Heat treatment of steel involves a variety of processes designed to alter the material's physical and mechanical properties, such as hardness, strength, ductility, and toughness. These processes are essential in manufacturing to ensure that steel components meet specific performance requirements. The most common methods include annealing, quenching, tempering, normalizing, case hardening, and martensitic transformation. Each method involves heating the steel to a specific temperature, holding it at that temperature for a set duration, and then cooling it in a controlled manner. The choice of method depends on the desired outcome, whether it's increasing hardness, improving ductility, or relieving internal stresses.
Key Points Explained:
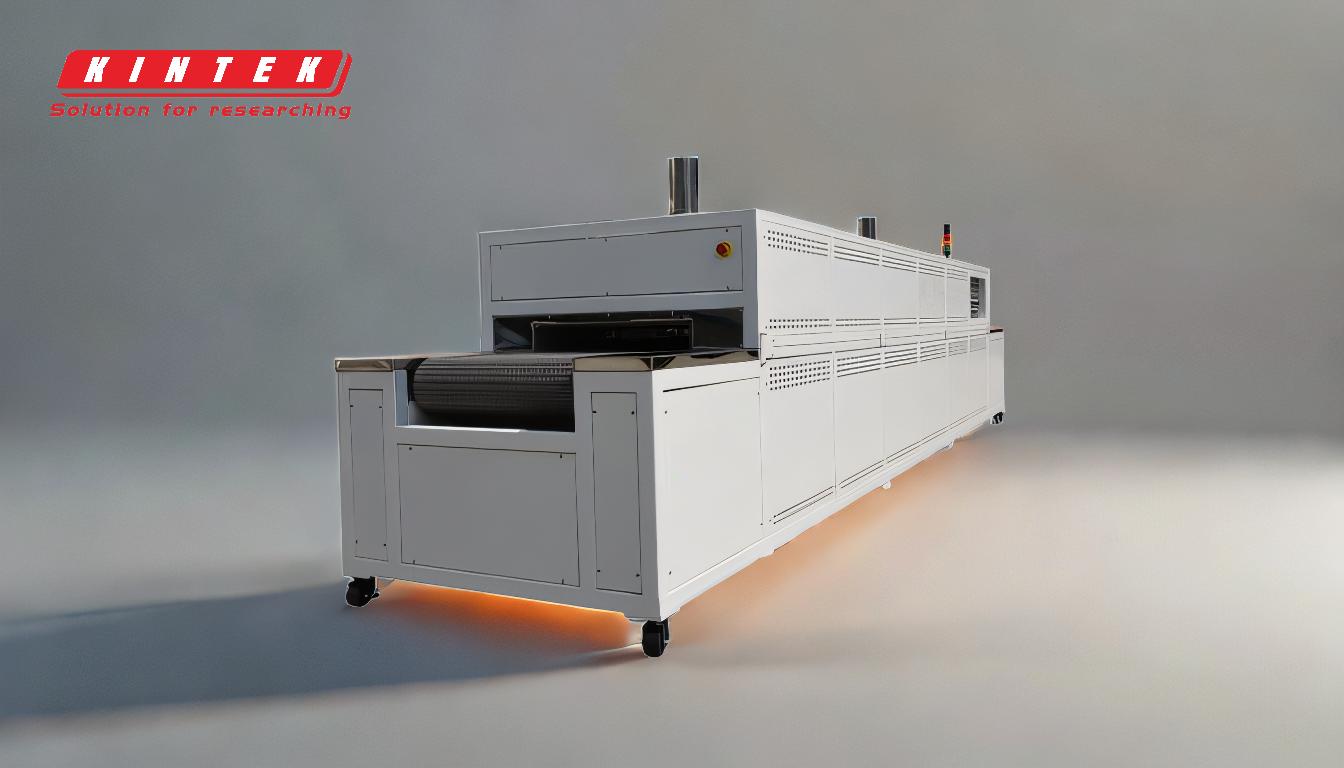
-
Annealing:
- Process: Annealing involves heating the steel to a specific temperature (typically between 1,500°F and 1,600°F) and then allowing it to cool slowly, usually in the furnace.
- Purpose: This process softens the steel, making it more ductile and less brittle. It also relieves internal stresses and refines the grain structure, which improves machinability.
- Applications: Annealing is commonly used in the manufacturing of tools, machinery, and structural components where improved ductility and reduced hardness are required.
-
Quenching:
- Process: Quenching involves heating the steel to a high temperature (often above 1,500°F) and then rapidly cooling it by immersing it in a quenching medium such as water, oil, or polymer solutions.
- Purpose: This process increases the hardness and strength of the steel by transforming the microstructure into martensite, a very hard and brittle form of steel.
- Applications: Quenching is used in the production of tools, gears, and other components that require high surface hardness and wear resistance.
-
Tempering:
- Process: After quenching, the steel is often too brittle for practical use. Tempering involves reheating the quenched steel to a lower temperature (typically between 300°F and 700°F) and then cooling it slowly.
- Purpose: This process reduces the brittleness of the steel while maintaining a significant portion of its hardness. It also improves toughness and ductility.
- Applications: Tempering is essential for components that need a balance of hardness and toughness, such as springs, cutting tools, and structural parts.
-
Normalizing:
- Process: Normalizing involves heating the steel to a temperature above its critical range (typically between 1,600°F and 1,800°F) and then allowing it to cool in air.
- Purpose: This process refines the grain structure, improves mechanical properties, and relieves internal stresses. It results in a more uniform and fine-grained microstructure compared to annealing.
- Applications: Normalizing is used for components that require improved mechanical properties and a more uniform structure, such as large forgings and castings.
-
Case Hardening:
- Process: Case hardening involves adding carbon or nitrogen to the surface layer of the steel while keeping the core relatively soft. Common methods include carburizing, nitriding, and carbonitriding.
- Purpose: This process creates a hard, wear-resistant surface while maintaining a tough and ductile core, which is ideal for components subjected to high wear and impact.
- Applications: Case hardening is used for gears, shafts, and other components that require a hard surface and a tough core.
-
Martensitic Transformation:
- Process: Martensitic transformation occurs during quenching when the steel is rapidly cooled, transforming the austenite phase into martensite.
- Purpose: This transformation significantly increases the hardness and strength of the steel, but it also makes it more brittle.
- Applications: Martensitic transformation is critical in the production of high-strength, high-hardness components such as cutting tools, knives, and bearings.
-
Stress Relieving:
- Process: Stress relieving involves heating the steel to a temperature below its critical range (typically between 500°F and 1,200°F) and then cooling it slowly.
- Purpose: This process reduces internal stresses caused by machining, welding, or cold working without significantly altering the steel's hardness or strength.
- Applications: Stress relieving is used for components that have undergone significant machining or welding, such as large structural parts and precision components.
-
Precipitation Hardening:
- Process: Precipitation hardening involves heating the steel to a specific temperature to form a supersaturated solid solution, followed by aging at a lower temperature to precipitate fine particles that strengthen the material.
- Purpose: This process increases the strength and hardness of the steel while maintaining good ductility and toughness.
- Applications: Precipitation hardening is used for high-strength alloys in aerospace, automotive, and other high-performance applications.
Each of these heat treatment methods plays a crucial role in tailoring the properties of steel to meet specific application requirements. The choice of method depends on the desired balance of hardness, strength, ductility, and toughness, as well as the specific manufacturing processes involved.
Summary Table:
Process | Temperature Range | Purpose | Applications |
---|---|---|---|
Annealing | 1,500°F - 1,600°F | Softens steel, improves ductility, relieves stress, refines grain structure | Tools, machinery, structural components |
Quenching | Above 1,500°F | Increases hardness and strength by forming martensite | Tools, gears, wear-resistant components |
Tempering | 300°F - 700°F | Reduces brittleness, improves toughness and ductility | Springs, cutting tools, structural parts |
Normalizing | 1,600°F - 1,800°F | Refines grain structure, improves mechanical properties | Large forgings, castings |
Case Hardening | Varies | Creates a hard surface with a tough core | Gears, shafts, wear-resistant components |
Martensitic Transformation | Rapid cooling | Increases hardness and strength, but makes steel brittle | Cutting tools, knives, bearings |
Stress Relieving | 500°F - 1,200°F | Reduces internal stresses without altering hardness | Machined or welded components, precision parts |
Precipitation Hardening | Specific temperatures | Increases strength and hardness while maintaining ductility | Aerospace, automotive, high-performance alloys |
Need help choosing the right heat treatment for your steel components? Contact our experts today to get started!