A burnout furnace, also known as a burnout oven, is primarily used in metal casting and dental restoration processes to eliminate wax or resin patterns from molds. In metal casting, it rapidly heats the mold to remove wax, ensuring efficient and clean mold preparation for molten metal. In dental applications, it is used for dewaxing and heat treatment of 3D-printed restorations. The furnace ensures precise temperature control, which is critical for achieving high-quality results. Its function is essential in industries requiring intricate mold preparation and material sintering, such as jewelry making, dental labs, and metal injection molding.
Key Points Explained:
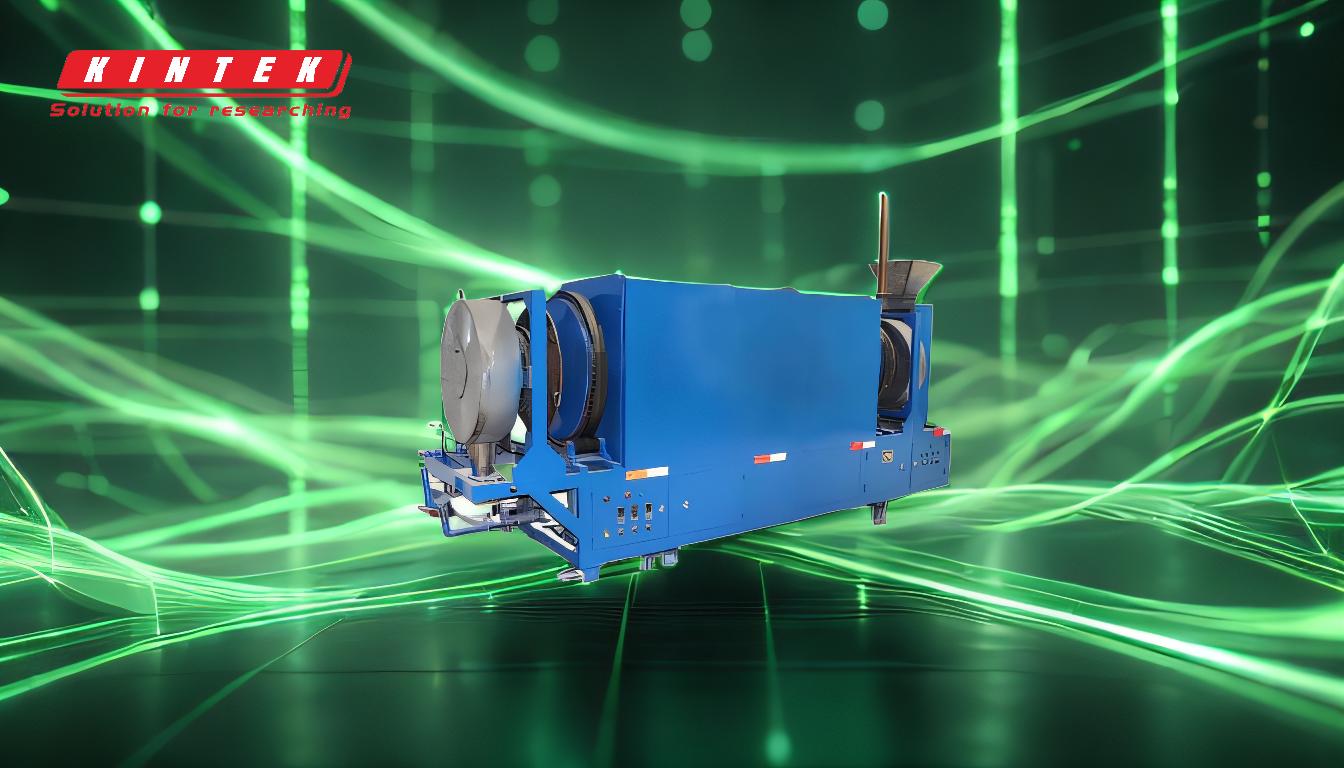
-
Primary Function of a Burnout Furnace:
- The burnout furnace is designed to remove wax or resin patterns from molds through controlled heating. This process is crucial in industries like metal casting and dental restoration, where wax or resin is used to create intricate molds.
- In metal casting, the furnace accelerates the wax burnout process by quickly raising the temperature to eliminate wax from the mold. This rapid heating ensures efficient wax elimination, allowing for faster turnaround times in metal casting procedures.
-
Applications in Metal Casting:
- Burnout furnaces are widely used in jewelry making and industrial metal casting. They prepare molds by burning out wax patterns, leaving behind a clean cavity for molten metal.
- The precise temperature control ensures that the wax is completely removed without damaging the mold, which is critical for producing high-quality castings.
-
Dental Restoration Applications:
- In dental labs, burnout furnaces are used for dewaxing and heat treatment of 3D-printed restorations, such as crowns, bridges, and frameworks. This process ensures that the final dental prosthetics are free of residual wax and have the necessary structural integrity.
- The furnace is also used in conjunction with sintering furnaces to process zirconia and other dental materials, ensuring they reach their final hardness and density.
-
Temperature Control and Precision:
- Burnout furnaces are equipped with advanced temperature control systems to ensure precise heating profiles. This is essential for achieving consistent results in both metal casting and dental applications.
- The ability to control heating and cooling rates prevents thermal shock, which can damage molds or restorations.
-
Integration with Sintering Processes:
- In some applications, burnout furnaces work in tandem with sintering furnaces. For example, in metal injection molding (MIM), the burnout furnace removes the binder material, while the sintering furnace densifies the metal parts.
- This integration ensures a seamless transition from debinding to sintering, improving the overall efficiency of the manufacturing process.
-
Safety Features:
- Given the high temperatures involved, burnout furnaces are designed with safety features such as over-temperature protection, ventilation systems, and robust insulation. These features ensure safe operation and prevent accidents in industrial and dental settings.
-
Versatility in Material Processing:
- Burnout furnaces can handle a variety of materials, including wax, resin, and binder materials used in metal injection molding. This versatility makes them indispensable in industries requiring precise mold preparation and material processing.
-
Comparison with Sintering Furnaces:
- While burnout furnaces focus on removing wax or resin, sintering furnaces are used to densify and strengthen materials by heating them below their melting point. Both types of furnaces are often used in sequence to achieve the desired final product.
By understanding the function and applications of burnout furnaces, purchasers can make informed decisions about the equipment needed for their specific processes, whether in metal casting, dental restoration, or other industries requiring precise thermal processing.
Summary Table:
Function | Applications | Key Features |
---|---|---|
Removes wax or resin patterns | Metal casting (jewelry, industrial), dental restoration (crowns, bridges) | Precise temperature control, rapid heating, safety features |
Prepares molds for molten metal | Used in conjunction with sintering furnaces for metal injection molding (MIM) | Advanced temperature profiles, prevents thermal shock |
Dewaxing and heat treatment | Processes 3D-printed dental restorations, zirconia, and other materials | Versatile material handling, integration with sintering processes |
Discover how a burnout furnace can optimize your metal casting or dental lab processes—contact us today for expert advice!