Horizontal furnaces are versatile thermal processing equipment widely used across various industries for heat treatment and material processing. They are particularly valued for their precise temperature control, uniform heating, and ability to handle large volumes of material efficiently. Key industries that utilize horizontal furnaces include aerospace, automotive, electronics manufacturing, materials science, metallurgy, ceramics, and battery manufacturing. These furnaces are employed in processes such as annealing, hardening, tempering, sintering, thermal analysis, and chemical vapor deposition. Their design makes them ideal for high-performance production environments, offering cost savings and low maintenance.
Key Points Explained:
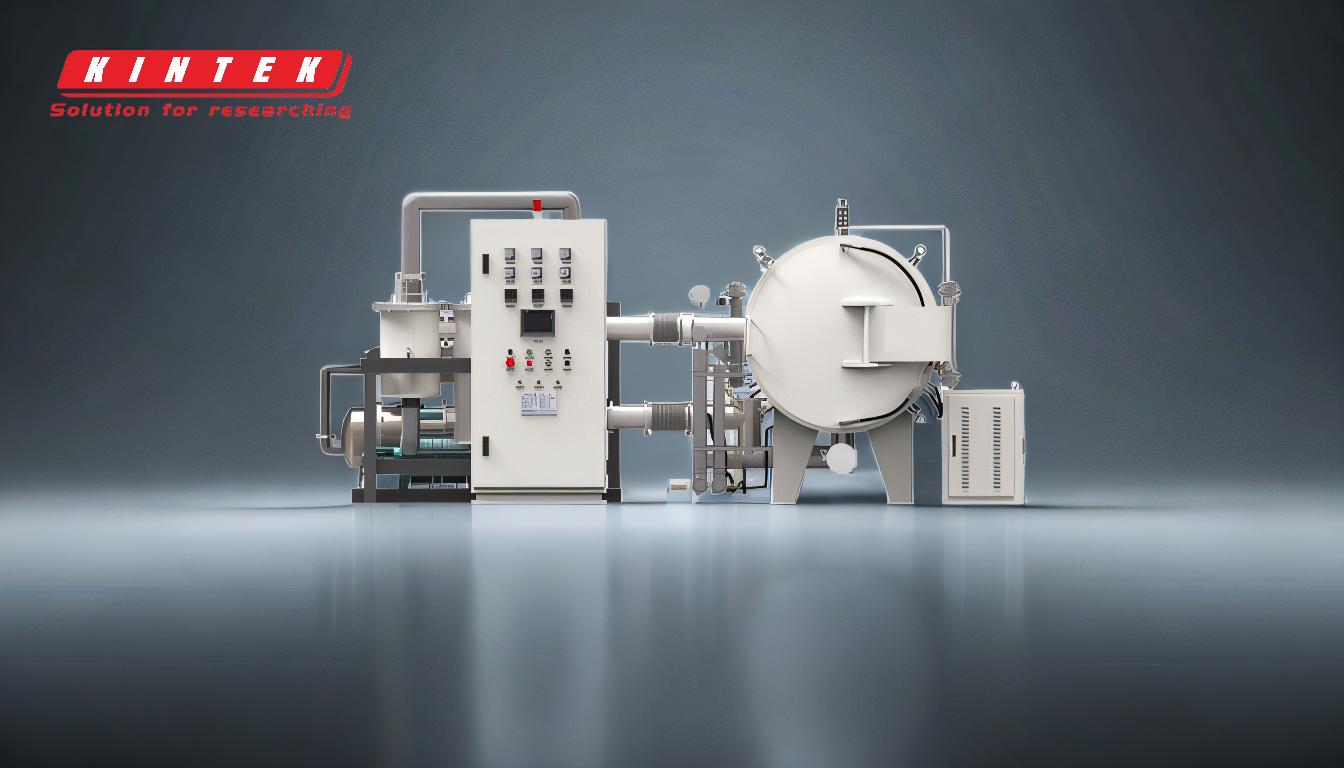
-
Primary Industries Using Horizontal Furnaces:
- Aerospace: Horizontal furnaces are used for heat treatment processes like annealing, hardening, and tempering of aerospace components. These processes ensure the materials meet stringent performance and safety standards.
- Automotive: In the automotive industry, horizontal furnaces are employed for processes such as carburizing and carbonitriding, which enhance the durability and strength of metal parts.
- Electronics Manufacturing: These furnaces are used for processes like sintering and thermal analysis, which are critical for producing high-quality electronic components.
-
Key Applications of Horizontal Furnaces:
- Heat Treatment: Processes such as annealing, hardening, and tempering are commonly performed in horizontal furnaces. These processes are essential for improving the mechanical properties of metals.
- Sintering: Used in powder metallurgy and ceramics, sintering involves heating materials to just below their melting point to form a solid mass without liquefaction.
- Thermal Analysis: Horizontal furnaces are used to study the thermal properties of materials, which is crucial for research and development in materials science.
- Chemical Vapor Deposition (CVD): This process is used to produce high-purity, high-performance solid materials, often in the electronics and nanotechnology sectors.
-
Advantages of Horizontal Furnaces:
- Uniform Heating: Horizontal furnaces provide consistent and uniform heating, which is essential for processes that require precise temperature control.
- High Performance: Designed for high-performance production environments, these furnaces can handle large volumes of material efficiently.
- Cost Savings: The ability to process large volumes of material per hour results in significant cost savings, making horizontal furnaces a cost-effective solution for many industries.
- Low Maintenance: Horizontal furnaces are designed to be low maintenance, reducing downtime and operational costs.
-
Specific Processes in Various Industries:
- Materials Science: Horizontal furnaces are used for thermal decomposition, pyrolysis, and annealing of materials, which are critical for developing new materials with specific properties.
- Metallurgy: Processes like forging and heat treatment are commonly performed in horizontal furnaces to enhance the mechanical properties of metals.
- Ceramics: Sintering and annealing processes in the ceramics industry are often carried out in horizontal furnaces to achieve the desired material properties.
- Battery Manufacturing: Horizontal furnaces are used in the production of batteries, particularly for processes that require precise thermal control, such as the sintering of battery components.
-
Design and Operational Features:
- Precise Temperature Control: Horizontal furnaces are equipped with advanced temperature control systems to ensure precise and consistent heating, which is crucial for many industrial processes.
- Large Volume Processing: The horizontal design allows for the efficient processing of large volumes of material, making these furnaces ideal for high-throughput production environments.
- Versatility: Horizontal furnaces can be used for a wide range of processes, from simple heat treatment to complex chemical vapor deposition, making them a versatile tool in many industries.
In summary, horizontal furnaces are essential equipment in various industries due to their ability to provide precise temperature control, uniform heating, and efficient processing of large volumes of material. Their applications range from heat treatment and sintering to chemical vapor deposition, making them a versatile and cost-effective solution for many industrial processes.
Summary Table:
Aspect | Details |
---|---|
Primary Industries | Aerospace, Automotive, Electronics, Materials Science, Metallurgy, Ceramics, Battery Manufacturing |
Key Applications | Heat Treatment, Sintering, Thermal Analysis, Chemical Vapor Deposition (CVD) |
Advantages | Uniform Heating, High Performance, Cost Savings, Low Maintenance |
Design Features | Precise Temperature Control, Large Volume Processing, Versatility |
Ready to optimize your thermal processing? Contact our experts today to find the perfect horizontal furnace for your needs!