Pressureless compaction is a method used to form and compact metal powder particles into dense agglomerates without applying external pressure. This process relies on the natural packing behavior of powder particles, often enhanced by techniques such as vibration or slip casting. The key to achieving high-density agglomerates lies in the size distribution of the powder particles, which influences how effectively they pack together. Unlike traditional compaction methods that use mechanical pressure, pressureless compaction is advantageous for producing complex shapes and minimizing equipment costs. However, it requires careful control of particle size and distribution to ensure optimal density and structural integrity.
Key Points Explained:
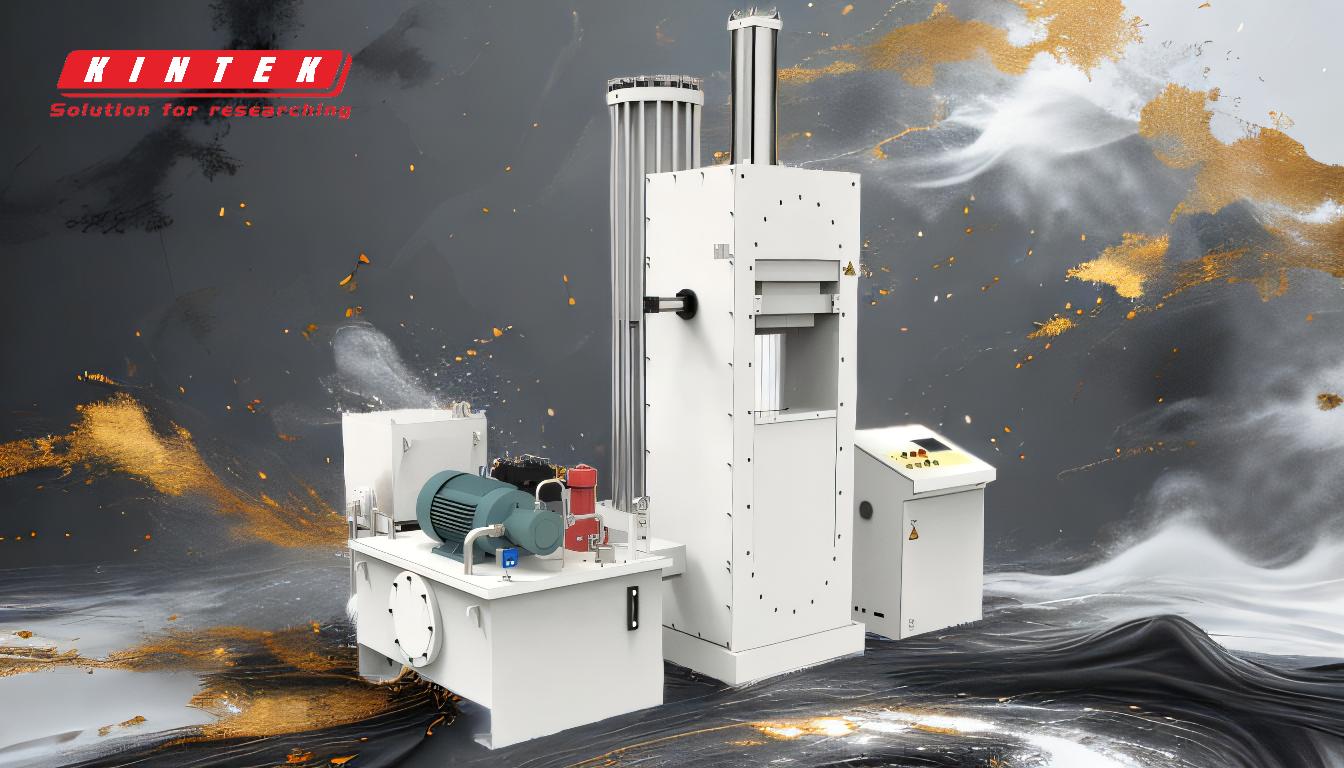
-
Definition of Pressureless Compaction:
- Pressureless compaction is a process where metal powder particles are formed into dense agglomerates without the application of external pressure. Instead, it relies on natural packing mechanisms, often aided by techniques like vibration or slip casting.
-
Importance of Particle Size Distribution:
- The size distribution of the powder particles is critical in pressureless compaction. A well-controlled distribution ensures better packing density, as smaller particles can fill the gaps between larger ones, leading to higher overall density.
- In processes like loose powder sintering, vibratory compacting, and slip casting, the particle size directly affects the final density and mechanical properties of the compacted material.
-
Techniques Used in Pressureless Compaction:
- Loose Powder Sintering: This involves heating the powder particles to a temperature below their melting point, allowing them to bond and form a solid structure without external pressure.
- Vibratory Compacting: Vibration is used to enhance the natural packing of particles, reducing voids and increasing density.
- Slip Casting: A slurry of powder particles in a liquid medium is poured into a mold, where the liquid is removed, leaving behind a compacted powder structure.
-
Advantages of Pressureless Compaction:
- Complex Shapes: Pressureless compaction is suitable for producing intricate shapes that might be difficult to achieve with traditional pressing methods.
- Cost-Effective: It eliminates the need for expensive high-pressure equipment, reducing overall production costs.
- Minimal Equipment Wear: Without the need for high-pressure machinery, there is less wear and tear on equipment, leading to lower maintenance costs.
-
Challenges and Considerations:
- Density Control: Achieving uniform density can be challenging, as it heavily depends on the particle size distribution and the effectiveness of the compaction technique.
- Material Limitations: Not all materials are suitable for pressureless compaction, especially those with poor packing characteristics or those that require high densities for specific applications.
- Process Optimization: Careful optimization of parameters such as vibration frequency, sintering temperature, and slurry composition is necessary to achieve the desired results.
-
Applications of Pressureless Compaction:
- Pressureless compaction is widely used in industries where complex shapes and cost-effective production are essential, such as in the manufacturing of ceramic components, metal filters, and certain types of bearings.
- It is also used in research and development for prototyping new materials and shapes without the need for expensive tooling.
In summary, pressureless compaction is a versatile and cost-effective method for forming dense agglomerates from metal powder particles. By leveraging natural packing mechanisms and carefully controlling particle size distribution, it offers a viable alternative to traditional high-pressure compaction methods, particularly for complex shapes and cost-sensitive applications.
Summary Table:
Aspect | Details |
---|---|
Definition | Forms dense agglomerates without external pressure. |
Key Techniques | Loose powder sintering, vibratory compacting, slip casting. |
Advantages | Produces complex shapes, cost-effective, minimal equipment wear. |
Challenges | Density control, material limitations, process optimization. |
Applications | Ceramic components, metal filters, bearings, R&D prototyping. |
Learn how pressureless compaction can revolutionize your production process—contact us today!