Sintering is a thermal process used to transform powdered materials into dense, solid bodies by heating them to temperatures below their melting point. This process involves three main stages: powder preparation, compaction, and heating. During heating, particles bond through solid-state diffusion, leading to densification, pore elimination, and increased strength. The sintering cycle is critical in industries like metallurgy and ceramics, as it imparts the final product with its desired mechanical, thermal, and structural properties. Understanding the sintering cycle is essential for optimizing material performance and achieving consistent quality in manufacturing processes.
Key Points Explained:
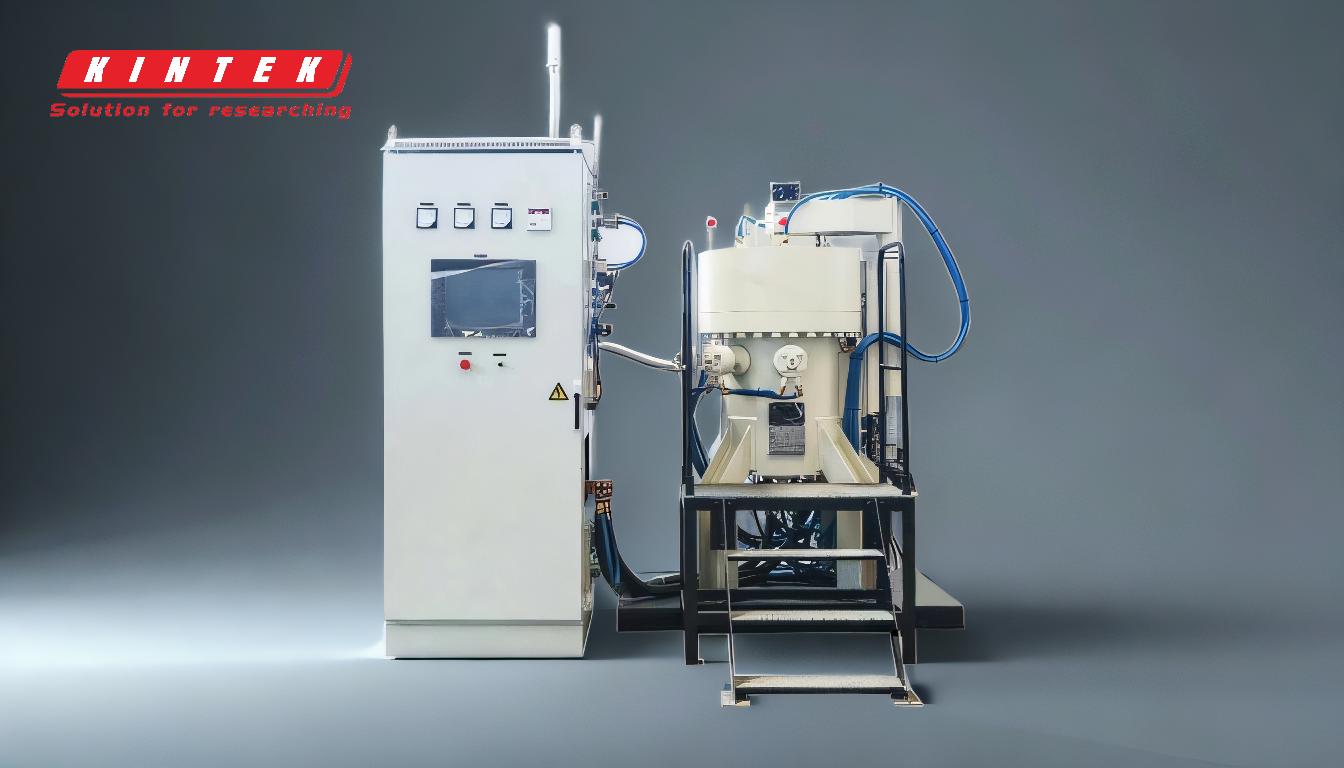
-
Definition of Sintering:
- Sintering is a thermal process where powdered materials are heated to temperatures below their melting point to create a dense, solid body.
- It involves the mutual bonding of particles through solid-state diffusion, leading to densification and strength increase.
-
Purpose of Sintering:
- To transform powdered materials into a cohesive, dense structure.
- To impart the material with its characteristic properties, such as strength, durability, and thermal resistance.
- To eliminate pores and achieve volume shrinkage, resulting in a uniform and robust final product.
-
Stages of the Sintering Process:
-
Powder Preparation (Composing):
- Involves mixing raw materials, such as metal or ceramic powders, with additives like binders, deflocculants, and water to create a slurry.
- The slurry is often spray-dried to form a uniform powder ready for compaction.
-
Compaction:
- The powder is pressed into a desired shape using cold or hot mold pressing to create a "green part."
- Compaction ensures uniformity and eliminates voids, preparing the material for sintering.
-
Heating (Sintering Cycle):
- The green part is heated in a furnace (tunnel kiln or periodic kiln) to a temperature below the melting point.
- During heating, particles bond through diffusion, forming necks and densifying the material.
- The process involves three phases: heating, sintering, and cooling, ensuring uniform strength and durability.
-
Powder Preparation (Composing):
-
Detailed Sintering Cycle:
-
Initial Stage:
- Materials are heated to induce the formation of crystalline structures without complete compaction.
- This stage sets the foundation for particle bonding and densification.
-
Intermediate Stage:
- Particle density increases, and particles merge through methods like transient or permanent liquid phase sintering.
- This stage is critical for achieving the desired material properties and eliminating porosity.
-
Final Stage:
- The material becomes mostly solid, with any remaining pores filled by liquid or binder additives.
- The final product is cooled to solidify into a rigid and cohesive structure.
-
Initial Stage:
-
Key Factors Influencing Sintering:
-
Temperature Control:
- Precise temperature regulation is essential to ensure particle bonding without complete melting.
-
Time:
- The duration of heating affects the extent of particle diffusion and densification.
-
Atmosphere:
- The sintering environment (e.g., inert gas, vacuum) can influence the final material properties.
-
Material Composition:
- The type and proportion of raw materials and additives determine the sintering behavior and final product characteristics.
-
Temperature Control:
-
Applications of Sintering:
-
Metallurgy:
- Used to produce metal parts with high strength and durability, such as gears, bearings, and filters.
-
Ceramics:
- Essential for manufacturing ceramic components like tiles, insulators, and cutting tools.
-
Advanced Materials:
- Applied in the production of composites, superconductors, and other high-performance materials.
-
Metallurgy:
-
Advantages of Sintering:
- Enables the production of complex shapes with high precision.
- Reduces material waste compared to traditional manufacturing methods.
- Enhances material properties, such as strength, wear resistance, and thermal stability.
By understanding the sintering cycle and its stages, manufacturers can optimize the process to achieve consistent quality and performance in their products. This knowledge is particularly valuable for equipment and consumable purchasers, as it helps in selecting the right materials and processes for specific applications.
Summary Table:
Aspect | Details |
---|---|
Definition | A thermal process bonding powdered materials below melting point. |
Purpose | Creates dense, strong, and uniform materials with enhanced properties. |
Stages | 1. Powder Preparation 2. Compaction 3. Heating (Sintering Cycle) |
Key Factors | Temperature, time, atmosphere, and material composition. |
Applications | Metallurgy, ceramics, advanced materials (e.g., composites, superconductors). |
Advantages | Precise shapes, reduced waste, improved strength, and thermal stability. |
Optimize your manufacturing process with sintering—contact our experts today to learn more!