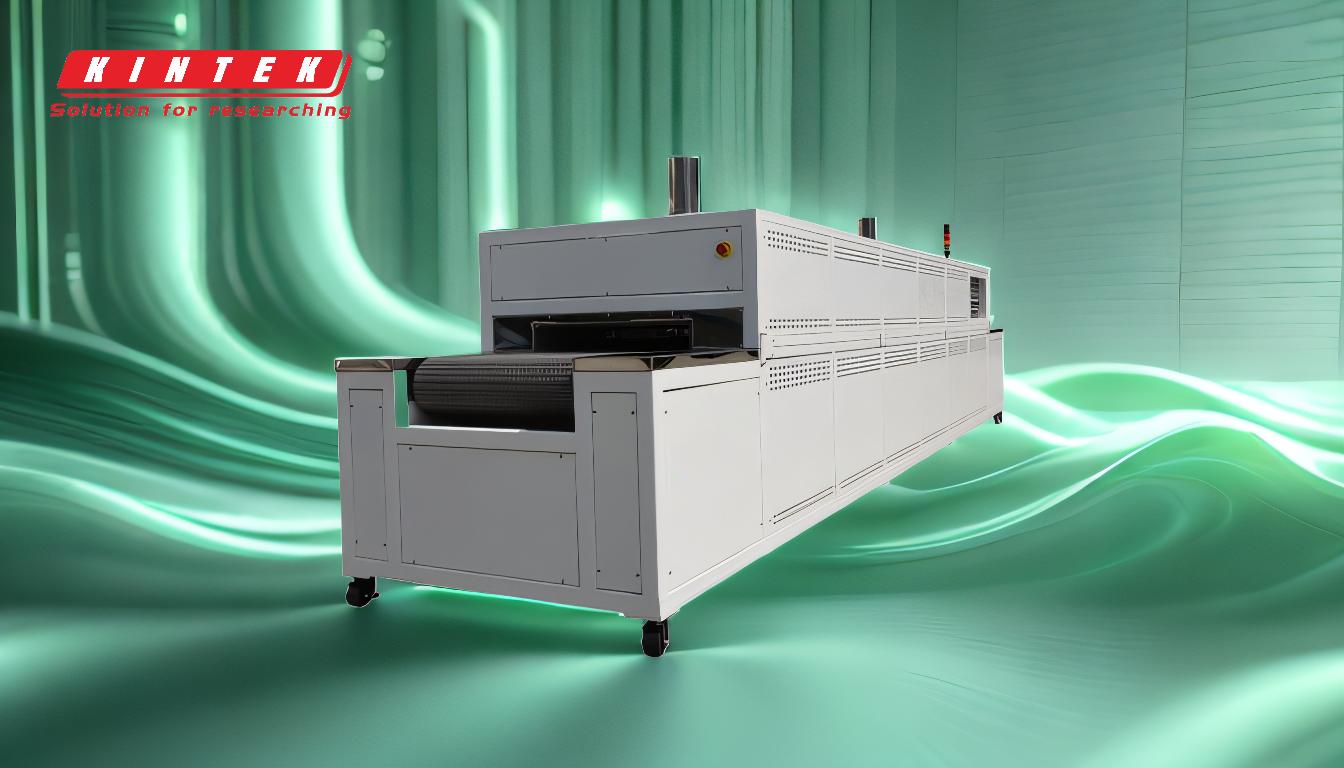
-
Temperature Control:
- Importance: The temperature to which the metal is heated is crucial because it determines the phase transformations within the material. Different metals and alloys require specific temperatures to achieve the desired microstructure and properties.
- Process: Gradual heating ensures uniform temperature distribution throughout the material, preventing stress and distortion. The temperature must be precise to avoid overheating or underheating, which can lead to suboptimal results.
- Application: For example, in the oil and gas industry, components like pipelines and drilling equipment require precise heat treatment to withstand extreme conditions.
-
Soaking Time:
- Importance: The duration the metal is held at the target temperature (soaking time) allows for the complete transformation of the material's microstructure. This ensures uniformity in properties throughout the part.
- Process: Soaking time varies depending on the material's thickness, composition, and the desired outcome. Insufficient soaking can result in incomplete transformation, while excessive soaking may lead to grain growth and reduced strength.
- Application: In industries like aerospace, where components must endure high stress and fatigue, precise soaking times are critical to achieving the necessary mechanical properties.
-
Cooling Method and Rate:
- Importance: The method and rate of cooling significantly influence the final properties of the material. Rapid cooling (quenching) can increase hardness, while slower cooling (annealing) can improve ductility and reduce internal stresses.
- Process: Cooling can be achieved through various mediums, such as air, oil, water, or gas, depending on the material and desired outcome. The cooling rate must be carefully controlled to avoid cracking or distortion.
- Application: For instance, in automotive manufacturing, gears and shafts are often quenched to achieve high hardness, followed by tempering to balance toughness and reduce brittleness.
By meticulously controlling these three factors—temperature, soaking time, and cooling method—engineers and metallurgists can tailor the heat treatment process to meet specific performance requirements, ensuring the durability and reliability of critical components across various industries.
Summary Table:
Factor | Importance | Process | Application |
---|---|---|---|
Temperature Control | Determines phase transformations and microstructure. | Gradual heating ensures uniform temperature distribution. | Used in oil and gas for pipelines and drilling equipment. |
Soaking Time | Ensures complete transformation of microstructure. | Varies based on material thickness and composition. | Critical in aerospace for high-stress components. |
Cooling Method | Influences final properties like hardness and ductility. | Controlled cooling via air, oil, water, or gas to avoid cracking. | Applied in automotive for gears and shafts. |
Optimize your heat treatment process for superior results—contact our experts today!