Selective Heat Sintering (SHS) is a 3D printing technology that offers numerous advantages, particularly for engineers and designers. It eliminates the need for support structures, enabling the creation of complex geometries and intricate designs with high accuracy and repeatability. SHS improves mechanical properties, reduces porosity, and enhances material strength, electrical conductivity, and thermal conductivity. It is cost-effective, energy-efficient, and versatile in material selection, making it suitable for producing high-performance components. Additionally, SHS is environmentally friendly, producing no harmful emissions, and offers vibration damping properties due to the dense bond between particles.
Key Points Explained:
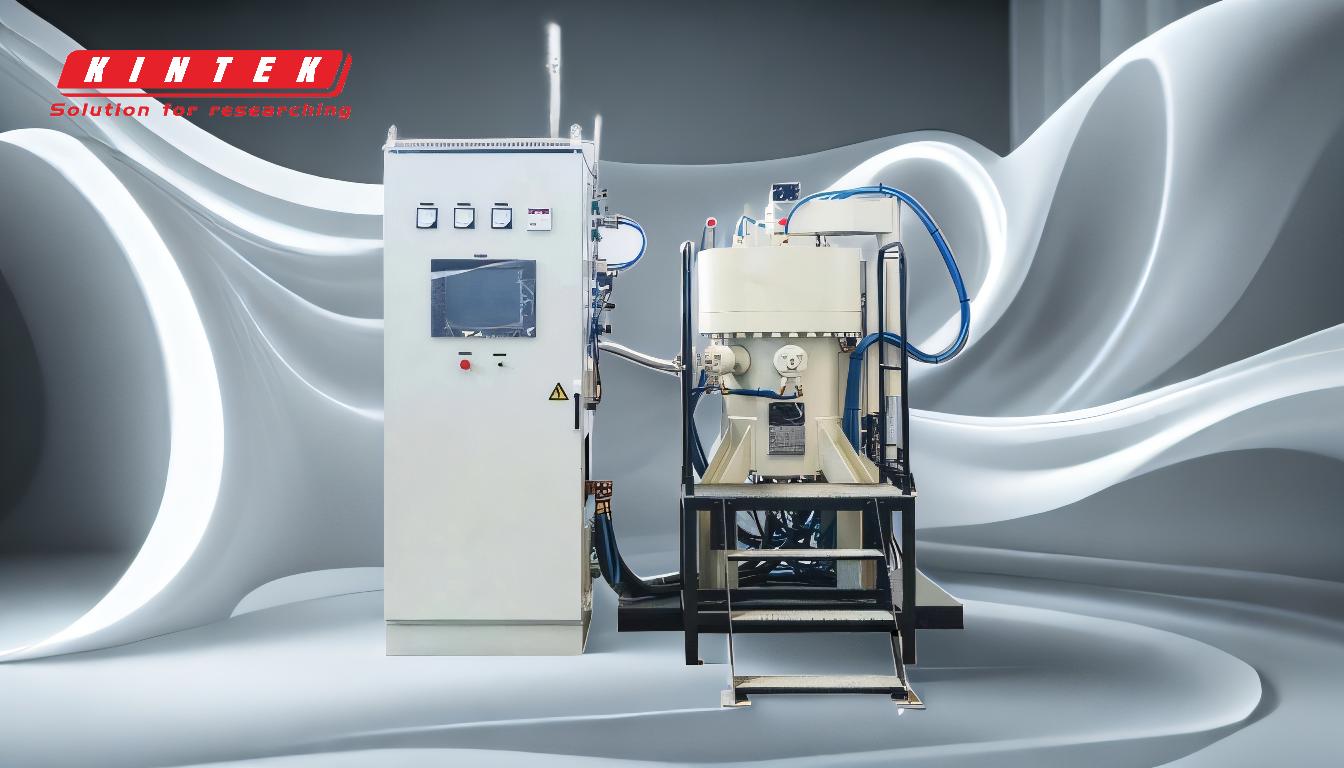
-
No Need for Support Structures:
- Selective Heat Sintering builds 3D objects without requiring support structures, simplifying the design and post-processing stages. This is particularly beneficial for creating complex geometries and internal features that would be challenging to produce using traditional manufacturing methods.
-
Complex Geometries and Intricate Designs:
- SHS allows for the production of parts with complex shapes and intricate designs. The layer-by-layer melting of metal powder ensures high accuracy and repeatability, making it ideal for components that demand precise dimensions and detailed features.
-
Improved Mechanical Properties:
- The sintering process enhances the mechanical properties of the final product. It reduces porosity, increases strength, and improves properties such as electrical conductivity, transparency, and thermal conductivity. This results in components that are stronger and more durable.
-
Cost-Effectiveness and Energy Efficiency:
- SHS is a cost-effective and energy-efficient manufacturing method. It eliminates the need for lubricants in the compacted powder and reduces surface oxygen, leading to better material utilization and lower production costs. Additionally, it works with high-melting-point materials without the need for melting, further saving energy.
-
Versatility in Material Selection:
- SHS offers versatility in material selection, allowing for the use of various metals and ceramics. This flexibility enables the production of components with tailored material compositions to meet specific performance requirements.
-
Environmental Benefits:
- SHS is considered a green technology as it produces no harmful emissions. The process is environmentally friendly, making it a sustainable choice for modern manufacturing.
-
Vibration Damping Properties:
- The dense bond between particles in SHS provides vibration damping properties, which can be beneficial for applications requiring reduced noise and vibration.
-
High Dimensional Precision and Repeatability:
- SHS ensures high dimensional precision, making the finished product very close to the desired shape. This reliability and repeatability are crucial for large-scale production, ensuring consistent quality across multiple units.
-
Enhanced Product Performance:
- The sintering process promotes densification, improves strength, and enhances overall product performance. It also prevents oxidation and pollution, leading to higher-quality products.
-
Creation of Isotropic Materials:
- SHS can create unique isotropic materials with uniform properties in all directions. This uniformity is essential for applications requiring consistent performance regardless of the direction of force or stress.
In summary, Selective Heat Sintering offers a comprehensive set of advantages that make it a highly attractive option for modern manufacturing. Its ability to produce complex, high-performance components with precision and efficiency, coupled with its environmental benefits, positions SHS as a leading technology in the field of additive manufacturing.
Summary Table:
Advantage | Description |
---|---|
No Support Structures | Simplifies design and post-processing, ideal for complex geometries. |
Complex Geometries | Enables intricate designs with high accuracy and repeatability. |
Improved Mechanical Properties | Reduces porosity, enhances strength, conductivity, and durability. |
Cost-Effective & Energy-Efficient | Reduces material waste and energy consumption, lowering production costs. |
Versatile Material Selection | Compatible with various metals and ceramics for tailored performance. |
Environmental Benefits | Produces no harmful emissions, making it a sustainable manufacturing option. |
Vibration Damping | Dense particle bonds reduce noise and vibration in final products. |
High Dimensional Precision | Ensures consistent quality and repeatability for large-scale production. |
Enhanced Product Performance | Improves strength, prevents oxidation, and enhances overall product quality. |
Isotropic Materials | Creates uniform materials with consistent properties in all directions. |
Ready to transform your 3D printing process? Contact us today to learn more about Selective Heat Sintering!