A calcination furnace is a specialized industrial or laboratory furnace designed to perform the process of calcination, which involves heating a material to high temperatures to drive off absorbed moisture, remove volatile constituents like carbon dioxide, and oxidize part or all of the substance. This process is essential in various industries, including ceramics, metallurgy, and chemical manufacturing, where precise thermal treatment is required to achieve desired material properties. Calcination furnaces are equipped with features such as high-temperature capabilities, programmable controls, and energy-efficient designs to ensure optimal performance and safety. They are used in applications ranging from sample preparation in laboratories to large-scale industrial processes.
Key Points Explained:
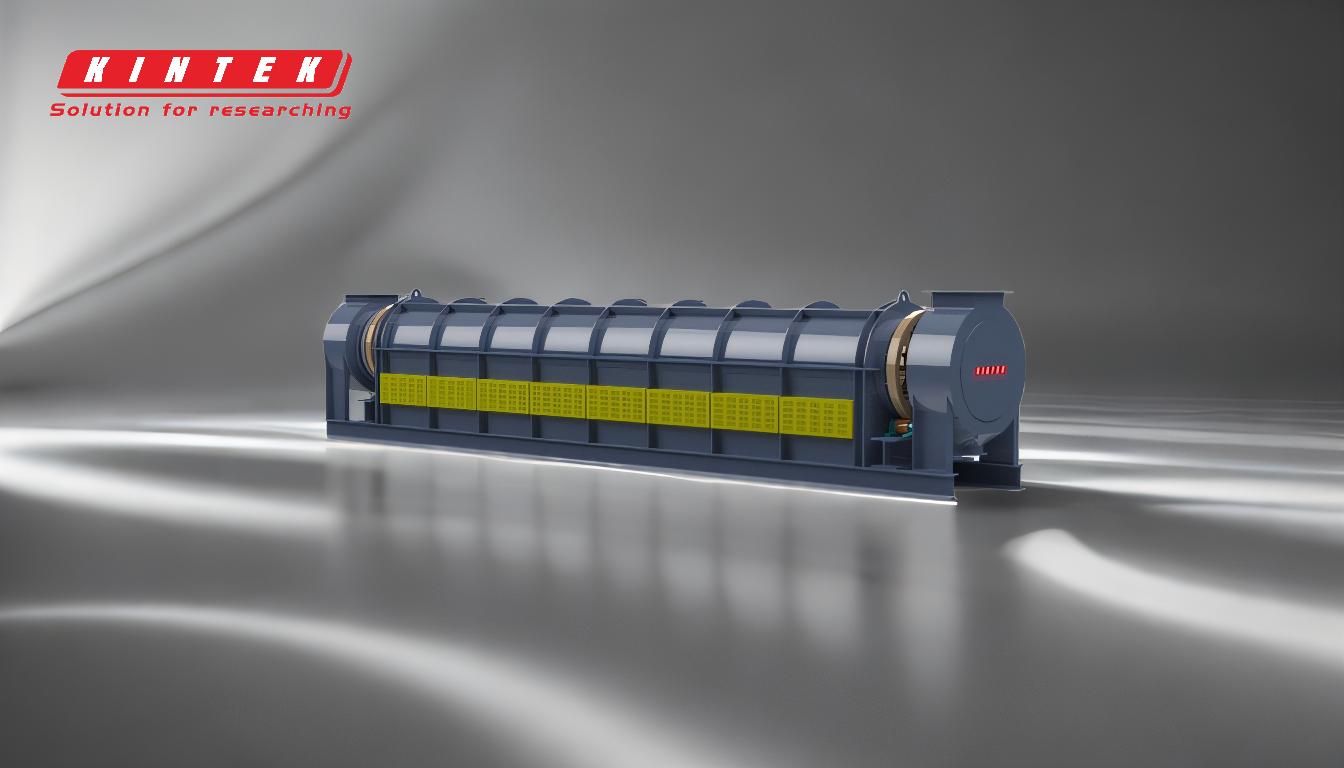
-
Definition and Purpose of a Calcination Furnace:
- A calcination furnace is a thermal processing device used to heat materials to high temperatures for the purpose of calcination.
- Calcination involves driving off absorbed moisture, removing volatile constituents (e.g., carbon dioxide, sulfur dioxide), and oxidizing part or all of the material.
-
Key Objectives of Calcination:
- Moisture Removal: Eliminates water absorbed by the material, which is crucial for processes requiring dry starting materials.
- Volatile Constituent Removal: Expels gases like carbon dioxide or sulfur dioxide, often present in raw materials or formed during heating.
- Oxidation: Facilitates chemical reactions that oxidize the material, altering its composition and properties.
-
Applications of Calcination Furnaces:
- Industrial Processes: Used in industries such as cement production, ceramics, and metallurgy to process raw materials like limestone, gypsum, and metal ores.
- Laboratory Use: Employed for sample preparation, material testing, and research in fields like chemistry, materials science, and geology.
- Environmental Applications: Utilized in waste treatment to stabilize or detoxify hazardous materials.
-
Key Features of Calcination Furnaces:
- High-Temperature Capability: Designed to withstand and maintain temperatures up to 1200°C or higher, depending on the application.
- Programmable Controls: Equipped with PID (Proportional-Integral-Derivative) controllers and programmable segments for precise temperature regulation and heating rates.
- Energy Efficiency: Incorporates insulation materials like ceramic fiber or alumina fiber to minimize heat loss and reduce energy consumption.
- Safety Features: Includes double-layer steel casings, fan cooling systems, and temperature monitoring to ensure operator safety and equipment longevity.
-
Types of Calcination Furnaces:
- Laboratory Furnaces: Compact, cylindrical designs with integrated heating elements and insulation, ideal for small-scale experiments and sample processing.
- Industrial Furnaces: Larger, robust designs capable of handling bulk materials and continuous operation, often used in manufacturing and processing plants.
- Specialized Furnaces: Tailored for specific applications, such as burnout furnaces for removing organic binders or sintering furnaces for powder metallurgy.
-
Design and Operational Considerations:
- Heating Elements: Typically made of materials like silicon carbide or molybdenum disilicide, arranged to ensure uniform temperature distribution.
- Insulation: High-purity alumina fiber or ceramic fiber insulation is used to enhance thermal efficiency and reduce heat loss.
- Mobility and Space Efficiency: Laboratory models often feature compact designs with casters for easy movement, while industrial models are stationary but optimized for space utilization.
-
Advantages of Using Calcination Furnaces:
- Precision: Allows for controlled and repeatable thermal processing, ensuring consistent material properties.
- Versatility: Suitable for a wide range of materials and applications, from small-scale research to large-scale production.
- Efficiency: Advanced insulation and programmable controls minimize energy consumption and operational costs.
-
Comparison with Other Furnaces:
- Sintering Furnaces: Focus on bonding particles at high temperatures without melting, often used in powder metallurgy and ceramics.
- Carbonization Furnaces: Designed for converting organic materials into carbon through pyrolysis, with features like smokeless operation and high carbonization rates.
- High-Temperature Furnaces: Used for processes like fusion, melting, and testing, with heating elements on all sides for uniform temperature distribution.
In summary, a calcination furnace is a versatile and essential tool for thermal processing, enabling precise control over material properties through the removal of moisture, volatile constituents, and oxidation. Its design and features make it suitable for a wide range of applications, from laboratory research to industrial production.
Summary Table:
Key Feature | Description |
---|---|
High-Temperature Capability | Withstands up to 1200°C or higher for demanding applications. |
Programmable Controls | PID controllers ensure precise temperature regulation and heating rates. |
Energy Efficiency | Advanced insulation minimizes heat loss and reduces energy consumption. |
Safety Features | Includes double-layer steel casings, fan cooling, and temperature monitoring. |
Applications | Used in ceramics, metallurgy, cement production, and lab research. |
Types | Laboratory, industrial, and specialized furnaces for specific processes. |
Upgrade your thermal processing capabilities with a calcination furnace—contact us today for expert guidance!