The critical temperature in heat treatment refers to the specific temperature range at which a material undergoes a significant structural or phase transformation, influencing its mechanical properties. This temperature is crucial because it determines the effectiveness of the heat treatment process in achieving desired outcomes such as hardness, strength, or ductility. The critical temperature varies depending on the material and the specific heat treatment process being applied, such as annealing, quenching, or tempering. Understanding and controlling this temperature is essential for ensuring uniform temperature distribution, proper gas circulation, and optimal cycle times, which collectively impact the final product quality.
Key Points Explained:
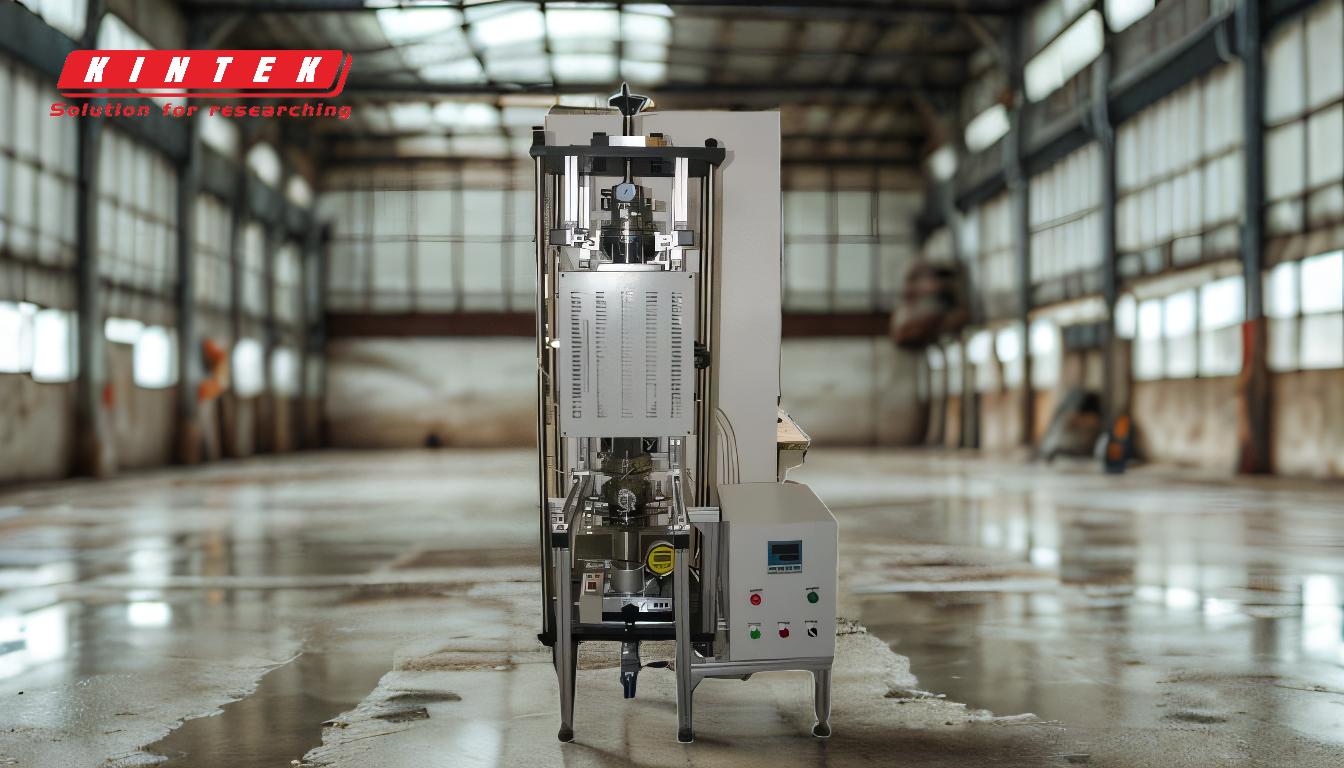
-
Definition of Critical Temperature in Heat Treatment:
- The critical temperature is the specific temperature range at which a material experiences a phase transformation or structural change during heat treatment.
- This temperature is material-specific and depends on the alloy composition and the desired properties.
-
Importance of Critical Temperature:
- Determines the success of the heat treatment process in achieving the desired mechanical properties (e.g., hardness, strength, ductility).
- Ensures uniform temperature distribution throughout the hot zone, which is essential for consistent results.
- Influences the gas circulation and cooling rates, which are critical for achieving the desired microstructure.
-
Factors Influencing Critical Temperature:
- Material Type: Different metals and alloys have unique critical temperatures. For example, steel has a critical temperature range for austenitization, typically between 700°C and 900°C.
- Heat Treatment Process: The critical temperature varies depending on whether the process is annealing, quenching, tempering, or case hardening.
- End Application: The properties required for the final product (e.g., wear resistance, toughness) dictate the critical temperature range.
-
Variables in Heat Treatment:
- Temperature: The critical temperature must be accurately controlled to ensure the material reaches the desired phase.
- Time: The duration the material is held at the critical temperature affects the extent of the transformation.
- Cooling Rate: The method and rate of cooling (e.g., air cooling, oil quenching) determine the final microstructure and properties.
-
Practical Considerations:
- Uniform Temperature Distribution: Ensuring the entire part reaches the critical temperature uniformly is vital for consistent results.
- Gas Circulation: Proper gas flow (e.g., inert gas or quench gas) helps maintain the desired atmosphere and cooling rates.
- Cycle Times: Optimizing heating and cooling cycles minimizes energy consumption and reduces the risk of defects.
-
Examples of Critical Temperatures in Common Materials:
- Steel: The critical temperature for austenitization is typically between 700°C and 900°C, depending on the carbon content.
- Aluminum Alloys: Critical temperatures vary based on the alloy, but they generally range from 400°C to 500°C for solution heat treatment.
- Titanium Alloys: Critical temperatures for heat treatment are usually between 700°C and 1000°C, depending on the alloy and desired properties.
-
Challenges and Solutions:
- Temperature Control: Precise control is necessary to avoid overheating or underheating, which can lead to defects.
- Material Variability: Variations in material composition can affect the critical temperature, requiring adjustments in the heat treatment process.
- Equipment Maintenance: Anticipating and addressing potential equipment issues can prevent downtime and ensure consistent results.
In summary, the critical temperature in heat treatment is a fundamental parameter that dictates the success of the process. It varies depending on the material, desired properties, and specific heat treatment method. Accurate control of this temperature, along with proper gas circulation and cycle times, ensures high-quality outcomes and minimizes the risk of defects. Understanding these factors is essential for equipment and consumable purchasers to select the right materials and processes for their applications.
Summary Table:
Aspect | Details |
---|---|
Definition | Temperature range for phase transformation during heat treatment. |
Importance | Determines mechanical properties like hardness, strength, and ductility. |
Factors Influencing | Material type, heat treatment process, and end application. |
Variables | Temperature, time, and cooling rate. |
Practical Considerations | Uniform temperature distribution, gas circulation, and cycle times. |
Examples | Steel: 700°C–900°C, Aluminum: 400°C–500°C, Titanium: 700°C–1000°C. |
Challenges | Temperature control, material variability, and equipment maintenance. |
Optimize your heat treatment process with expert guidance—contact us today!