Temperature significantly affects the mechanical properties of materials, influencing their strength, ductility, hardness, and toughness. As temperature increases, most materials experience a reduction in strength and hardness, while their ductility and toughness generally increase. This is due to the increased atomic vibrations and mobility at higher temperatures, which facilitate dislocation movement and reduce resistance to deformation. Conversely, at lower temperatures, materials tend to become more brittle and less ductile, as atomic motion is restricted, and dislocations are less mobile. Understanding these temperature-dependent changes is crucial for material selection in applications exposed to varying thermal conditions.
Key Points Explained:
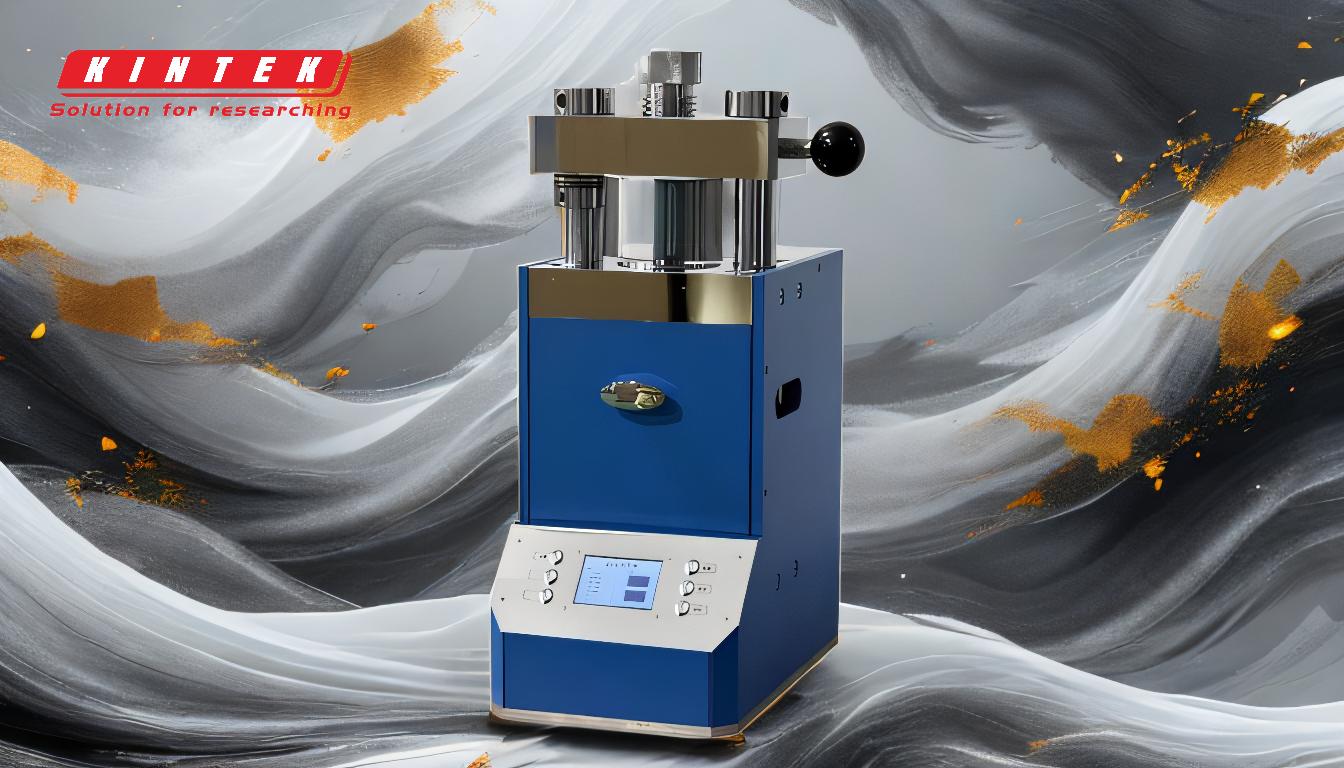
-
Effect of Temperature on Material Strength:
- High Temperatures: At elevated temperatures, materials typically exhibit a decrease in yield strength and tensile strength. This is because higher thermal energy increases atomic vibrations, making it easier for dislocations to move through the material. As a result, the material becomes softer and more prone to deformation.
- Low Temperatures: At lower temperatures, materials generally become stronger but more brittle. Reduced thermal energy restricts dislocation movement, increasing the material's resistance to deformation. However, this increased strength comes at the cost of reduced ductility, making the material more susceptible to fracture under stress.
-
Effect of Temperature on Ductility and Toughness:
- High Temperatures: Ductility and toughness usually increase with temperature. The enhanced atomic mobility allows the material to undergo more plastic deformation before fracturing, making it more ductile. This increased ability to absorb energy before failure also enhances toughness.
- Low Temperatures: Ductility and toughness decrease as temperatures drop. The restricted atomic motion limits the material's ability to deform plastically, leading to a more brittle behavior. This makes the material less capable of absorbing energy, reducing its toughness and increasing the likelihood of brittle fracture.
-
Effect of Temperature on Hardness:
- High Temperatures: Hardness generally decreases with increasing temperature. The increased atomic vibrations and dislocation mobility reduce the material's resistance to indentation and scratching.
- Low Temperatures: Hardness tends to increase at lower temperatures due to the reduced atomic mobility and increased resistance to dislocation movement. This makes the material harder but also more brittle.
-
Thermal Expansion and Contraction:
- High Temperatures: Materials expand when heated due to increased atomic vibrations. This thermal expansion can lead to dimensional changes and stress within the material, potentially affecting its mechanical properties and performance.
- Low Temperatures: Materials contract when cooled, which can also induce stress and affect mechanical properties. The contraction can lead to increased internal stresses, particularly in constrained components, potentially causing cracking or failure.
-
Phase Changes and Microstructural Effects:
- High Temperatures: Some materials undergo phase changes at elevated temperatures, such as melting or recrystallization. These changes can significantly alter the material's microstructure, leading to changes in mechanical properties. For example, annealing at high temperatures can reduce internal stresses and increase ductility.
- Low Temperatures: At low temperatures, certain materials may undergo phase transformations, such as the formation of martensite in steel, which can increase hardness but reduce ductility. These microstructural changes can have a profound impact on the material's mechanical behavior.
-
Creep and Stress Relaxation:
- High Temperatures: Creep, the slow, time-dependent deformation under constant stress, becomes more significant at high temperatures. The increased atomic mobility allows dislocations to move more easily, leading to gradual deformation over time. Stress relaxation, the reduction in stress over time under constant strain, is also more pronounced at elevated temperatures.
- Low Temperatures: Creep and stress relaxation are less significant at low temperatures due to the reduced atomic mobility. However, the material may still experience time-dependent deformation under certain conditions, albeit at a much slower rate.
-
Impact of Temperature on Fatigue Life:
- High Temperatures: Fatigue life, the number of cycles a material can endure before failure, is generally reduced at high temperatures. The increased dislocation mobility and potential for creep deformation accelerate the initiation and propagation of fatigue cracks.
- Low Temperatures: Fatigue life can be either increased or decreased at low temperatures, depending on the material. Some materials may exhibit improved fatigue resistance due to increased strength, while others may become more prone to fatigue failure due to reduced ductility and increased brittleness.
-
Material-Specific Behavior:
- Metals: Metals generally follow the trends described above, with reduced strength and increased ductility at high temperatures, and increased strength and reduced ductility at low temperatures. However, specific metals may exhibit unique behaviors due to their crystal structure and alloying elements.
- Polymers: Polymers are particularly sensitive to temperature changes. At high temperatures, they may soften or melt, significantly reducing their mechanical properties. At low temperatures, they can become brittle and lose their flexibility.
- Ceramics: Ceramics are generally more resistant to high temperatures but can become brittle at low temperatures. Their mechanical properties are less affected by temperature compared to metals and polymers, but they can still experience significant changes under extreme conditions.
Understanding these temperature-dependent changes in mechanical properties is essential for selecting the right material for specific applications, especially those exposed to varying thermal environments. Engineers must consider these effects to ensure the reliability and longevity of materials in real-world applications.
Summary Table:
Property | High Temperature Effects | Low Temperature Effects |
---|---|---|
Strength | Decreases due to increased atomic vibrations and dislocation mobility. | Increases due to reduced atomic mobility, but material becomes more brittle. |
Ductility | Increases as atomic mobility allows more plastic deformation before fracture. | Decreases as restricted atomic motion limits plastic deformation. |
Hardness | Decreases due to reduced resistance to indentation and scratching. | Increases due to restricted dislocation movement. |
Toughness | Increases as the material can absorb more energy before failure. | Decreases as the material becomes more brittle and less capable of absorbing energy. |
Thermal Expansion | Materials expand, leading to dimensional changes and potential stress. | Materials contract, inducing stress and potential cracking. |
Phase Changes | Phase transformations (e.g., melting, recrystallization) alter microstructure and properties. | Phase changes (e.g., martensite formation) increase hardness but reduce ductility. |
Creep | More significant due to increased atomic mobility and dislocation movement. | Less significant due to reduced atomic mobility. |
Fatigue Life | Generally reduced due to accelerated crack initiation and propagation. | Varies by material; some show improved resistance, others become more prone to failure. |
Need help selecting the right material for your application? Contact our experts today for tailored solutions!