The arc melting method is a process used in metallurgy to melt metals using an electric arc, which is a high-temperature plasma generated by an electrical discharge. This method is commonly employed in industries such as steelmaking, where it is used to melt scrap steel and other metals without altering their chemical properties. The arc is created between an electrode and the material to be melted, or between two electrodes, and the intense heat generated by the arc melts the metal. The process is efficient and allows for precise control over the melting process, making it suitable for producing high-quality metals and alloys.
Key Points Explained:
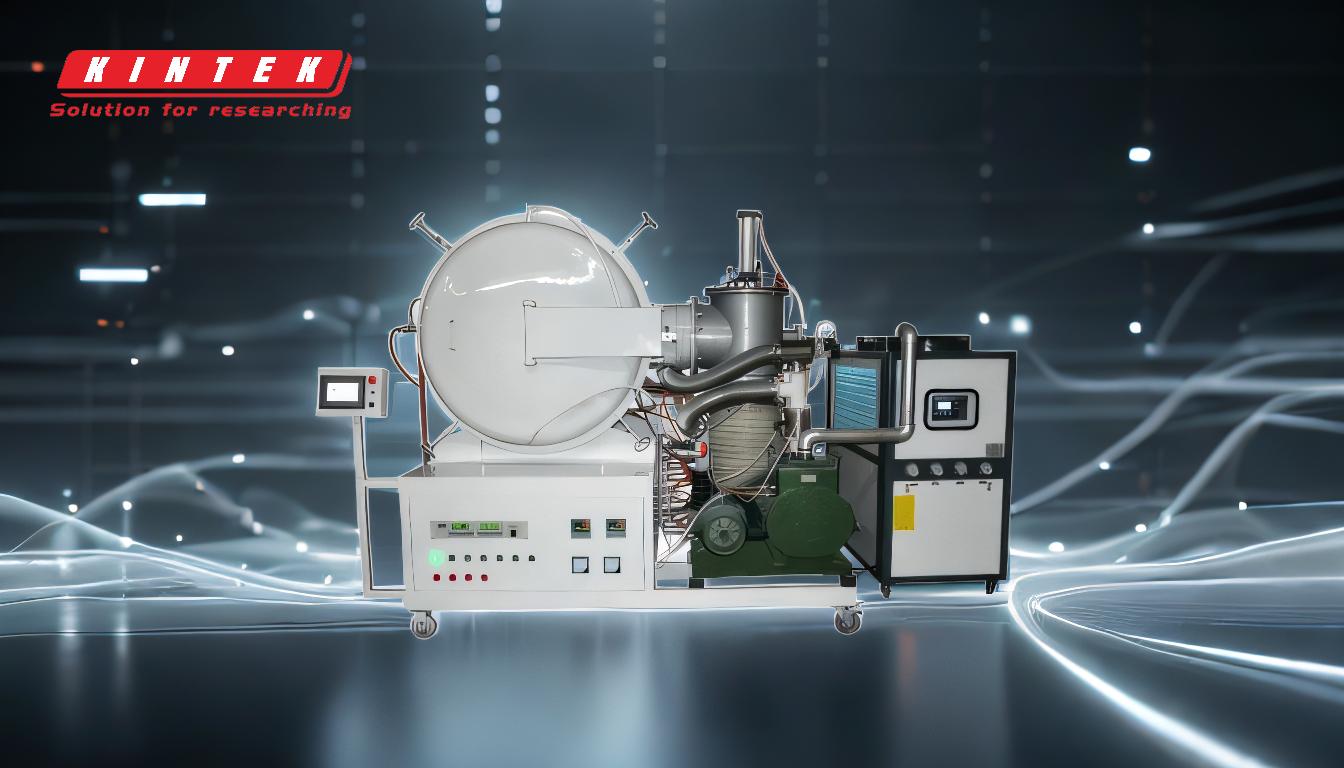
-
Definition of Arc Melting:
- Arc melting is an electrothermal metallurgical method that uses electric energy to generate an electric arc. This arc is created either between an electrode and the material to be melted or between two electrodes. The high temperatures produced by the arc are sufficient to melt metals, making this method highly effective for metallurgical applications.
-
Components of an Arc Melting Furnace:
- The primary component of an arc melting furnace is the electric welder, which converts standard electrical voltages (220V or 380V) into low voltage and high current. This conversion is crucial for generating the intense heat required to create and sustain the electric arc.
- The furnace also includes electrodes, which are used to create the arc, and a crucible or chamber where the material to be melted is placed.
-
How the Arc is Generated:
- The arc is triggered by an instantaneous short circuit between the positive and negative poles of the electrode(s). This short circuit creates a discharge of electricity, which ionizes the air or gas between the electrodes, forming a plasma arc.
- Once the arc is established, it becomes a self-sustaining discharge phenomenon. This means that the arc continues to burn stably without the need for continuous external intervention, as long as the electrical current is maintained.
-
Applications of Arc Melting:
- Arc melting is widely used in the steel industry for melting scrap steel. The method is particularly advantageous because it does not alter the chemical properties of the metal, allowing for the recycling of scrap materials without compromising their quality.
- It is also used in the production of high-purity metals and alloys, such as stainless steel, where precise control over the melting process is essential.
-
Advantages of Arc Melting:
- High Efficiency: The electric arc generates extremely high temperatures, allowing for rapid and efficient melting of metals.
- Precision Control: The process can be finely controlled, enabling the production of metals with specific properties and compositions.
- Versatility: Arc melting can be used with a wide range of metals and alloys, making it a versatile method in metallurgy.
- Recycling Capability: The method is ideal for recycling scrap metals, as it does not alter their chemical properties, ensuring that the recycled material retains its original quality.
-
Comparison with Other Melting Methods:
- Electric Arc Furnace (EAF) vs. Induction Furnace (IF): While both methods are used for melting metals, the EAF uses an electric arc to generate heat, whereas the IF uses electromagnetic induction. The EAF is generally more suitable for larger-scale operations and can handle a wider variety of materials.
- Vacuum Induction Melting (VIM): VIM is used for melting high-purity metals and alloys in a vacuum environment, which prevents contamination. While VIM offers superior purity, it is more complex and expensive than arc melting, making arc melting a more practical choice for many industrial applications.
-
Operational Considerations:
- Energy Consumption: Arc melting furnaces require a significant amount of electrical energy to generate and sustain the arc. Therefore, energy efficiency is an important consideration in the design and operation of these furnaces.
- Maintenance: The electrodes and other components of the furnace are subject to wear and tear due to the high temperatures and electrical currents involved. Regular maintenance is necessary to ensure the longevity and efficiency of the furnace.
- Safety: The high temperatures and electrical currents used in arc melting pose safety risks, including the risk of electrical shock and burns. Proper safety protocols and equipment are essential to protect workers and ensure safe operation.
In summary, the arc melting method is a highly effective and versatile technique for melting metals, particularly in the steel industry. It offers several advantages, including high efficiency, precise control, and the ability to recycle scrap metals without altering their chemical properties. However, it also requires careful consideration of energy consumption, maintenance, and safety to ensure optimal performance and safe operation.
Summary Table:
Aspect | Details |
---|---|
Definition | Electrothermal method using electric arcs to melt metals. |
Key Components | Electric welder, electrodes, crucible/chamber. |
Arc Generation | Created by short circuit between electrodes, forming a self-sustaining arc. |
Applications | Steelmaking, recycling scrap metals, producing high-purity alloys. |
Advantages | High efficiency, precision control, versatility, recycling capability. |
Comparison | More suitable for large-scale operations compared to induction furnaces. |
Operational Factors | Energy consumption, maintenance, safety protocols. |
Discover how the arc melting method can enhance your metallurgical processes—contact our experts today for more information!