Vacuum mold casting, a specialized process within vacuum-based manufacturing, is primarily used in industries requiring high-precision, high-performance components. This method involves creating molds under vacuum conditions to eliminate air and impurities, ensuring superior material quality and structural integrity. Its applications span industries such as aerospace, automotive, medical, and energy, where the demand for high-purity, durable, and complex components is critical. The process is particularly beneficial for producing parts with intricate geometries, enhanced mechanical properties, and resistance to extreme conditions. Below, we explore the key applications and benefits of vacuum mold casting in detail.
Key Points Explained:
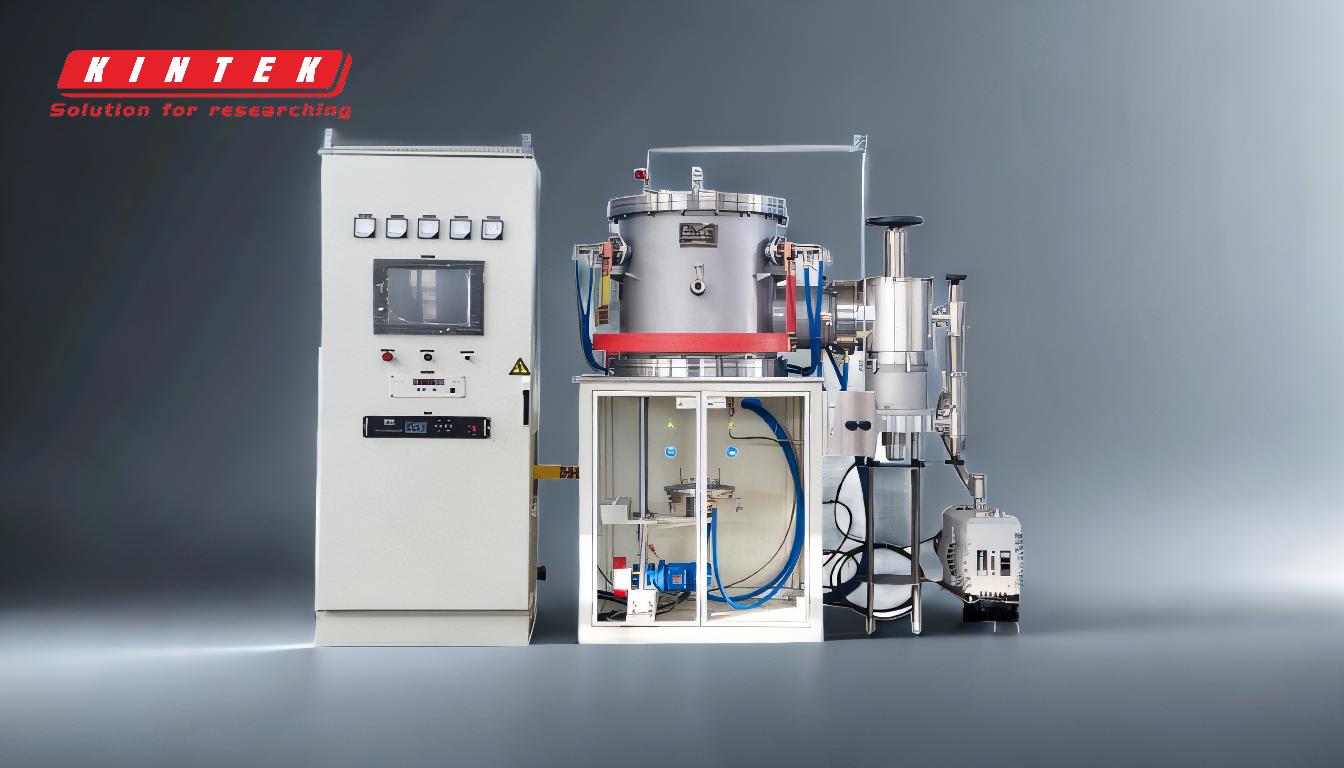
-
Aerospace Industry Applications
- High-Performance Components: Vacuum mold casting is extensively used to manufacture critical aerospace components such as turbine blades, engine parts, and structural elements. These parts must withstand extreme temperatures, pressures, and mechanical stresses.
- Material Purity: The vacuum environment ensures minimal contamination, which is crucial for materials like titanium and high-temperature alloys used in aerospace applications.
- Complex Geometries: The process allows for the creation of intricate shapes and thin-walled structures, which are often required in aerospace design.
-
Automotive Industry Applications
- Lightweight Components: Vacuum mold casting is employed to produce lightweight yet durable parts, such as engine components, transmission parts, and suspension systems. This contributes to improved fuel efficiency and performance.
- High-Strength Materials: The process is ideal for casting high-strength alloys, which are essential for safety-critical automotive parts.
- Precision and Consistency: The vacuum environment ensures uniform material properties and reduces defects, leading to higher reliability in automotive applications.
-
Medical and Pharmaceutical Industry Applications
- Biocompatible Materials: Vacuum mold casting is used to produce medical implants, surgical instruments, and pharmaceutical equipment from biocompatible materials like titanium and stainless steel.
- Sterility and Cleanliness: The vacuum environment minimizes contamination, ensuring that medical components meet stringent hygiene and safety standards.
- Customization: The process enables the production of patient-specific implants and devices with precise dimensions and tailored properties.
-
Energy and Power Generation Applications
- Turbine Components: Vacuum mold casting is utilized to manufacture turbine blades and other components for power generation systems, including nuclear, wind, and gas turbines.
- High-Temperature Alloys: The process is ideal for casting materials that can withstand extreme thermal and mechanical stresses in energy applications.
- Corrosion Resistance: The vacuum environment enhances the corrosion resistance of materials, which is critical for components exposed to harsh operating conditions.
-
Tool and Die Industry Applications
- Durable Tooling: Vacuum mold casting is used to produce molds, dies, and tooling with superior wear resistance and longevity.
- High Precision: The process ensures tight tolerances and smooth surface finishes, which are essential for high-quality tooling.
- Complex Designs: It allows for the creation of intricate tooling geometries that are difficult to achieve with conventional methods.
-
Research and Development Applications
- Material Innovation: Vacuum mold casting plays a key role in developing new materials and alloys for advanced applications.
- Prototyping: The process is used to create prototypes with high accuracy and material integrity, enabling faster development cycles.
- Custom Solutions: Researchers leverage vacuum mold casting to produce specialized components for experimental setups and testing.
-
Advantages of Vacuum Mold Casting
- Superior Material Properties: The vacuum environment eliminates impurities and oxidation, resulting in materials with enhanced mechanical and thermal properties.
- Reduced Defects: The process minimizes porosity, inclusions, and other defects, leading to higher-quality components.
- Versatility: It can be used with a wide range of materials, including titanium, nickel-based alloys, and refractory metals.
- Sustainability: The process reduces material waste and energy consumption compared to traditional casting methods.
-
Future Trends and Developments
- Advanced Alloys: Ongoing research is focused on developing new alloys specifically tailored for vacuum mold casting applications.
- Automation and Digitalization: The integration of automation and digital technologies is expected to improve process efficiency and consistency.
- Expanding Applications: As industries demand higher performance and reliability, the use of vacuum mold casting is likely to expand into new sectors and applications.
In summary, vacuum mold casting is a versatile and highly effective manufacturing process with applications across multiple high-performance industries. Its ability to produce high-purity, durable, and complex components makes it indispensable in fields such as aerospace, automotive, medical, and energy. As technology advances, the process is expected to play an even greater role in meeting the growing demands for precision, reliability, and innovation in manufacturing.
Summary Table:
Industry | Key Applications | Benefits |
---|---|---|
Aerospace | Turbine blades, engine parts, structural elements | High-performance, material purity, complex geometries |
Automotive | Engine components, transmission parts, suspension systems | Lightweight, high-strength materials, precision and consistency |
Medical & Pharmaceutical | Medical implants, surgical instruments, pharmaceutical equipment | Biocompatibility, sterility, customization |
Energy & Power | Turbine components for nuclear, wind, and gas systems | High-temperature alloys, corrosion resistance |
Tool & Die | Molds, dies, tooling | Durability, high precision, complex designs |
Research & Development | Material innovation, prototyping, custom solutions | Enhanced material properties, reduced defects, sustainability |
Unlock the potential of vacuum mold casting for your industry—contact our experts today!