Heat treatment is a critical process in materials science and manufacturing that involves controlled heating and cooling of metals and alloys to alter their physical and mechanical properties. This process is used to achieve desired characteristics such as increased hardness, improved ductility, enhanced strength, and better wear resistance. Heat treatment techniques, including annealing, quenching, tempering, and case hardening, are applied to both ferrous and non-ferrous metals to make them suitable for specific industrial applications. By manipulating the microstructure of the material through precise temperature control and cooling rates, heat treatment ensures a balance between cost and quality, making it indispensable in industries like aerospace, automotive, and batch metal production.
Key Points Explained:
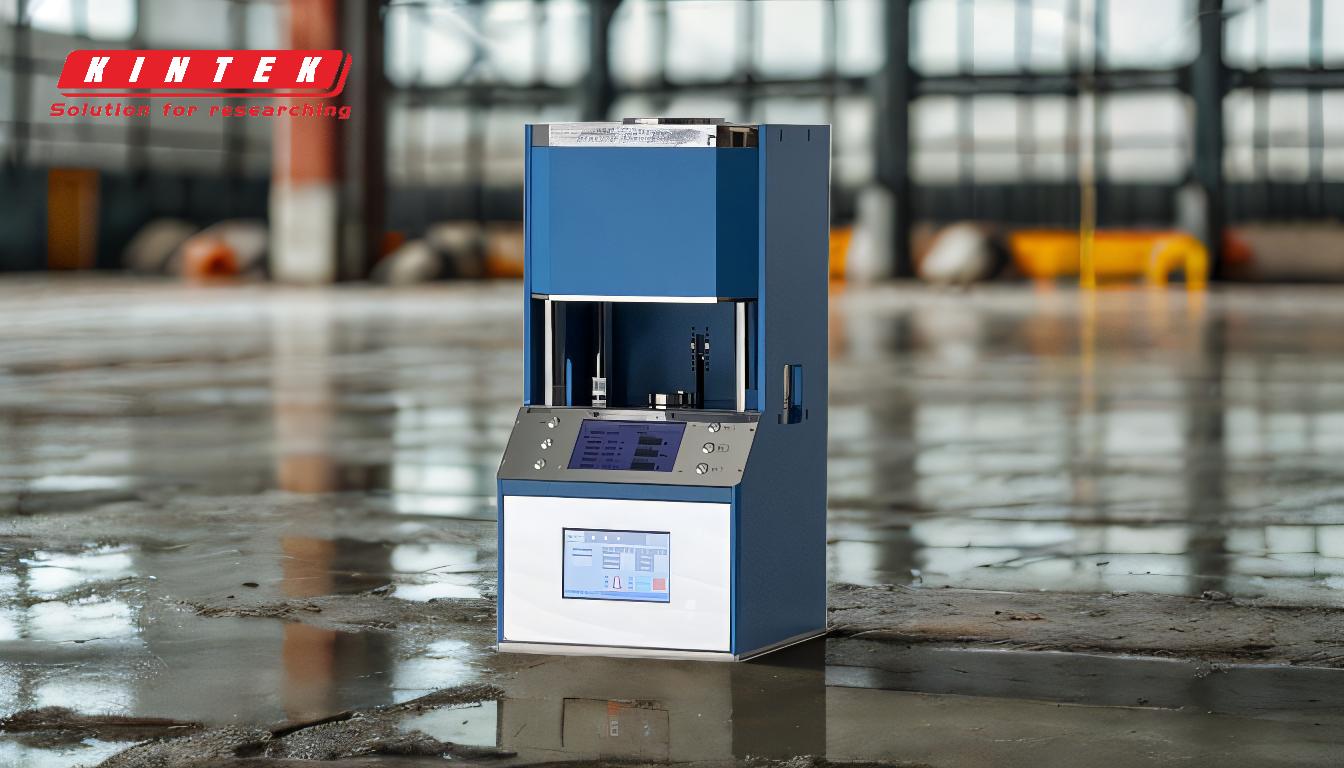
-
Definition and Purpose of Heat Treatment
- Heat treatment is a process that involves heating and cooling metals or alloys in a controlled manner to modify their physical and mechanical properties.
- The primary purpose is to achieve desired characteristics such as increased hardness, improved ductility, enhanced strength, and better wear resistance.
- It is applicable to both ferrous (iron-based) and non-ferrous metals (e.g., aluminum, copper).
-
Common Heat Treatment Techniques
- Annealing: Heating the material to a specific temperature and then slowly cooling it to soften the metal, improve ductility, and reduce internal stresses.
- Quenching: Rapidly cooling the material after heating to increase hardness and strength, often by immersing it in water, oil, or air.
- Tempering: Reheating a quenched material to a lower temperature to reduce brittleness while maintaining hardness.
- Case Hardening: Adding a hard surface layer to a softer metal core, often through processes like carburizing or nitriding.
- Normalizing: Heating the material to a high temperature and then air-cooling it to refine the grain structure and improve mechanical properties.
- Precipitation Strengthening: Heating an alloy to dissolve a constituent, followed by rapid cooling to create a supersaturated solution, which then hardens over time.
-
How Heat Treatment Alters Material Properties
- Heat treatment works by manipulating the microstructure of the metal, which directly influences its mechanical properties.
- Controlled heating allows atoms to diffuse and rearrange, while controlled cooling locks these changes into place.
- For example, quenching creates a hard but brittle structure, while tempering reduces brittleness by allowing some of the internal stresses to relax.
-
Applications of Heat Treatment
- Heat treatment is widely used in industries such as aerospace, automotive, and manufacturing to enhance the performance and durability of components.
- It is essential for producing parts that require a balance of strength, toughness, and wear resistance, such as gears, shafts, and engine components.
- Batch metal production also relies on heat treatment to ensure consistent quality across large quantities of parts.
-
Importance of Temperature and Cooling Rates
- The success of heat treatment depends on precise control of heating temperatures and cooling rates.
- Heating to the correct temperature ensures that the desired phase transformations occur in the metal's microstructure.
- Cooling rates determine whether the material becomes harder (fast cooling) or softer (slow cooling).
-
Benefits of Heat Treatment
- Improves mechanical properties such as hardness, strength, toughness, and ductility.
- Enhances wear resistance and durability, extending the lifespan of components.
- Allows for customization of material properties to meet specific application requirements.
-
Challenges and Considerations
- Heat treatment requires specialized equipment and expertise to ensure consistent results.
- Overheating or improper cooling can lead to defects such as warping, cracking, or uneven hardness.
- The process must be tailored to the specific material and desired outcome, making it essential to follow precise guidelines.
In conclusion, heat treatment is a versatile and essential process in materials engineering that enables the customization of metal properties to meet the demands of various industrial applications. By understanding the principles and techniques involved, manufacturers can optimize the performance and longevity of their products.
Summary Table:
Aspect | Details |
---|---|
Purpose | Modify physical and mechanical properties of metals and alloys. |
Common Techniques | Annealing, quenching, tempering, case hardening, normalizing, precipitation strengthening. |
Key Benefits | Increased hardness, improved ductility, enhanced strength, better wear resistance. |
Applications | Aerospace, automotive, manufacturing, batch metal production. |
Critical Factors | Precise temperature control and cooling rates. |
Challenges | Requires specialized equipment; risk of warping, cracking, or uneven hardness. |
Optimize your materials with expert heat treatment solutions—contact us today!