Annealing is a heat treatment process used to alter the physical and sometimes chemical properties of a material to increase its ductility and reduce its hardness, making it more workable. The temperature and time for annealing depend on the material being treated, its initial condition, and the desired final properties. Generally, annealing involves heating the material to a specific temperature, holding it at that temperature for a certain period, and then cooling it slowly. For metals, the annealing temperature is typically between 50% to 75% of the melting point, and the holding time can range from a few minutes to several hours, depending on the material's thickness and composition.
Key Points Explained:
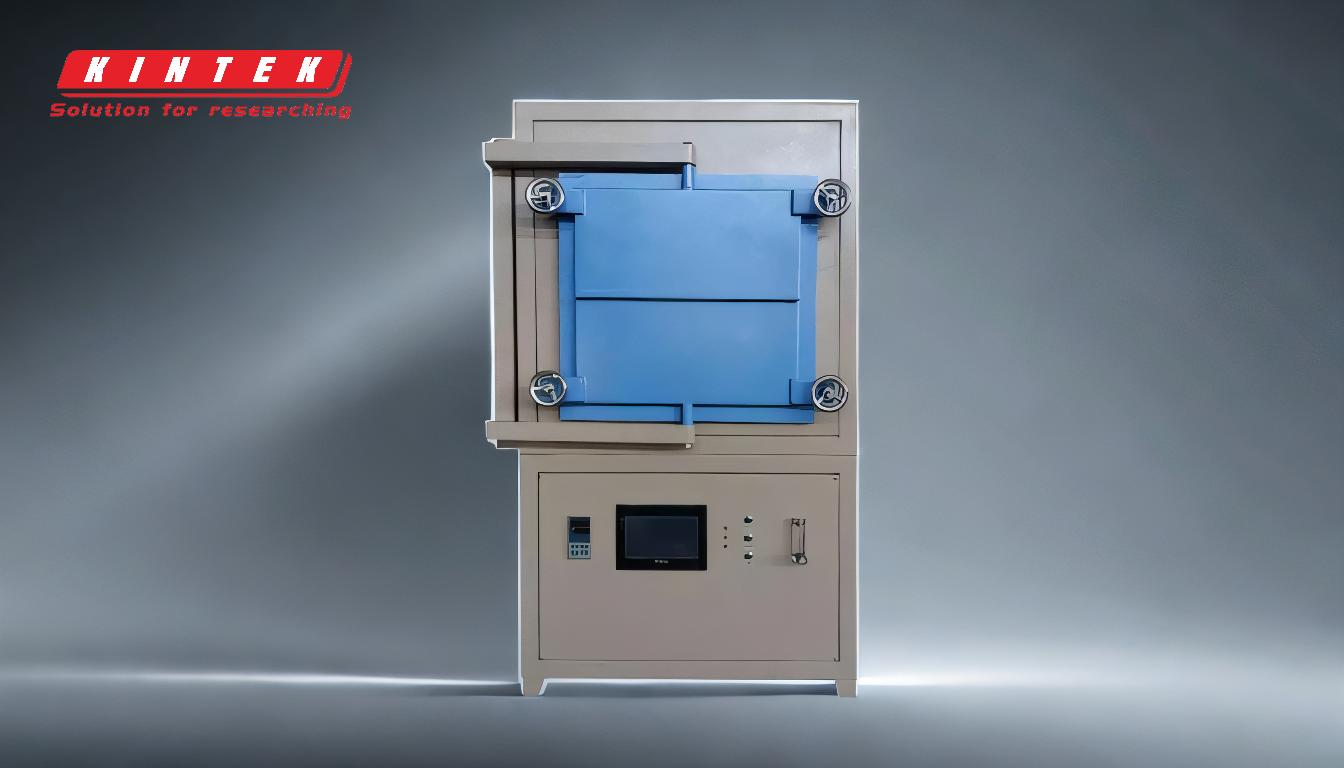
-
Material-Specific Annealing Temperatures:
- Metals: The annealing temperature for metals is usually set between 50% to 75% of their melting point. For example, steel might be annealed at around 700°C to 900°C, while aluminum alloys are typically annealed at lower temperatures, around 300°C to 400°C.
- Glass: For glass, annealing temperatures are much lower, typically around 500°C to 550°C, to relieve internal stresses without causing deformation.
- Polymers: Annealing temperatures for polymers are close to their glass transition temperatures, which can be as low as 60°C to 100°C for some plastics.
-
Holding Time:
- The holding time at the annealing temperature is crucial for achieving the desired material properties. It allows the material to reach a uniform temperature throughout and for the necessary microstructural changes to occur.
- For thin materials, the holding time might be as short as a few minutes. For thicker materials or those requiring significant microstructural changes, the holding time can extend to several hours.
- In some cases, such as with certain alloys, the material may need to be held at the annealing temperature for a specific time to achieve the desired grain size or to allow for the diffusion of alloying elements.
-
Cooling Rate:
- The cooling rate after annealing is just as important as the heating and holding phases. Slow cooling is generally preferred to prevent the reintroduction of stresses and to allow the material to reach a stable, stress-free state.
- For metals, cooling is often done in the furnace itself (furnace cooling) or in still air. For glass, controlled cooling in an annealing lehr is typical to ensure even temperature reduction and stress relief.
-
Purpose of Annealing:
- Stress Relief: Annealing helps to relieve internal stresses that may have been introduced during manufacturing processes like welding, machining, or cold working.
- Softening: It increases the material's ductility, making it easier to shape or form without cracking.
- Improving Machinability: By reducing hardness, annealing can make materials easier to machine.
- Enhancing Electrical Properties: For some materials, annealing can improve electrical conductivity by allowing for better grain alignment and reduced defects.
-
Equipment Used:
- Furnaces: Various types of furnaces are used for annealing, including batch furnaces, continuous furnaces, and vacuum furnaces, depending on the material and the scale of production.
- Annealing Lehrs: Specifically for glass, annealing lehrs are used to control the cooling rate precisely.
Understanding the specific requirements for temperature and time in annealing is crucial for achieving the desired material properties. The process must be carefully controlled to ensure that the material does not become too soft or that undesirable microstructural changes do not occur. Each material and application may require a tailored annealing process to achieve optimal results.
Summary Table:
Material | Annealing Temperature | Holding Time | Cooling Rate |
---|---|---|---|
Metals | 50%-75% of melting point | Few minutes to hours | Slow (furnace or air) |
Glass | 500°C-550°C | Controlled | Annealing lehr |
Polymers | Near glass transition | Minutes to hours | Controlled slow cooling |
Need help optimizing your annealing process? Contact our experts today for tailored solutions!