Annealing is a heat treatment process used to alter the physical and mechanical properties of metals, making them more ductile and less brittle. The process involves heating the metal to a specific temperature, holding it at that temperature for a set period, and then allowing it to cool slowly. Key components needed for annealing include a heating device (such as a furnace), precise temperature control, and a controlled cooling environment. The process is divided into three stages: Recovery, Recrystallization, and Grain Growth, each of which occurs at specific temperature ranges. Annealing can be performed on various metals, including steel, aluminum, brass, and copper, using specialized equipment like chamber furnaces, atmosphere furnaces, and vacuum furnaces.
Key Points Explained:
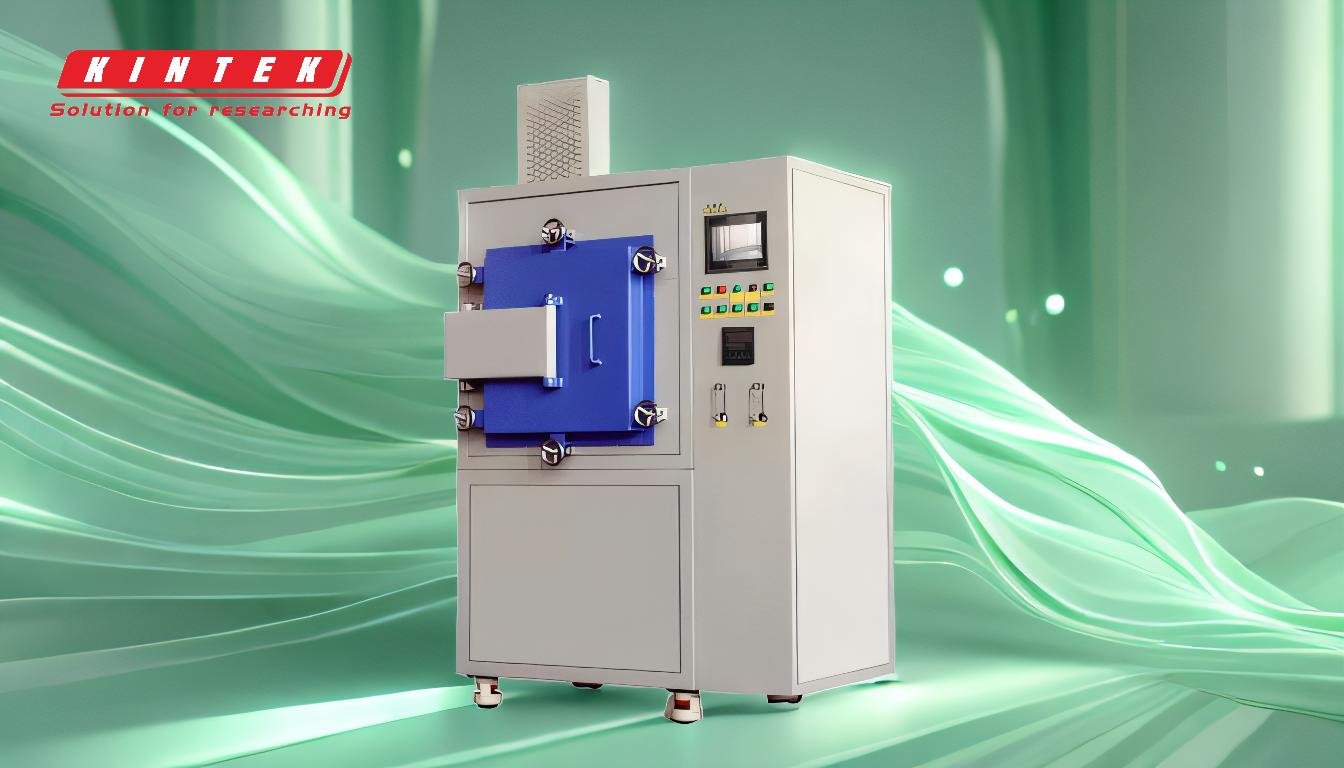
-
Heating Device (Furnace):
- A furnace is the primary equipment required for annealing. It must be capable of reaching and maintaining high temperatures, typically between 700 °C and 900 °C, although some furnaces can exceed 1000 °C.
- The furnace must provide uniform heating to ensure the metal reaches the desired temperature throughout its structure.
- Types of furnaces used include chamber furnaces, atmosphere furnaces, and vacuum furnaces, each suited for specific materials and annealing requirements.
-
Temperature Control:
- Precise temperature control is critical during annealing. The metal must be heated to a temperature where its crystalline structure becomes fluid but remains solid.
- This temperature varies depending on the type of metal being annealed. For example, steel typically requires higher temperatures compared to aluminum or copper.
- Maintaining the correct temperature ensures that defects in the material can repair themselves, leading to improved material properties.
-
Stages of Annealing:
- Recovery: During this stage, the metal is heated to a temperature that relieves internal stresses without changing the grain structure. This stage prepares the metal for the next phases.
- Recrystallization: The metal is heated above its recrystallization temperature, allowing new grains to form without the pre-existing stresses. This stage results in a softer and more ductile material.
- Grain Growth: If the metal is held at the annealing temperature for too long, the grains may grow larger, which can affect the material's mechanical properties. Controlled cooling prevents excessive grain growth.
-
Cooling Process:
- After the metal has been held at the annealing temperature, it must be cooled slowly to room temperature. Rapid cooling can reintroduce stresses and negate the benefits of annealing.
- The cooling rate is carefully controlled to ensure the formation of a ductile crystalline structure, which improves the metal's workability and reduces brittleness.
-
Materials Suitable for Annealing:
- While steel and alloy steel are commonly annealed, other metals such as aluminum, brass, and copper also benefit from the process.
- Each metal has a specific annealing temperature range and cooling rate, which must be adhered to for optimal results.
-
Equipment Variations:
- Chamber Furnaces: These are versatile and can handle a wide range of materials and sizes. They are suitable for batch processing.
- Atmosphere Furnaces: These furnaces control the environment around the metal, preventing oxidation or other chemical reactions during annealing. They are ideal for materials sensitive to atmospheric conditions.
- Vacuum Furnaces: Used for high-purity materials or those that require an oxygen-free environment. Vacuum furnaces are essential for annealing metals that react with air at high temperatures.
-
Applications and Benefits:
- Annealing is used to improve the machinability, ductility, and toughness of metals.
- It is commonly applied in industries such as automotive, aerospace, and manufacturing, where metal components must withstand stress and deformation.
- The process also enhances the electrical conductivity of metals like copper, making it valuable in electrical and electronic applications.
By understanding these key points, an equipment or consumable purchaser can make informed decisions about the type of furnace and annealing process required for specific materials and applications.
Summary Table:
Key Aspect | Details |
---|---|
Heating Device | Furnace (chamber, atmosphere, vacuum) capable of 700–1000 °C uniform heating |
Temperature Control | Precise heating to metal-specific annealing temperatures |
Stages of Annealing | Recovery, Recrystallization, Grain Growth |
Cooling Process | Slow cooling to room temperature to prevent stress reintroduction |
Materials | Steel, aluminum, brass, copper |
Equipment Variations | Chamber, atmosphere, and vacuum furnaces for specific needs |
Applications | Automotive, aerospace, manufacturing, electrical industries |
Ready to optimize your metal properties with annealing? Contact our experts today for tailored solutions!