Debinding is a critical step in the manufacturing of technical ceramics and 3D-printed parts, involving the removal of organic binders or carrier materials from the green body. This process ensures the structural integrity of the final product by eliminating impurities that could lead to defects during sintering. Debinding can be achieved through thermal or chemical methods, with thermal debinding being the most common. It involves carefully controlled heating in a nitrogen-purged furnace to avoid oxidation and defects. The process typically starts at room temperature and progresses to around 600°C, with precise control over temperature, pressure, gas atmosphere, and time to prevent warping or cracking. The duration of debinding varies based on the part's geometry, often taking 24-36 hours, and may require multiple furnace passes to ensure complete binder removal.
Key Points Explained:
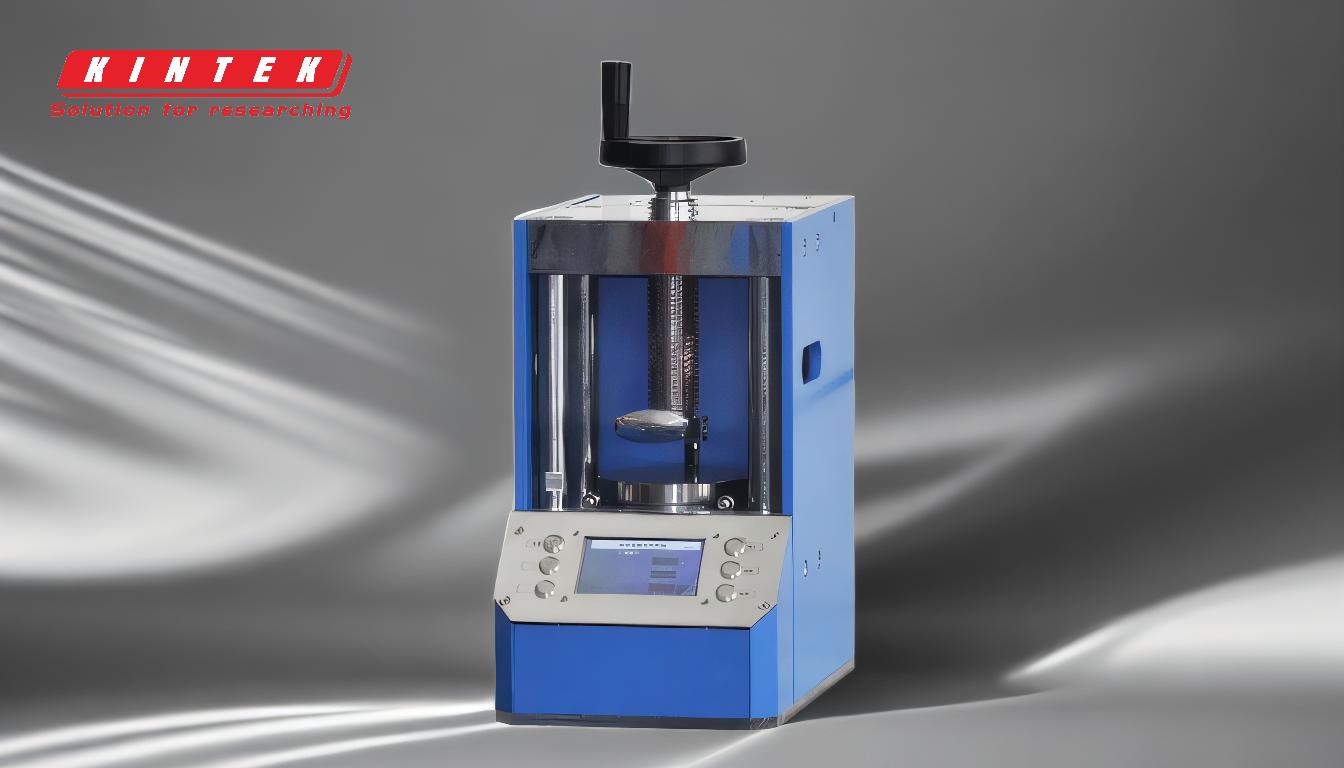
-
Purpose of Debinding:
- Debinding removes organic binders or carrier materials from the green body (uncured ceramic or 3D-printed parts).
- This step is essential to prevent contamination during sintering, which could lead to defects like cracks or warps in the final product.
-
Methods of Debinding:
- Thermal Debinding: The most common method, involving controlled heating in a furnace. The process starts at room temperature and gradually increases to 600°C, ensuring the decomposition of binders without damaging the part.
- Chemical Debinding: Involves immersing the part in a chemical bath to dissolve the binder. This method is less common but can be effective for specific materials.
-
Process Parameters:
- Temperature Profile: The temperature is carefully controlled, often starting at 2°C/min to 225°C, then increasing to 550°C at 1°C/min, and finally reaching up to 600°C or higher. Multiple heating cycles may be required.
- Gas Atmosphere: A nitrogen purge is used to reduce oxygen levels in the furnace, preventing oxidation and ensuring a controlled environment.
- Time: Debinding can take 24-36 hours, depending on the part's geometry and binder content. Thicker or more complex parts require longer debinding times.
-
Importance of Controlled Conditions:
- Precise control of temperature, pressure, and gas atmosphere is crucial to avoid defects such as warping, cracking, or incomplete binder removal.
- Even trace amounts of residual binder can contaminate the sintering phase, leading to poor-quality final products.
-
Post-Debinding Steps:
- After debinding, parts often undergo sintering, where they are heated to even higher temperatures (e.g., 1,300°C) to achieve final density and strength.
- The cooling process is also controlled, typically cooling to 600°C at 6°C/min before allowing parts to cool naturally in the furnace.
-
Applications:
- Debinding is widely used in the production of technical ceramics and metal injection molding (MIM) parts.
- It is also critical in additive manufacturing (3D printing) for removing support materials or binders from printed parts.
By understanding these key points, equipment and consumable purchasers can better evaluate the debinding process requirements for their specific applications, ensuring high-quality outcomes and efficient production workflows.
Summary Table:
Aspect | Details |
---|---|
Purpose | Removes organic binders to prevent defects during sintering. |
Methods | Thermal (most common) or chemical debinding. |
Temperature Profile | Controlled heating from room temperature to 600°C, with precise ramping. |
Gas Atmosphere | Nitrogen purge to prevent oxidation. |
Time | 24-36 hours, depending on part geometry and binder content. |
Applications | Technical ceramics, metal injection molding, and 3D printing. |
Optimize your debinding process for high-quality results—contact our experts today!