High-frequency furnaces are essential in various industrial and metallurgical processes due to their ability to provide precise and efficient heating. High-frequency induction heating is particularly useful when rapid heating, localized heating, or precise temperature control is required. This method is commonly used in applications such as metal melting, forging, brazing, and heat treatment. The need for high frequency arises from its ability to generate eddy currents directly within the material, leading to uniform and controlled heating. Below, we explore the reasons and scenarios where high-frequency furnaces are indispensable.
Key Points Explained:
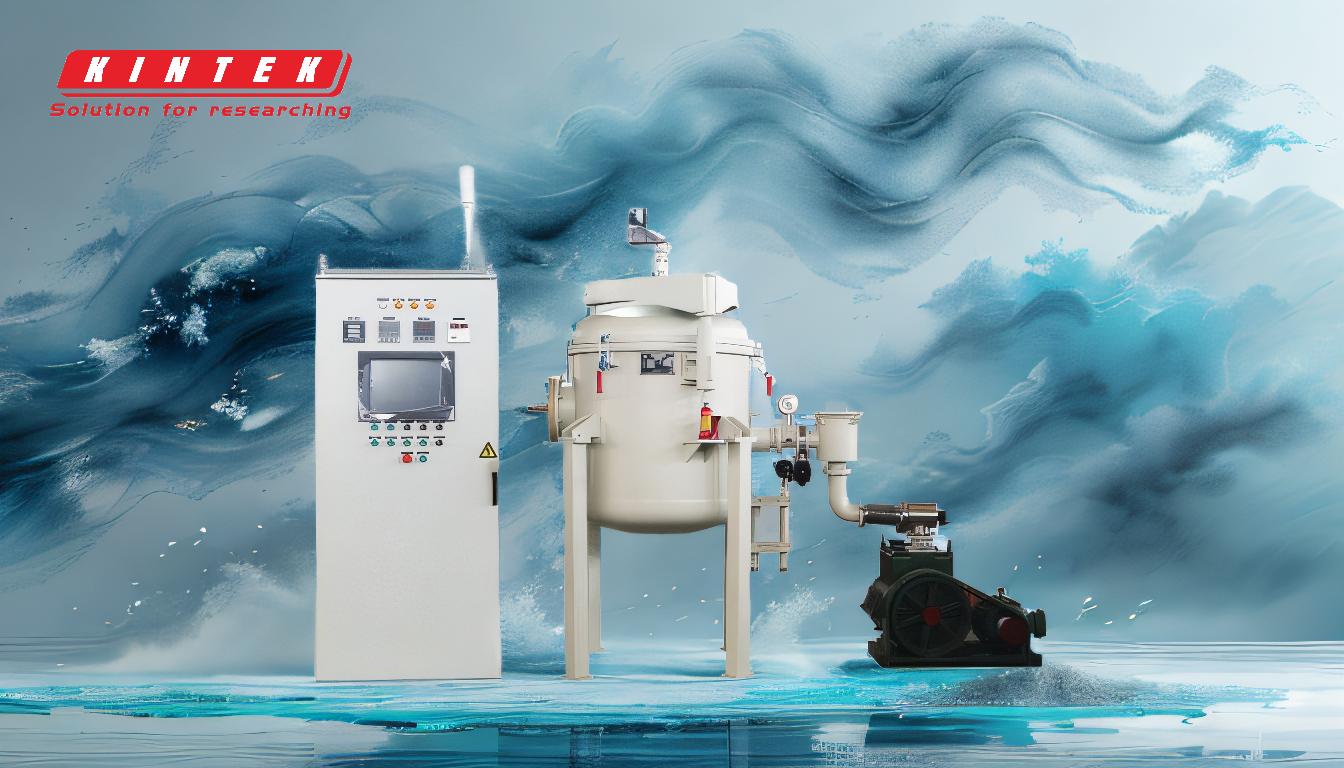
-
Understanding High-Frequency Induction Heating:
- High-frequency induction heating operates on the principle of electromagnetic induction. When a high-frequency alternating current passes through a coil, it generates a rapidly alternating magnetic field. This field induces eddy currents within the conductive material placed inside the coil, causing it to heat up due to electrical resistance.
- The frequency of the alternating current determines the depth of penetration of the eddy currents (skin effect). Higher frequencies result in shallower penetration, making them ideal for heating smaller or thinner materials.
-
When High Frequency is Needed:
- Rapid Heating: High-frequency furnaces are ideal for applications requiring quick heating, such as in metalworking or manufacturing processes where time efficiency is critical.
- Localized Heating: In processes like brazing or welding, only specific areas of a component need to be heated. High-frequency induction allows for precise targeting of heat without affecting the surrounding material.
- Surface Hardening: High-frequency heating is used in surface hardening processes (e.g., induction hardening) where only the outer layer of a metal part needs to be hardened while maintaining the core's toughness.
- Melting of Precious Metals: High-frequency furnaces are often used for melting precious metals like gold, silver, and platinum due to their ability to provide clean and controlled heating.
- Thin Materials: High frequencies are suitable for heating thin materials or small components because the shallow penetration ensures uniform heating without overheating.
-
Advantages of High-Frequency Furnaces:
- Energy Efficiency: High-frequency induction heating is highly efficient as it directly heats the material, minimizing energy loss.
- Precision and Control: The ability to control the frequency and power allows for precise temperature regulation, which is crucial in processes like annealing or tempering.
- Clean and Contaminant-Free Heating: Since the heat is generated within the material itself, there is no risk of contamination from external sources, making it ideal for applications in the jewelry and electronics industries.
- Compact and Portable: High-frequency furnaces are often smaller and more portable compared to traditional furnaces, making them suitable for workshops and small-scale operations.
-
Applications Requiring High Frequency:
- Metal Melting: High-frequency induction furnaces are widely used for melting metals, especially in foundries and jewelry manufacturing.
- Heat Treatment: Processes like annealing, tempering, and hardening often require high-frequency heating to achieve the desired material properties.
- Brazing and Soldering: High-frequency induction is used to join metals by melting a filler material without melting the base metals.
- Forging and Forming: High-frequency heating is used to soften metals before shaping them into desired forms.
- Electronics Manufacturing: High-frequency induction is used in the production of semiconductors and other electronic components where precise heating is critical.
-
Factors Influencing Frequency Selection:
- Material Type: The electrical conductivity and magnetic permeability of the material influence the choice of frequency.
- Heating Depth: Higher frequencies are chosen for shallow heating, while lower frequencies are used for deeper penetration.
- Component Size: Smaller components or thin materials require higher frequencies to ensure uniform heating.
- Process Requirements: The specific requirements of the process, such as heating speed and temperature control, determine the optimal frequency.
-
Challenges and Considerations:
- Equipment Cost: High-frequency furnaces can be more expensive than traditional heating methods due to their advanced technology.
- Power Supply Requirements: High-frequency induction requires a stable and powerful electrical supply, which may not be available in all locations.
- Material Limitations: Not all materials are suitable for high-frequency induction heating. Non-conductive materials, for example, cannot be heated using this method.
In summary, high-frequency furnaces are indispensable in scenarios where rapid, precise, and localized heating is required. Their ability to provide energy-efficient and contamination-free heating makes them a preferred choice in industries ranging from metallurgy to electronics. However, the selection of frequency and equipment must be carefully considered based on the material, process requirements, and operational constraints.
Summary Table:
Key Aspect | Details |
---|---|
Rapid Heating | Ideal for time-critical processes like metalworking and manufacturing. |
Localized Heating | Targets specific areas for brazing, welding, or surface hardening. |
Surface Hardening | Hardens outer layers while maintaining core toughness. |
Melting Precious Metals | Provides clean, controlled heating for gold, silver, and platinum. |
Thin Material Heating | Ensures uniform heating without overheating small or thin components. |
Energy Efficiency | Directly heats materials, minimizing energy loss. |
Applications | Metal melting, heat treatment, brazing, forging, and electronics manufacturing. |
Challenges | High equipment costs, power supply requirements, and material limitations. |
Ready to enhance your heating processes with high-frequency furnaces? Contact us today to find the perfect solution for your needs!