The cooling rate in casting significantly impacts the microstructure, mechanical properties, and overall quality of the final product. A faster cooling rate typically results in finer grain structures, increased strength, and improved hardness, but it can also lead to higher internal stresses and potential cracking. Conversely, slower cooling rates produce coarser grains, reduced strength, and lower hardness but minimize internal stresses and improve ductility. The cooling rate must be carefully controlled to achieve the desired balance between mechanical properties and defect minimization, depending on the specific application and material used.
Key Points Explained:
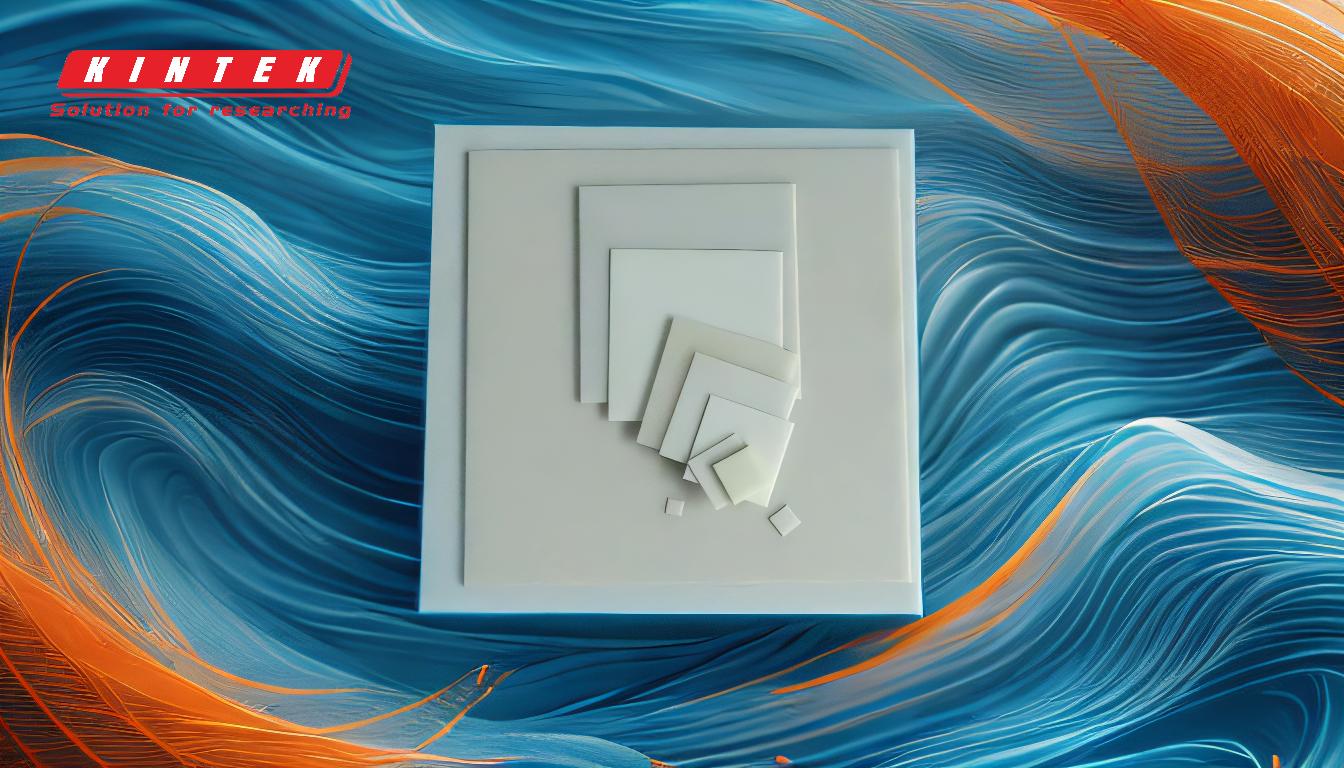
-
Influence on Microstructure:
- Faster cooling rates lead to finer grain structures due to rapid solidification, which limits the time available for grain growth.
- Slower cooling rates allow for larger grain formation as the material has more time to solidify and grow.
- The microstructure directly affects properties like strength, ductility, and toughness.
-
Mechanical Properties:
- Strength and Hardness: Faster cooling rates generally increase strength and hardness due to the finer grain structure and potential formation of harder phases (e.g., martensite in steel).
- Ductility and Toughness: Slower cooling rates enhance ductility and toughness by reducing internal stresses and allowing for more uniform grain growth.
- Residual Stresses: Rapid cooling can introduce residual stresses, which may lead to warping or cracking, especially in complex geometries.
-
Defect Formation:
- Porosity: Faster cooling can trap gases, leading to porosity, while slower cooling allows gases to escape, reducing porosity.
- Cracking: High cooling rates increase the risk of thermal cracking due to uneven contraction and internal stresses.
- Shrinkage Defects: Slower cooling minimizes shrinkage defects by allowing the material to solidify more uniformly.
-
Material-Specific Effects:
- Steel and Iron: Cooling rate affects phase transformations (e.g., austenite to pearlite, bainite, or martensite), influencing hardness and strength.
- Aluminum Alloys: Faster cooling can refine grain size and improve mechanical properties, but it may also increase susceptibility to hot tearing.
- Titanium Alloys: Controlled cooling is critical to avoid undesirable phase formations and ensure optimal mechanical properties.
-
Process Optimization:
- Cooling Rate Control: Techniques like water quenching, air cooling, or controlled furnace cooling are used to achieve the desired cooling rate.
- Mold Design: The choice of mold material (e.g., sand, metal) and design (e.g., chills, risers) influences the cooling rate.
- Post-Casting Treatments: Heat treatments like annealing or tempering can mitigate the effects of rapid cooling and improve material properties.
-
Application-Specific Considerations:
- High-Strength Components: Faster cooling is preferred for parts requiring high strength and wear resistance.
- Complex Geometries: Slower cooling is often necessary to avoid cracking and ensure dimensional accuracy.
- Cost and Efficiency: Balancing cooling rate with production speed and energy consumption is crucial for cost-effective manufacturing.
By understanding and controlling the cooling rate, manufacturers can tailor the casting process to meet specific performance requirements and minimize defects, ensuring high-quality cast components.
Summary Table:
Aspect | Faster Cooling Rate | Slower Cooling Rate |
---|---|---|
Microstructure | Finer grain structure | Coarser grain structure |
Strength & Hardness | Increased | Reduced |
Ductility & Toughness | Lower | Higher |
Residual Stresses | Higher risk of cracking | Minimized |
Porosity | Higher risk due to trapped gases | Reduced |
Applications | High-strength components | Complex geometries |
Need help optimizing your casting process? Contact our experts today for tailored solutions!