Heat treatment is a critical process in metallurgy that significantly influences the corrosion resistance of metals and alloys. By altering the microstructure through controlled heating and cooling, heat treatment can enhance or degrade a material's ability to withstand corrosive environments. The effect of heat treatment on corrosion resistance depends on factors such as the type of material, the specific heat treatment process, and the corrosive environment. For instance, processes like annealing, quenching, and tempering can refine grain structure, reduce internal stresses, and improve homogeneity, all of which contribute to better corrosion resistance. Conversely, improper heat treatment can lead to microstructural defects, such as grain boundary segregation or residual stresses, which may increase susceptibility to corrosion. Understanding the relationship between heat treatment and corrosion resistance is essential for optimizing material performance in applications where durability and longevity are paramount.
Key Points Explained:
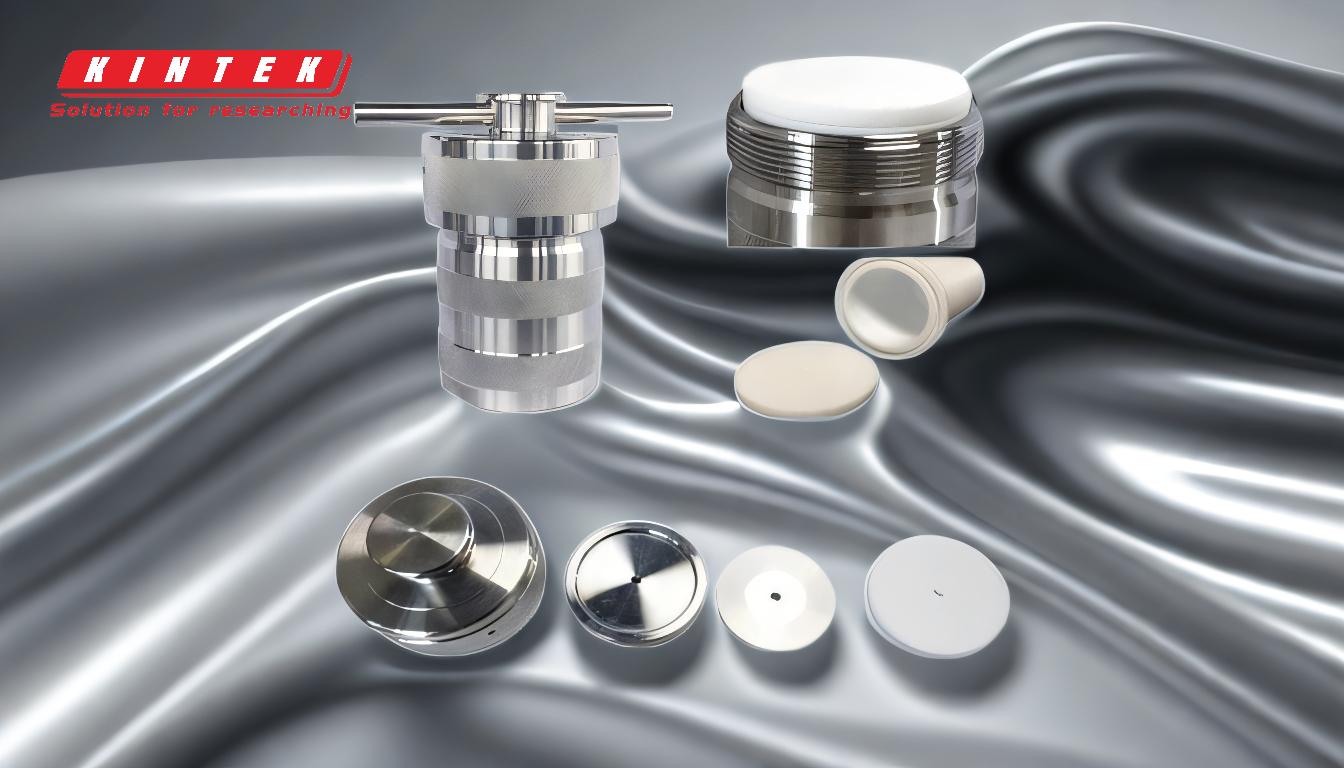
-
Microstructural Changes and Corrosion Resistance:
- Heat treatment alters the microstructure of metals, which directly impacts their corrosion resistance. For example, annealing can soften the material and reduce internal stresses, leading to a more uniform microstructure that resists corrosion better. On the other hand, quenching can create a harder but more brittle structure, which might be more prone to stress corrosion cracking.
- Grain size refinement through heat treatment often improves corrosion resistance by reducing the number of grain boundaries, which are typically more susceptible to corrosion.
-
Effect of Different Heat Treatment Processes:
- Annealing: This process involves heating the material to a specific temperature and then slowly cooling it. Annealing can improve corrosion resistance by reducing internal stresses and creating a more homogeneous microstructure.
- Quenching and Tempering: Quenching rapidly cools the metal, creating a hard but potentially brittle structure. Tempering, which follows quenching, reduces brittleness and can improve corrosion resistance by relieving internal stresses and refining the microstructure.
- Solution Treatment: Often used for alloys, this process involves heating the material to dissolve secondary phases and then rapidly cooling it to maintain a single-phase structure. This can enhance corrosion resistance by eliminating microstructural inhomogeneities that might act as corrosion initiation sites.
-
Role of Residual Stresses:
- Residual stresses introduced during heat treatment can significantly affect corrosion resistance. Tensile residual stresses, often resulting from rapid cooling, can increase susceptibility to stress corrosion cracking. Conversely, compressive residual stresses, which can be introduced through processes like shot peening after heat treatment, generally improve corrosion resistance by closing surface pores and cracks.
-
Material-Specific Considerations:
- Different materials respond differently to heat treatment. For example, stainless steels benefit from heat treatment processes that enhance the formation of a protective chromium oxide layer, thereby improving corrosion resistance. In contrast, aluminum alloys may require specific heat treatments to avoid sensitization, which can lead to intergranular corrosion.
-
Environmental Factors:
- The effectiveness of heat treatment in improving corrosion resistance also depends on the corrosive environment. For instance, in chloride-rich environments, materials with a refined grain structure and minimal residual stresses tend to perform better. Understanding the specific environmental conditions is crucial for selecting the appropriate heat treatment process.
-
Practical Applications and Optimization:
- In industries such as aerospace, automotive, and marine engineering, optimizing heat treatment processes is essential for ensuring long-term durability and performance. For example, in marine environments, where materials are exposed to saltwater, heat treatment processes that enhance the formation of protective oxide layers and reduce residual stresses are particularly beneficial.
By carefully selecting and controlling heat treatment processes, engineers and metallurgists can significantly enhance the corrosion resistance of metals and alloys, thereby extending their service life and improving performance in demanding applications.
Summary Table:
Aspect | Impact on Corrosion Resistance |
---|---|
Microstructural Changes | Refines grain structure, reduces internal stresses, and improves homogeneity for better resistance. |
Annealing | Reduces internal stresses and creates a uniform microstructure, enhancing corrosion resistance. |
Quenching & Tempering | Hardens material but may increase brittleness; tempering reduces brittleness and improves resistance. |
Residual Stresses | Tensile stresses increase corrosion susceptibility; compressive stresses improve resistance. |
Material-Specific Effects | Stainless steels benefit from protective oxide layers; aluminum alloys require careful treatment. |
Environmental Factors | Corrosive environments like chloride-rich areas demand refined grain structures for better performance. |
Optimize your material's corrosion resistance with expert heat treatment solutions—contact us today!