Ashing in a muffle furnace is a process where a sample is heated in the presence of air until its organic components combust, leaving behind inorganic, non-combustible residue known as ash. This process is critical for various analytical applications, such as determining the inorganic content of materials, analyzing loss on ignition (LOI), or preparing samples for further analysis. The muffle furnace provides a controlled environment for complete combustion, ensuring accurate and reproducible results. Ashing is commonly used in industries like coal, rubber, plastics, and food, as well as in laboratories adhering to international standards like ISO, EN, or ASTM.
Key Points Explained:
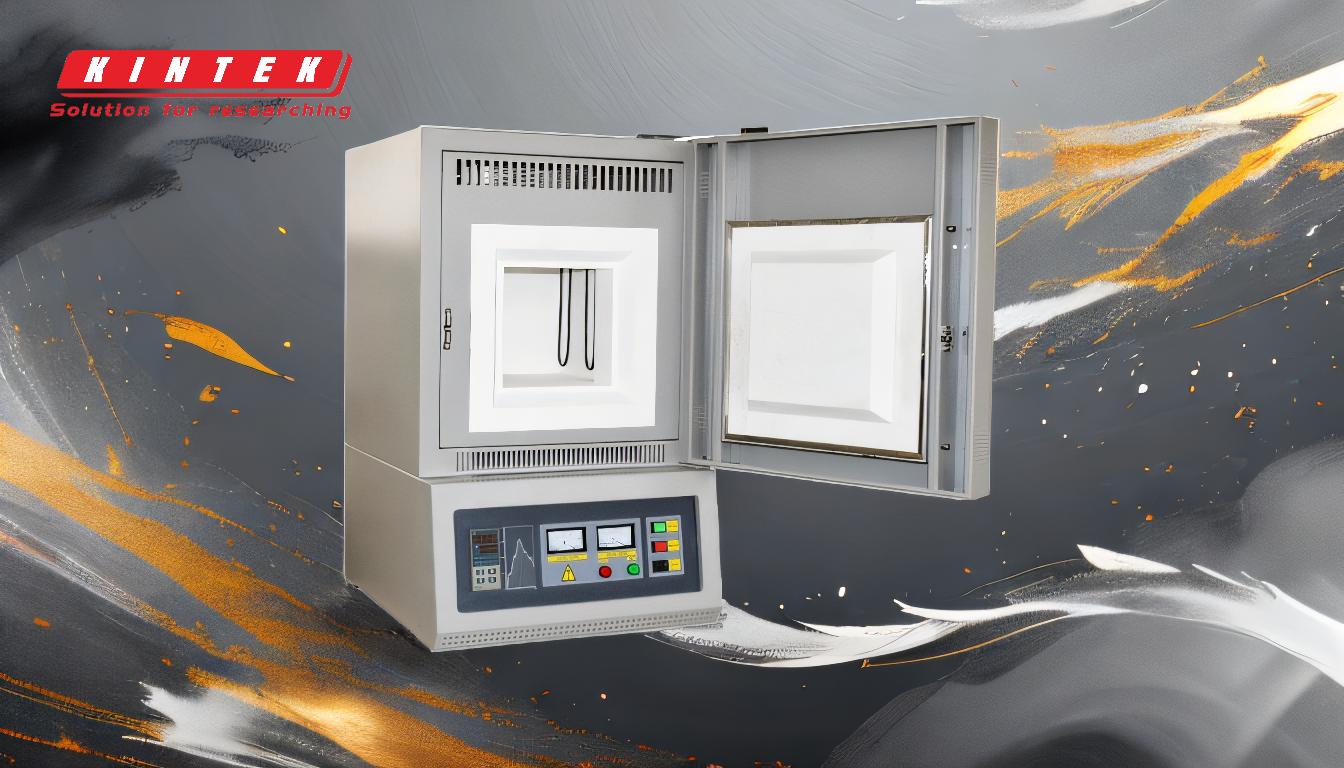
-
Definition of Ashing in a Muffle Furnace:
- Ashing is the process of heating a sample in a muffle furnace to combust its organic components, leaving behind inorganic residue (ash).
- This process is essential for analyzing the inorganic content of materials or preparing samples for further testing.
-
Purpose of Ashing:
- Removal of Organic Material: Ashing expels organic constituents from a sample, ensuring that only inorganic, non-combustible compounds remain.
- Weight Change Analysis: It quantifies the change in weight as organic components are burned away, which is critical for applications like Loss on Ignition (LOI).
- Interference Elimination: In analytical techniques like graphite furnace atomic absorption (AA), ashing removes matrix constituents that could interfere with analyte measurement.
-
Applications of Ashing:
- Material Analysis: Ashing is used to analyze materials such as coal, rubber, plastics, and grain, providing insights into their inorganic composition.
- Compliance with Standards: It is often performed to meet international standards like ISO, EN, or ASTM.
- Sample Preparation: Ashing prepares samples for further analysis by isolating inorganic components.
-
Equipment Used for Ashing:
- Muffle Furnace: A specialized ashing furnace with a heating element enclosed in a chamber, designed to provide controlled heating and combustion.
- Key Components: Includes a chamber, heating element, heat plate, and chamber threshold, all of which are replaceable for maintenance and customization.
- Weighing System: Many ashing furnaces include a scale to measure the sample's weight before, during, and after combustion, enabling precise weight change analysis.
-
Process of Ashing:
- Sample Preparation: The sample is prepared and placed in the muffle furnace.
- Combustion: The furnace heats the sample in the presence of air, causing organic components to combust and leave behind ash.
- Cooling and Weighing: After combustion, the sample is cooled and weighed to determine the weight loss or residual ash content.
-
Importance of Controlled Environment:
- Complete Combustion: The muffle furnace ensures complete combustion by providing a controlled temperature and environment.
- Reproducibility: Consistent heating and controlled conditions ensure reproducible results, which are critical for accurate analysis.
-
Industries and Laboratories Using Ashing:
- Coal Industry: Determines the ash content of coal, which is crucial for quality control.
- Rubber and Plastics: Analyzes the inorganic fillers and additives in these materials.
- Food and Grain: Measures ash content to assess purity and quality.
- Research and Testing Laboratories: Uses ashing for material analysis and compliance with international standards.
By understanding the ashing process, its applications, and the equipment involved, purchasers can make informed decisions about selecting the right muffle furnace for their specific needs.
Summary Table:
Aspect | Details |
---|---|
Definition | Heating a sample to combust organic components, leaving inorganic residue. |
Purpose | Removes organic material, analyzes weight changes, eliminates interference. |
Applications | Material analysis, compliance with standards, sample preparation. |
Equipment | Muffle furnace with chamber, heating element, and weighing system. |
Process | Sample preparation, combustion, cooling, and weighing. |
Industries | Coal, rubber, plastics, food, and testing laboratories. |
Need a muffle furnace for precise ashing? Contact us today to find the right solution for your lab!