Uniaxial pressing of ceramics is a manufacturing process where ceramic powders are compacted into a desired shape using a single-axis press. This method involves applying pressure in one direction to form a dense, uniform ceramic body. The process is widely used in the production of ceramic components due to its simplicity, cost-effectiveness, and ability to produce parts with high dimensional accuracy. The key steps include preparing the ceramic powder, filling the die, applying pressure, and sintering the pressed part to achieve the final properties. Proper control of parameters such as pressure, time, and temperature is crucial to ensure the quality and integrity of the ceramic product.
Key Points Explained:
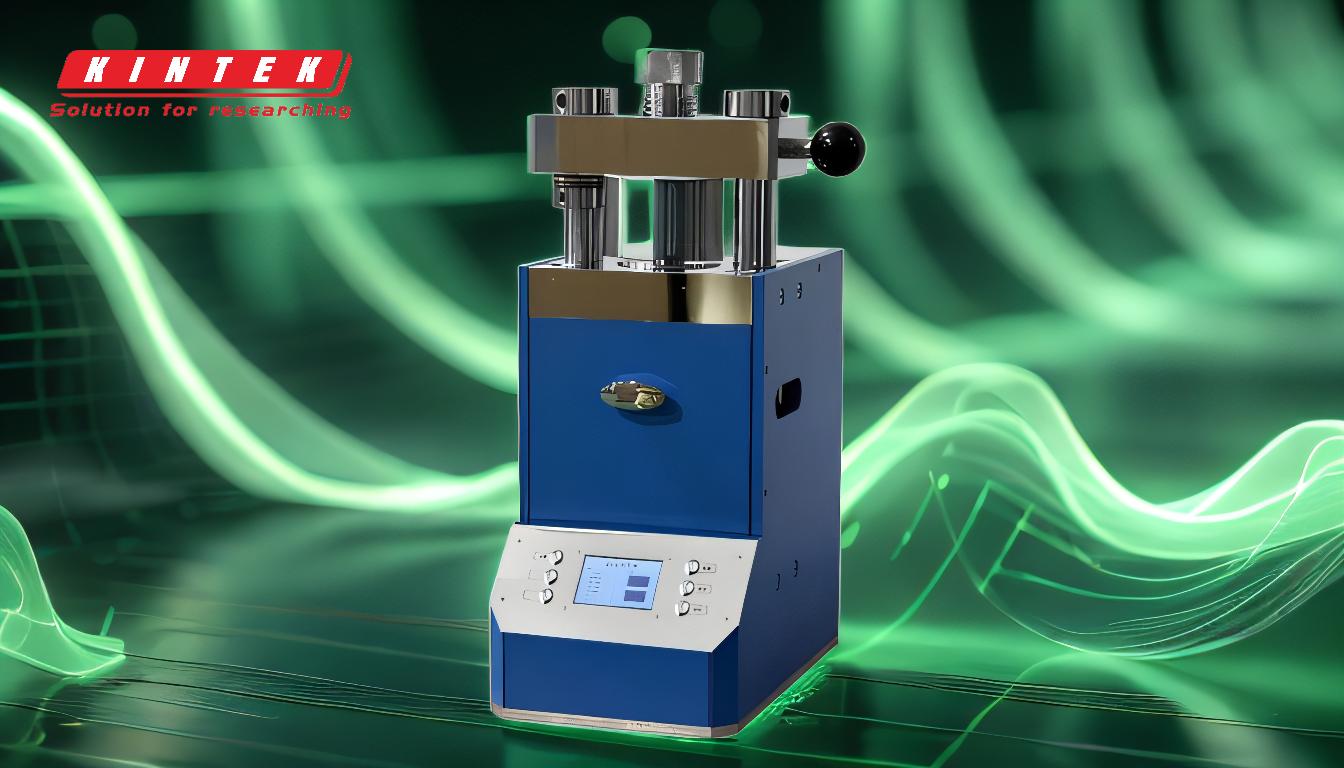
-
Preparation of Ceramic Powder:
- The ceramic powder is first prepared by mixing raw materials, often including binders and lubricants, to improve flowability and compaction. This step ensures that the powder can be evenly distributed in the die cavity.
-
Filling the Die:
- The prepared powder is then poured into a die, which is a mold that defines the shape of the final ceramic part. The die is typically made of hardened steel to withstand the high pressures used during pressing.
-
Application of Pressure:
- A uniaxial press applies pressure in a single direction, usually vertically, to compact the powder into a dense green body. The pressure can range from a few MPa to several hundred MPa, depending on the material and desired density. This step is critical for achieving the required mechanical properties and dimensional accuracy.
-
Ejection of the Green Body:
- After pressing, the green body (the compacted but unsintered ceramic part) is ejected from the die. Care must be taken to avoid cracking or deformation during this step.
-
Sintering:
- The green body is then sintered in a furnace at high temperatures to bond the particles together and achieve the final mechanical and thermal properties. Sintering also reduces porosity, increasing the density and strength of the ceramic part.
-
Importance of Burnout:
- If binders or lubricants were used in the powder preparation, a burnout step is necessary before sintering. This involves heating the green body to a temperature where the organic materials decompose and are removed, preventing defects during sintering.
-
Control of Time and Temperature:
- Both during pressing and sintering, careful control of time and temperature is essential. Incorrect parameters can lead to defects such as cracking, warping, or incomplete densification, which can compromise the performance of the final product.
-
Advantages of Uniaxial Pressing:
- Cost-Effectiveness: Uniaxial pressing is relatively simple and requires less complex equipment compared to other forming methods like isostatic pressing.
- High Dimensional Accuracy: The process allows for the production of parts with tight tolerances and consistent dimensions.
- Scalability: It is suitable for both small-scale and large-scale production, making it versatile for various applications.
-
Applications:
- Uniaxial pressing is used in the production of a wide range of ceramic products, including tiles, insulators, cutting tools, and electronic components. Its ability to produce complex shapes with high precision makes it a preferred method in many industries.
By following these steps and maintaining strict control over the process parameters, uniaxial pressing can produce high-quality ceramic components that meet the demanding requirements of various applications.
Summary Table:
Step | Description |
---|---|
Preparation of Powder | Mix raw materials with binders/lubricants for even distribution in the die. |
Filling the Die | Pour powder into a hardened steel die to define the part's shape. |
Applying Pressure | Compact powder vertically to form a dense green body. |
Ejection of Green Body | Carefully eject the unsintered part to avoid cracking or deformation. |
Sintering | Heat the green body to bond particles and achieve final properties. |
Burnout (if needed) | Remove organic materials before sintering to prevent defects. |
Control of Parameters | Monitor pressure, time, and temperature to ensure quality and integrity. |
Advantages | Cost-effectiveness, high dimensional accuracy, and scalability. |
Applications | Tiles, insulators, cutting tools, and electronic components. |
Discover how uniaxial pressing can optimize your ceramic production—contact our experts today!