Calculating the power consumption of an induction furnace involves understanding the relationship between production capacity, energy efficiency, and operational parameters. The process typically starts with determining the desired production output, such as yearly or daily tonnage, and then using standard power consumption metrics to estimate the required power supply capacity. For instance, if the standard power consumption for a steel induction furnace is 625 kWh/ton, the required power can be calculated by multiplying the hourly production rate by this value. Additionally, factors such as the type of material being melted, furnace efficiency, and operational conditions (e.g., cleanliness of the charge, refractory materials used) play a significant role in determining the overall power consumption. Advanced calculations may also involve specific heat capacity, heating temperature, and time, using formulas that account for these variables.
Key Points Explained:
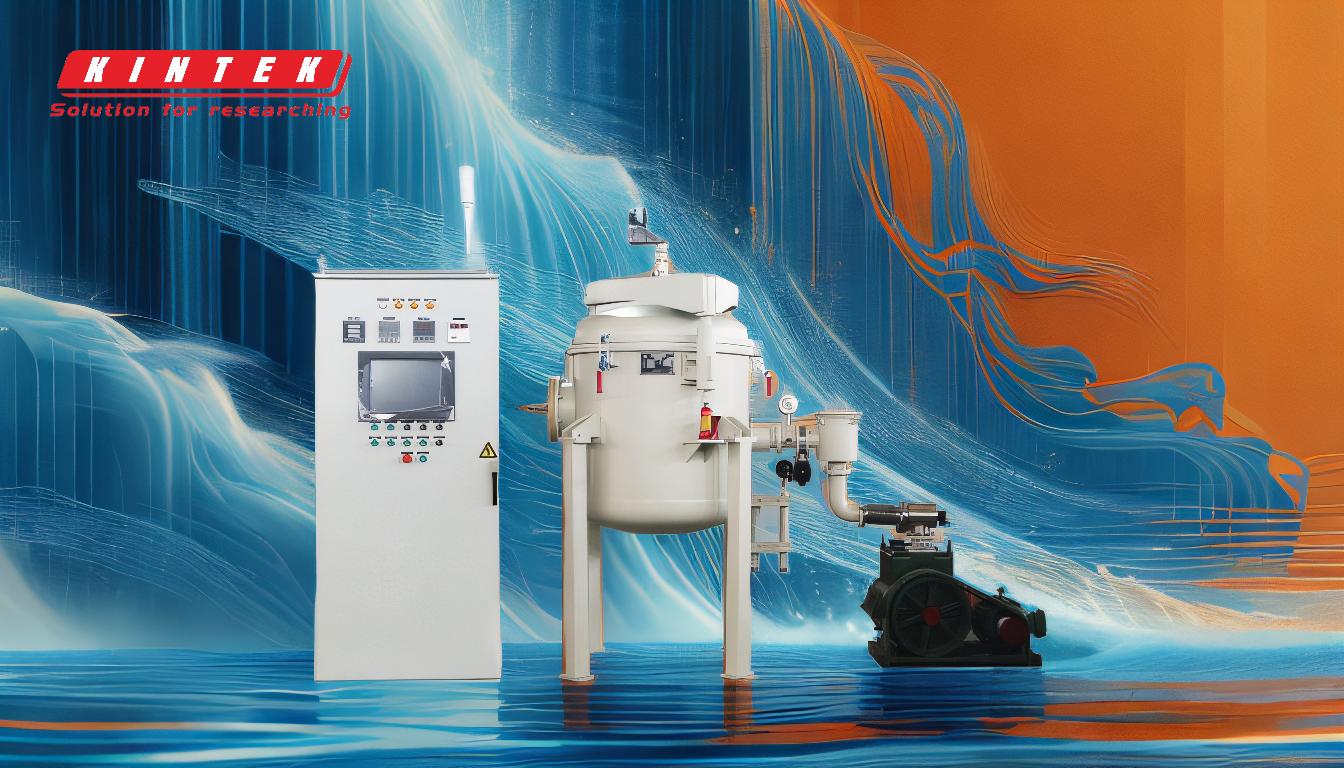
-
Understanding Production Capacity and Power Requirements:
- The first step in calculating power consumption is to determine the desired production capacity, typically measured in tons per year or per day.
- For example, if the desired yearly production is 2000 tons, and the furnace operates 240 days a year, the daily production is 8.33 tons/day.
- To find the hourly production, divide the daily production by the number of operating hours per day. For a two-shift operation of 16 hours, the hourly production is 0.520 tons/hour (520 kg/hour).
-
Using Standard Power Consumption Metrics:
- The standard power consumption for a steel induction furnace is 625 kWh/ton.
- Multiply the hourly production rate by the standard power consumption to calculate the required power supply capacity.
- For example, (520 kg/hour) * (625 kWh/1000 kg) = 325 kW.
-
Factors Affecting Power Consumption:
- Melting Rate and Power Configuration: The efficiency of the medium frequency power supply and the melting rate directly impact power consumption.
- Charge Cleanliness and Size: A clean charge and appropriate furnace block length improve efficiency, reducing power consumption.
- Refractory Materials: The type of refractory materials used, such as quartz crucibles, can influence heat transfer and overall energy efficiency.
-
Advanced Power Calculation Formula:
- For more precise calculations, use the formula:
[
P = \frac{C \times T \times G}{0.24 \times S \times \eta}
]
where:
- ( P ) = Power (kW)
- ( C ) = Specific heat of the material (kcal/kg℃)
- ( T ) = Heating temperature (℃)
- ( G ) = Workpiece weight (kg)
- ( S ) = Time (seconds)
- ( \eta ) = Heating efficiency (typically 0.6)
- This formula accounts for the material's specific heat, the desired temperature, and the time required to achieve it, providing a more detailed power consumption estimate.
- For more precise calculations, use the formula:
[
P = \frac{C \times T \times G}{0.24 \times S \times \eta}
]
where:
-
Operational Considerations:
- Energy Efficiency: Induction furnaces are designed for low energy consumption and high efficiency, but operational practices (e.g., maintaining clean charges, using appropriate refractory materials) are crucial for optimizing power usage.
- Cost Implications: Lower power consumption translates to reduced operational costs, making it essential to accurately calculate and optimize power requirements.
By following these steps and considering the factors mentioned, you can accurately calculate the power consumption of an induction furnace, ensuring efficient and cost-effective operation.
Summary Table:
Key Factor | Details |
---|---|
Production Capacity | Determine desired output (e.g., tons/year or tons/day). |
Standard Power Consumption | 625 kWh/ton for steel induction furnaces. |
Hourly Power Calculation | Multiply hourly production rate by standard power consumption. |
Factors Affecting Consumption | Melting rate, charge cleanliness, refractory materials, and furnace design. |
Advanced Formula | ( P = \frac{C \times T \times G}{0.24 \times S \times \eta} ) |
Operational Considerations | Energy efficiency, cost implications, and optimization practices. |
Need help calculating your induction furnace's power consumption? Contact our experts today for tailored solutions!