Induction heaters can achieve a wide range of temperatures, from as low as 100°C (212°F) to as high as 3000°C (5432°F), depending on the application and design. Specific systems, such as induction melting furnaces, typically operate between 1600°C (2900°F) and 2000°C (3632°F), with some reaching up to 1800°C (3272°F) or more. The temperature achieved depends on factors like inductive coupling, the material being heated, and the design of the inductor. While induction heating is versatile, it often requires custom inductors and careful engineering to manage high-current densities in small copper coils.
Key Points Explained:
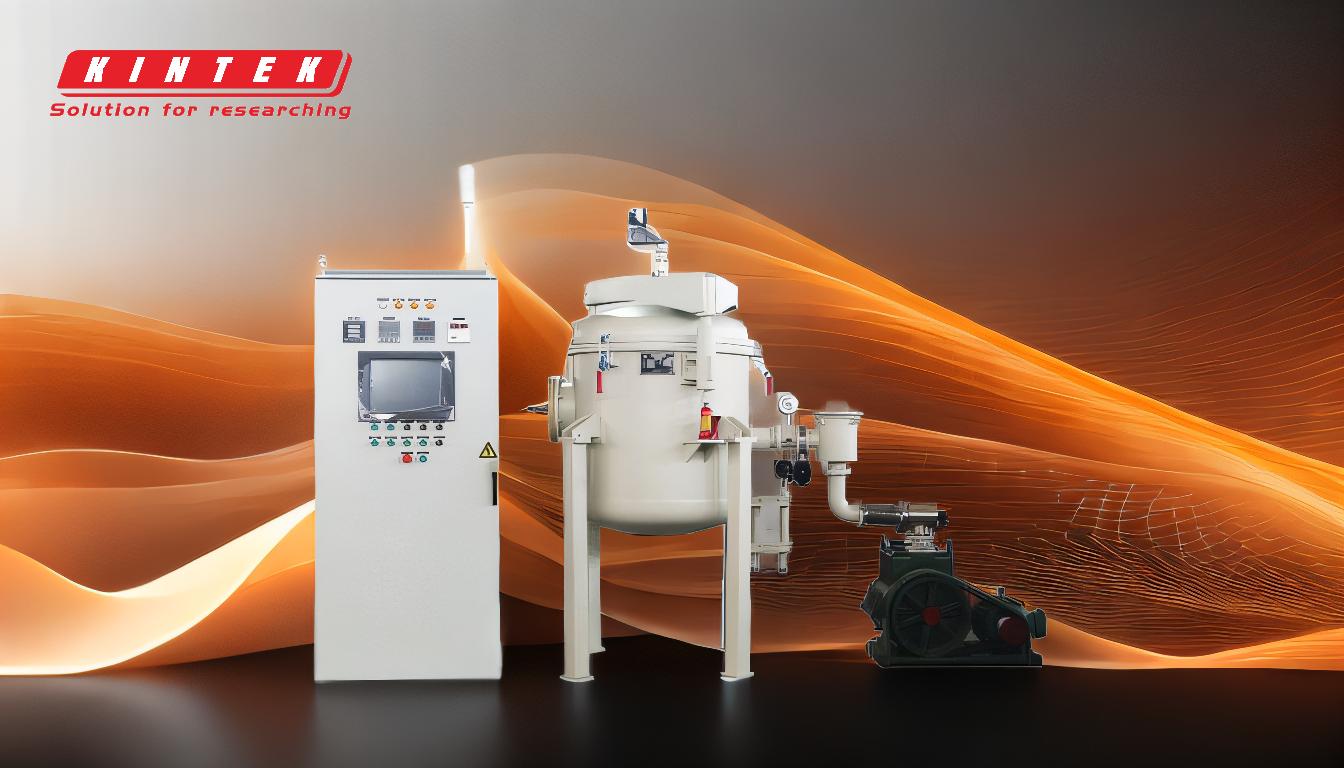
-
Temperature Range of Induction Heating:
- Induction heaters can operate across a broad temperature spectrum, from 100°C (212°F) to 3000°C (5432°F).
- This range makes induction heating suitable for a wide variety of applications, from low-temperature processes like cooking or medical treatments to high-temperature industrial processes like metal melting.
-
Induction Melting Furnaces:
- Induction melting furnaces are a common application of induction heating, capable of reaching temperatures between 1600°C (2900°F) and 2000°C (3632°F).
- Some systems can achieve even higher temperatures, up to 1800°C (3272°F) or more, depending on the inductive coupling between the coil and the material being heated.
-
Factors Influencing Temperature:
- Inductive Coupling: The efficiency of heat transfer between the induction coil and the material being heated plays a critical role in determining the maximum achievable temperature.
- Material Properties: The type of material being heated (e.g., metals with different melting points) affects the temperature range.
- Inductor Design: Custom inductors are often required to optimize heating for specific applications, which can influence the maximum temperature.
-
Engineering Challenges:
- High-Current Densities: Induction heaters require managing high-current densities in small copper inductors, which can generate significant heat and necessitate specialized cooling systems.
- Custom Inductors: Many applications require tailored inductor designs, which can be expensive and time-consuming to produce.
-
Applications of Induction Heating:
- Industrial Processes: Induction heating is widely used in metalworking, including forging, brazing, and melting.
- Domestic Uses: Induction cooktops are a common household application, operating at lower temperatures (typically up to 300°C or 570°F).
- Medical Treatments: Induction heating is used in medical devices for processes like sterilization or tissue treatment.
-
Limitations of Induction Heating:
- Cost and Complexity: The need for custom inductors and specialized engineering can make induction heating systems expensive and complex to design and maintain.
- Energy Efficiency: While induction heating is generally efficient, achieving very high temperatures (e.g., above 2000°C) may require significant energy input.
In summary, induction heaters are highly versatile and capable of reaching extreme temperatures, but their performance depends on factors like inductive coupling, material properties, and inductor design. While they offer significant advantages in efficiency and precision, the need for custom engineering and high-current management can pose challenges.
Summary Table:
Aspect | Details |
---|---|
Temperature Range | 100°C (212°F) to 3000°C (5432°F) |
Induction Melting | 1600°C (2900°F) to 2000°C (3632°F), with some reaching 1800°C (3272°F) or more |
Key Factors | Inductive coupling, material properties, inductor design |
Applications | Industrial (melting, forging), domestic (cooktops), medical (sterilization) |
Challenges | High-current densities, custom inductor design, cost, and complexity |
Ready to explore induction heating solutions for your needs? Contact us today to get started!