Chemical vapor infiltration (CVI) is a specialized variant of chemical vapor deposition (CVD) used to deposit materials within porous substrates, such as fiber preforms, to create composite materials. The process involves the infiltration of gaseous reactants into the porous structure, where they undergo chemical reactions to form a solid deposit. This method is particularly useful for creating high-performance materials like ceramic matrix composites (CMCs). Below is a detailed explanation of the CVI process, its steps, and its significance.
Key Points Explained:
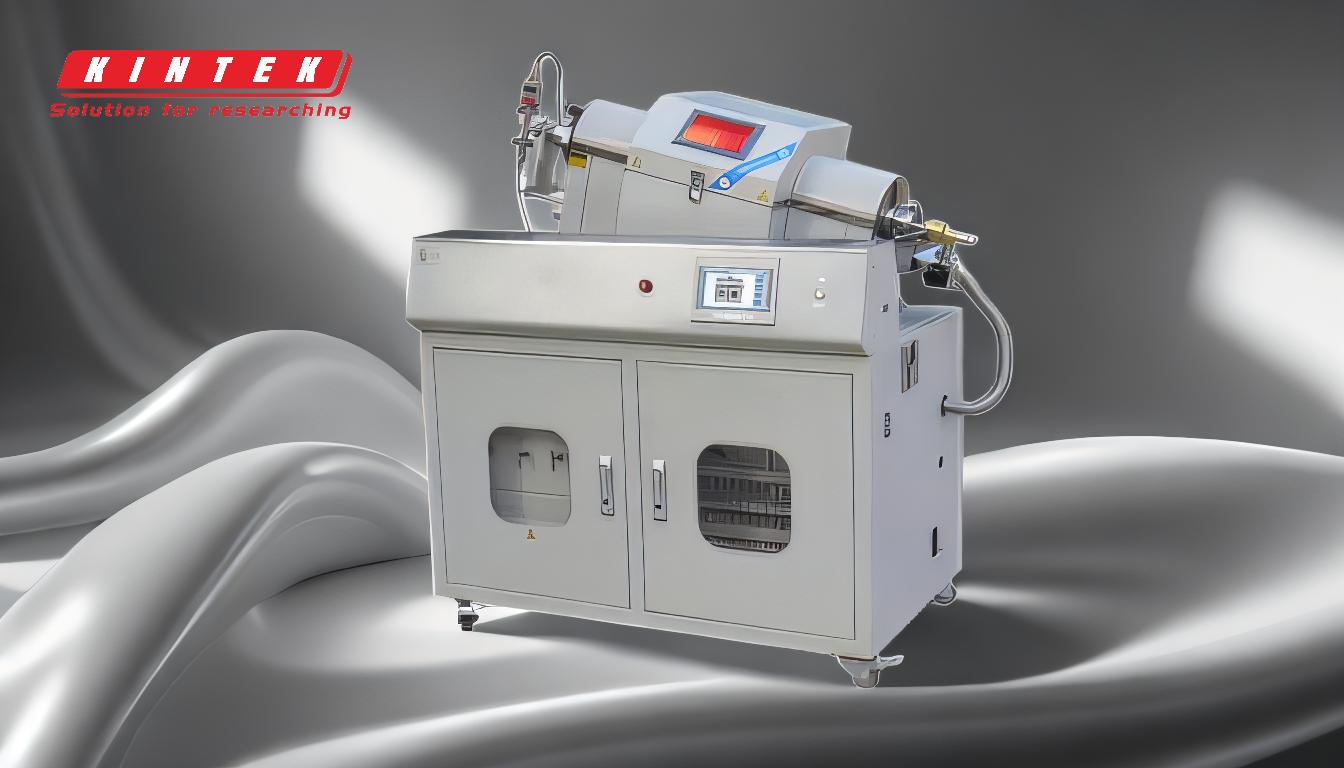
-
Introduction to Chemical Vapor Infiltration (CVI):
- CVI is a process derived from CVD, tailored for depositing materials within porous structures.
- It is widely used in the production of ceramic matrix composites, where a ceramic matrix is formed around reinforcing fibers.
- The process is advantageous for creating materials with high strength, thermal stability, and resistance to wear and corrosion.
-
Steps Involved in the CVI Process:
-
Transport of Gaseous Reactants:
- Gaseous precursors are introduced into a reaction chamber containing the porous substrate.
- The gases diffuse into the pores of the substrate, driven by concentration gradients and pressure differences.
-
Adsorption on the Substrate Surface:
- The gaseous species adsorb onto the surface of the porous substrate.
- This step is crucial for ensuring that the reactants are in close proximity to the substrate for subsequent reactions.
-
Surface Reactions:
- The adsorbed species undergo chemical reactions on the substrate surface, often catalyzed by the substrate material.
- These reactions result in the formation of solid deposits within the pores.
-
Nucleation and Growth:
- The solid deposits nucleate and grow, gradually filling the pores of the substrate.
- The growth rate is influenced by factors such as temperature, pressure, and the concentration of reactants.
-
Desorption and Removal of By-products:
- Gaseous by-products of the reactions are desorbed from the surface and transported out of the porous structure.
- Efficient removal of by-products is essential to prevent clogging of the pores and ensure uniform infiltration.
-
Transport of Gaseous Reactants:
-
Factors Influencing the CVI Process:
-
Temperature:
- The temperature must be carefully controlled to ensure that the reactions occur at an optimal rate without damaging the substrate.
-
Pressure:
- Pressure affects the diffusion of gases into the pores and the rate of chemical reactions.
-
Gas Composition:
- The composition of the reactant gases determines the type of deposit formed and the rate of infiltration.
-
Substrate Porosity:
- The size and distribution of pores in the substrate influence the depth and uniformity of infiltration.
-
Temperature:
-
Applications of CVI:
-
Ceramic Matrix Composites (CMCs):
- CVI is extensively used to produce CMCs, which are used in aerospace, automotive, and energy industries due to their high strength and thermal resistance.
-
Carbon-Carbon Composites:
- CVI is used to create carbon-carbon composites, which are employed in high-temperature applications such as brake discs and rocket nozzles.
-
Other Advanced Materials:
- The process is also used to create other advanced materials, including silicon carbide composites and coatings for various industrial applications.
-
Ceramic Matrix Composites (CMCs):
-
Advantages of CVI:
-
Uniform Infiltration:
- CVI allows for the uniform infiltration of complex shapes and intricate geometries.
-
High Purity Deposits:
- The process results in high-purity deposits with excellent mechanical properties.
-
Low Stress Formation:
- The gradual deposition process minimizes residual stresses in the final composite material.
-
Uniform Infiltration:
-
Challenges and Limitations:
-
Slow Process:
- CVI can be a slow process, especially for thick or dense composites, due to the time required for gas diffusion and reaction.
-
Cost:
- The process can be expensive due to the need for specialized equipment and high-purity gases.
-
Control of Process Parameters:
- Precise control of temperature, pressure, and gas composition is required to achieve optimal results, which can be challenging.
-
Slow Process:
In summary, chemical vapor infiltration is a sophisticated process used to create high-performance composite materials by depositing solid materials within porous substrates. The process involves several key steps, including the transport of gaseous reactants, adsorption, surface reactions, nucleation, and growth, followed by the removal of by-products. While CVI offers numerous advantages, such as uniform infiltration and high-purity deposits, it also presents challenges related to process speed, cost, and control. Despite these challenges, CVI remains a critical technology in the production of advanced materials for demanding applications.
Summary Table:
Aspect | Details |
---|---|
Process Overview | Infiltration of gaseous reactants into porous substrates to form solid deposits. |
Key Steps | 1. Transport of gaseous reactants. 2. Adsorption. 3. Surface reactions. 4. Nucleation & growth. 5. Desorption of by-products. |
Influencing Factors | Temperature, pressure, gas composition, and substrate porosity. |
Applications | Ceramic matrix composites (CMCs), carbon-carbon composites, and other advanced materials. |
Advantages | Uniform infiltration, high-purity deposits, and low stress formation. |
Challenges | Slow process, high cost, and precise control of parameters required. |
Discover how chemical vapor infiltration can revolutionize your material production—contact our experts today!