Oxygen plays a critical role in brazing, primarily in the context of its absence rather than its presence. In brazing, the goal is to create strong, reliable joints by ensuring the filler metal bonds effectively to the base metal. This requires clean, oxide-free surfaces, as oxides can prevent proper bonding and flow of the filler metal. Oxygen, when present in the brazing environment, can lead to oxidation, which is detrimental to the process. Therefore, controlling or eliminating oxygen is essential to maintain an oxide-free environment, ensuring successful brazing. This is achieved through the use of controlled atmospheres, such as hydrogen or inert gases, which prevent oxidation and promote the formation of high-quality brazed joints.
Key Points Explained:
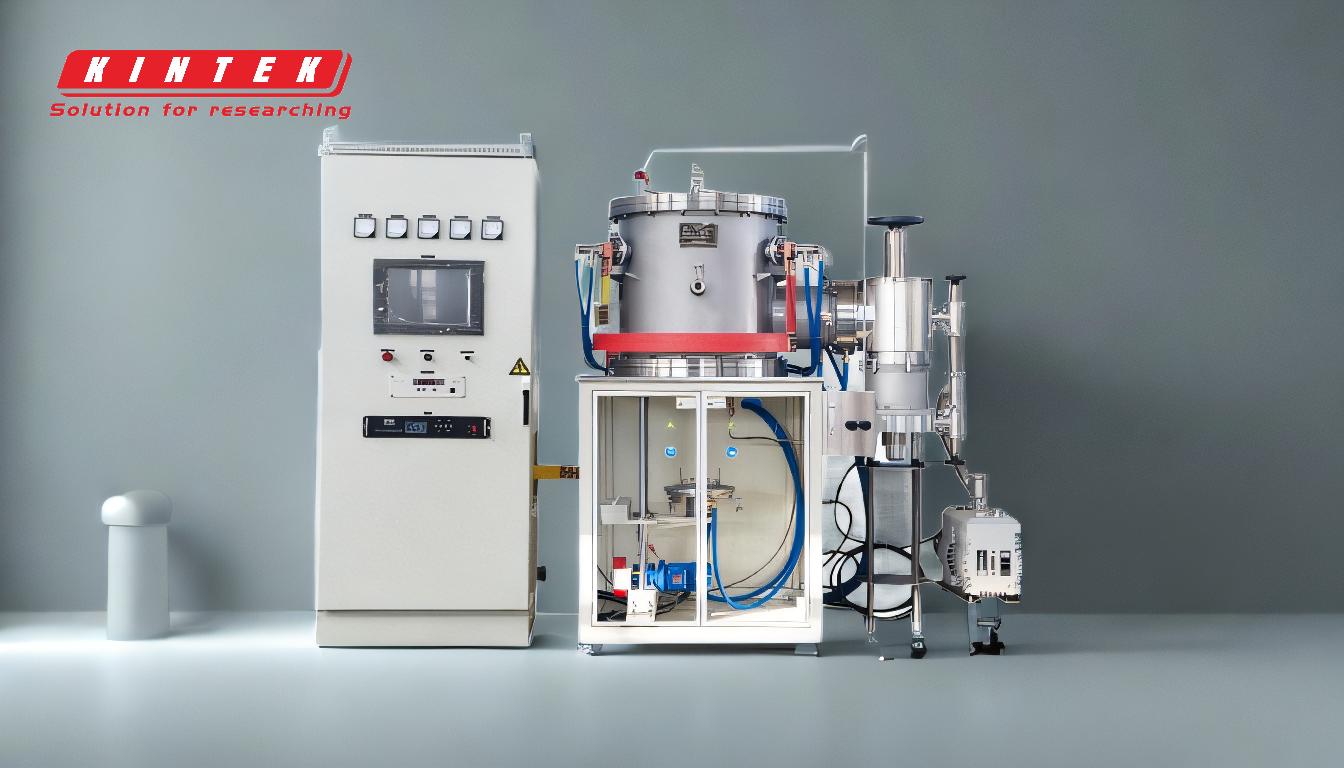
-
Role of Oxygen in Brazing:
- Oxygen is generally undesirable in the brazing process because it leads to oxidation of the metal surfaces.
- Oxidation forms a layer of oxides on the metal surfaces, which can prevent the filler metal from bonding properly and flowing uniformly.
- Clean, oxide-free surfaces are essential for achieving strong and reliable brazed joints.
-
Preventing Oxide Formation:
- Oxide-free surfaces are critical for successful brazing, as oxides can interfere with the capillary action required for the filler metal to flow and bond.
- The presence of oxygen in the brazing environment must be minimized or eliminated to prevent the formation of oxides.
- This is often achieved by using controlled atmospheres, such as hydrogen or inert gases, which protect the metal surfaces from oxidation.
-
Hydrogen as a Brazing Flux:
- In processes like copper brazing, hydrogen gas is used as a brazing flux.
- Hydrogen not only protects the metal surfaces from oxidation but also removes existing oxides, ensuring a clean surface for brazing.
- This eliminates the need for additional flux materials, simplifying the brazing process and improving efficiency.
-
Importance of Gas Control:
- Maintaining the proper gas mixture is crucial in brazing to prevent oxidation, scaling, and carbon buildup.
- Precise control of the brazing atmosphere, whether through manual valves or advanced electronic flow control systems, ensures that the environment remains free of oxygen and other contaminants.
- Quality brazing suppliers prioritize gas control to achieve consistent and high-quality brazed joints.
-
Capillary Action and Surface Cleanliness:
- Uniform capillary action, which is essential for the filler metal to flow and bond properly, can only occur on clean, oxide-free surfaces.
- Any grease, oil, dirt, or oxides on the base metal or filler metal must be removed before brazing to ensure a successful joint.
- The absence of oxygen in the brazing environment helps maintain this cleanliness, promoting effective capillary action and strong joints.
In summary, oxygen is a critical factor in brazing, but its role is primarily negative. The presence of oxygen leads to oxidation, which can compromise the quality of brazed joints. Therefore, controlling or eliminating oxygen through the use of controlled atmospheres, such as hydrogen or inert gases, is essential to ensure clean, oxide-free surfaces and successful brazing.
Summary Table:
Key Aspect | Explanation |
---|---|
Role of Oxygen | Oxygen leads to oxidation, preventing proper bonding and flow of filler metal. |
Preventing Oxide Formation | Controlled atmospheres (e.g., hydrogen or inert gases) eliminate oxygen exposure. |
Hydrogen as Flux | Hydrogen removes oxides, ensuring clean surfaces and simplifying the process. |
Gas Control Importance | Precise gas control prevents oxidation, scaling, and ensures high-quality joints. |
Capillary Action | Clean, oxide-free surfaces are essential for uniform filler metal flow and bonding. |
Ensure strong, reliable brazed joints—contact our experts today for tailored solutions!