The high-temperature method, specifically the High-Temperature–Short-Time (HTST) method, is a process used in various industries, including food processing and materials science, to achieve specific outcomes by exposing materials or products to high temperatures for a short duration. This method is designed to preserve quality characteristics, such as nutrients in food or material properties, while ensuring efficiency. A high temperature furnace is a key piece of equipment used in this process, providing controlled and uniform heating to achieve the desired results. Below, we break down the key aspects of this method and its applications.
Key Points Explained:
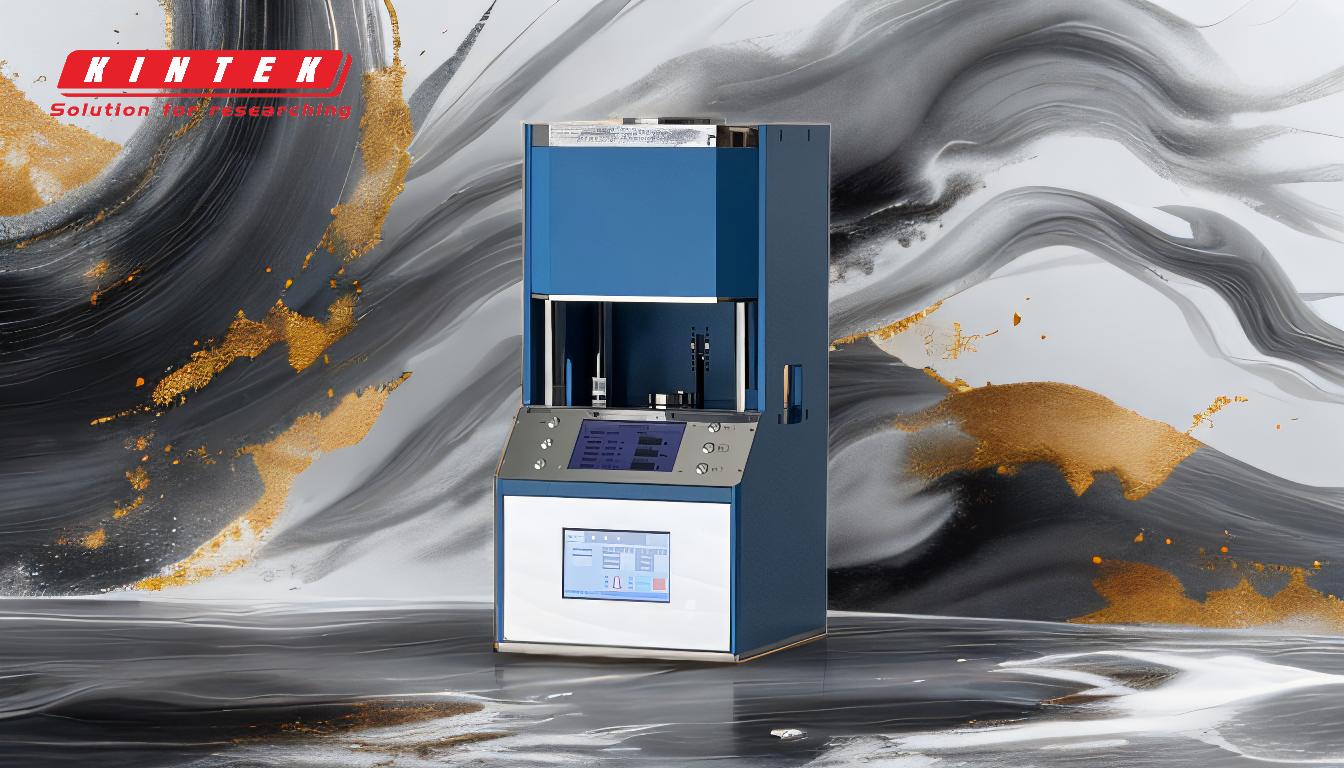
-
Definition of the High-Temperature Method
- The high-temperature method involves exposing materials or products to elevated temperatures for a short period.
- In the context of food processing, this is known as the High-Temperature–Short-Time (HTST) method.
- The goal is to achieve specific outcomes, such as microbial reduction or material transformation, while minimizing damage to the product's quality.
-
Key Features of the HTST Method
- Short Exposure Time: The process is designed to be quick, reducing the risk of over-processing.
- High Temperature: Temperatures are significantly higher than conventional methods, ensuring effectiveness.
- Controlled Conditions: Time and temperature are carefully calibrated based on factors like the type, size, and shape of the material or product.
-
Role of High-Temperature Furnaces
- A high temperature furnace is essential for achieving the required conditions.
- These furnaces are equipped with heating elements on both sides of the chamber to ensure uniform heat distribution.
- They are used in industries such as metallurgy, ceramics, and food processing to achieve precise thermal control.
-
Applications of the High-Temperature Method
- Food Processing: The HTST method is commonly used for pasteurization, preserving nutrients and flavor while ensuring safety.
- Materials Science: High-temperature methods are used for sintering, annealing, and other processes that alter material properties.
- Industrial Manufacturing: Processes like glass tempering and metal hardening rely on high-temperature techniques.
-
Advantages of the HTST Method
- Quality Retention: The short exposure time minimizes damage to the product's quality, such as nutrient loss in food or structural changes in materials.
- Efficiency: The process is faster and more energy-efficient compared to traditional methods.
- Versatility: It can be adapted to a wide range of materials and products.
-
Considerations for Equipment Selection
- When choosing a high temperature furnace, factors like temperature range, heating uniformity, and chamber size must be considered.
- The furnace should be compatible with the specific requirements of the HTST method, such as rapid heating and cooling capabilities.
-
Future Trends in High-Temperature Methods
- Advances in furnace technology, such as improved insulation and energy efficiency, are enhancing the effectiveness of high-temperature methods.
- Automation and precise control systems are making these processes more reliable and scalable.
By understanding the principles and applications of the high-temperature method, industries can optimize their processes to achieve better outcomes with improved efficiency and quality retention. The use of advanced equipment like high temperature furnaces plays a critical role in enabling these advancements.
Summary Table:
Aspect | Details |
---|---|
Definition | Exposing materials/products to high temperatures for a short duration. |
Key Features | Short exposure time, high temperature, controlled conditions. |
Applications | Food processing (pasteurization), materials science (sintering, annealing). |
Advantages | Quality retention, efficiency, versatility. |
Equipment | High-temperature furnaces with uniform heating and precise control. |
Future Trends | Improved insulation, energy efficiency, automation, and control systems. |
Discover how the high-temperature method can optimize your processes—contact us today for expert advice!