Brazing is a critical process in metal joining, requiring careful attention to detail to ensure strong, durable, and defect-free joints. Precautions during brazing involve proper material preparation, temperature control, flux application, and post-braze cleaning. These steps help prevent oxidation, contamination, and weak joints. Additionally, safety measures, such as proper ventilation and protective equipment, are essential to protect operators from fumes and heat. By following these precautions, the brazing process can achieve high-quality results while minimizing risks.
Key Points Explained:
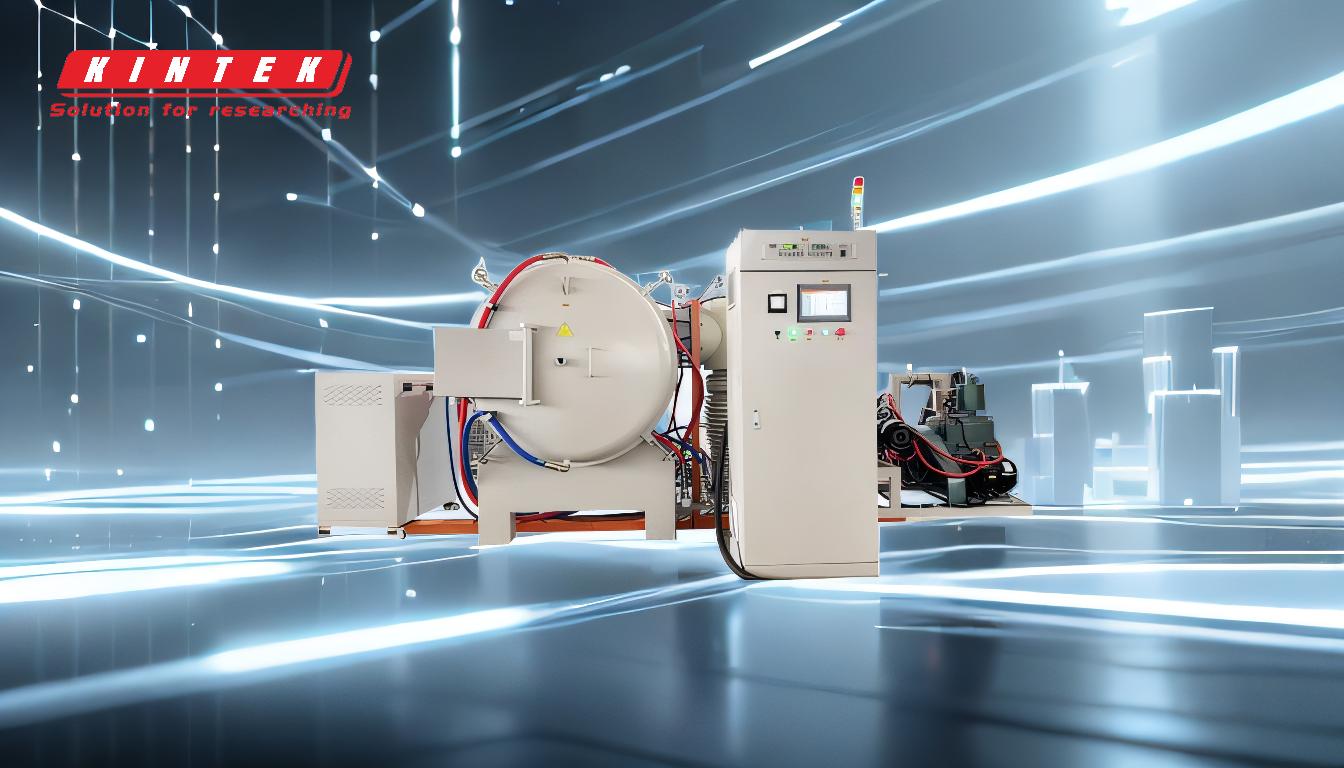
-
Material Preparation
- Clean the surfaces to be joined thoroughly to remove dirt, grease, and oxides. Contaminants can prevent proper bonding and weaken the joint.
- Use appropriate cleaning methods, such as degreasing solvents, wire brushing, or abrasives, depending on the material.
- Ensure proper fit-up of the parts to allow capillary action, which is essential for the filler metal to flow evenly into the joint.
-
Temperature Control
- Maintain precise temperature control during the brazing process. Overheating can damage the base metals, while insufficient heat may result in incomplete bonding.
- Use a calibrated thermometer or pyrometer to monitor the temperature accurately.
- Preheat the parts evenly to minimize thermal stress and ensure uniform heating.
-
Flux Application
- Apply flux to the joint area to prevent oxidation and promote wetting of the filler metal. Flux removes oxides and protects the surfaces during heating.
- Choose the right type of flux for the materials being joined. Some fluxes are designed for specific metals or temperature ranges.
- Avoid excessive flux, as it can lead to residue buildup and contamination.
-
Filler Metal Selection
- Select a filler metal that is compatible with the base metals and the intended application. Common filler metals include silver-based alloys, copper, and nickel-based alloys.
- Ensure the filler metal has the appropriate melting point and flow characteristics for the joint design.
-
Post-Braze Cleaning
- Remove any residual flux or oxide layers after brazing to prevent corrosion and improve the appearance of the joint.
- Use appropriate cleaning methods, such as water rinsing, chemical cleaning, or mechanical brushing, depending on the flux type.
-
Safety Precautions
- Work in a well-ventilated area or use fume extraction systems to avoid inhaling harmful fumes generated during brazing.
- Wear protective equipment, including gloves, safety glasses, and heat-resistant clothing, to protect against burns and splashes.
- Handle hot materials with care and allow them to cool before handling.
-
Joint Design and Fixturing
- Design the joint to maximize strength and ensure proper filler metal distribution. Common joint types include lap joints, butt joints, and T-joints.
- Use fixtures to hold the parts in place during brazing, ensuring alignment and preventing movement that could disrupt the joint.
-
Environmental Considerations
- Avoid brazing in areas with drafts or temperature fluctuations, as these can affect the heating process and lead to uneven joints.
- Control humidity levels, as moisture can interfere with flux performance and cause defects.
By adhering to these precautions, you can achieve high-quality brazed joints that meet performance and durability requirements. Proper preparation, temperature management, and safety measures are essential for successful brazing.
Summary Table:
Precaution | Key Steps |
---|---|
Material Preparation | Clean surfaces, ensure proper fit-up, and use appropriate cleaning methods. |
Temperature Control | Monitor temperature, preheat evenly, and avoid overheating or underheating. |
Flux Application | Apply the right flux type, avoid excess, and ensure proper coverage. |
Filler Metal Selection | Choose compatible filler metals with appropriate melting points. |
Post-Braze Cleaning | Remove residual flux and oxides to prevent corrosion. |
Safety Precautions | Use ventilation, wear protective gear, and handle hot materials carefully. |
Joint Design and Fixturing | Design joints for strength and use fixtures for alignment. |
Environmental Considerations | Avoid drafts, control humidity, and maintain stable conditions. |
Need expert advice on brazing? Contact us today to ensure flawless metal joining!