The refractory material in a muffle furnace is primarily designed to withstand high temperatures, resist chemical corrosion, and ensure durability and effective heat transfer. Common materials used include alumina (Al₂O₃), silicon carbide (SiC), zirconia board, and high alumina bricks. These materials are chosen based on their ability to endure specific temperature ranges, such as ceramic tiles for up to 1200°C, zirconia board for up to 1600°C, and high alumina bricks for up to 1800°C. Additionally, advanced materials like oxy-nitride bonded SiC are used for specialized applications, offering excellent heating performance and long service life. The choice of refractory material depends on the furnace's operating temperature and the specific requirements of the process.
Key Points Explained:
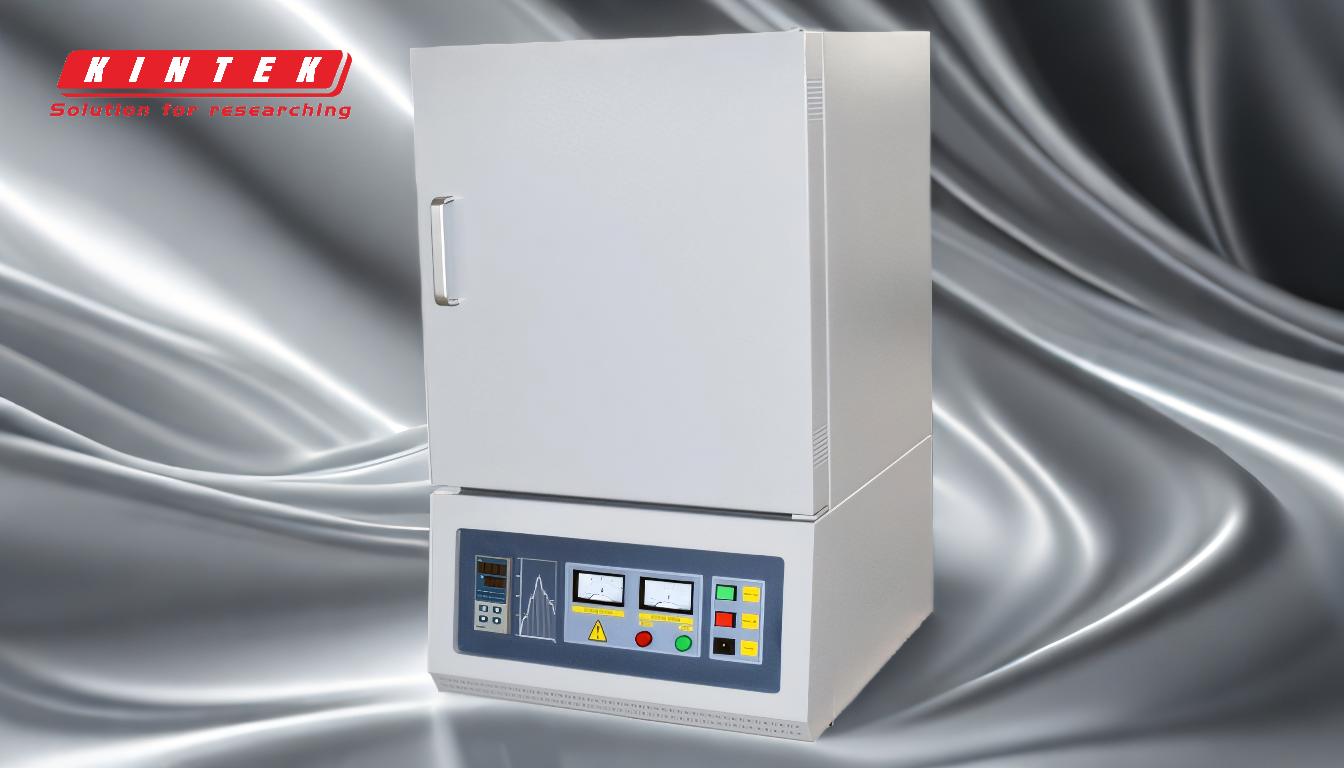
-
Primary Refractory Materials:
- Alumina (Al₂O₃): A widely used ceramic material in muffle furnaces due to its high melting point, excellent thermal stability, and resistance to chemical corrosion. It is ideal for applications requiring temperatures up to 1800°C.
- Silicon Carbide (SiC): Known for its exceptional thermal conductivity, mechanical strength, and resistance to thermal shock. Advanced forms like oxy-nitride bonded SiC are used for specialized applications, such as the radiant roof in ZnO production furnaces.
- Zirconia Board: Used for applications requiring temperatures up to 1600°C, zirconia offers excellent thermal insulation and resistance to thermal shock.
- High Alumina Bricks: These bricks are used for high-temperature applications, up to 1800°C, due to their high strength and thermal stability.
-
Temperature-Specific Materials:
- Ceramic Tiles: Suitable for temperatures up to 1200°C, ceramic tiles are commonly used in the inner chamber of muffle furnaces for their durability and heat resistance.
- Zirconia Board: Used for higher temperature applications, up to 1600°C, due to its superior thermal insulation properties.
- High Alumina Bricks: These are used for the highest temperature applications, up to 1800°C, providing excellent thermal stability and resistance to chemical corrosion.
-
Specialized Applications:
- Oxy-Nitride Bonded SiC: This advanced material is used in specialized applications, such as the radiant roof in muffle furnaces for ZnO production. It offers excellent heating performance and a long, reliable service life.
- Heat-Resisting Stainless Steel or Inconel: Used for muffles in sintering furnaces, depending on customer requirements, these materials offer high-temperature resistance and durability.
-
Construction and Insulation:
- Inner Chamber: The inner chamber of a muffle furnace is typically made of ceramic materials like alumina or zirconia, which can withstand high temperatures and ensure effective heat transfer.
- Insulation: The furnace is insulated to prevent heat loss during operation, ensuring efficient and uniform heating.
-
Material Selection Criteria:
- Temperature Range: The choice of refractory material depends on the operating temperature of the furnace. Different materials are used for different temperature ranges, from 1200°C to 1800°C.
- Chemical Resistance: Materials must resist chemical corrosion, especially in processes involving reactive substances.
- Thermal Stability: High thermal stability is crucial to prevent material degradation at high temperatures.
- Durability: The material must have a long service life to ensure the furnace's reliability and reduce maintenance costs.
By understanding these key points, a purchaser can make informed decisions about the appropriate refractory materials for their specific muffle furnace applications, ensuring optimal performance and longevity.
Summary Table:
Material | Temperature Range | Key Properties |
---|---|---|
Alumina (Al₂O₃) | Up to 1800°C | High melting point, thermal stability |
Silicon Carbide (SiC) | Up to 1600°C | Thermal conductivity, mechanical strength |
Zirconia Board | Up to 1600°C | Thermal insulation, shock resistance |
High Alumina Bricks | Up to 1800°C | High strength, thermal stability |
Ceramic Tiles | Up to 1200°C | Durability, heat resistance |
Need help choosing the right refractory material for your muffle furnace? Contact our experts today!