Heating elements are critical components in various applications, from household appliances to industrial furnaces. The choice of metal for heating elements depends on factors such as resistivity, melting point, oxidation resistance, and cost. Nickel-Chrome (NiCr) alloys are the most commonly used due to their affordability, high resistance, and stability in air at high temperatures. For high-temperature applications, exotic materials like molybdenum, tungsten, and silicon carbide are preferred. Other materials like iron-chrome aluminum alloys and graphite are also used, depending on the specific requirements of the application.
Key Points Explained:
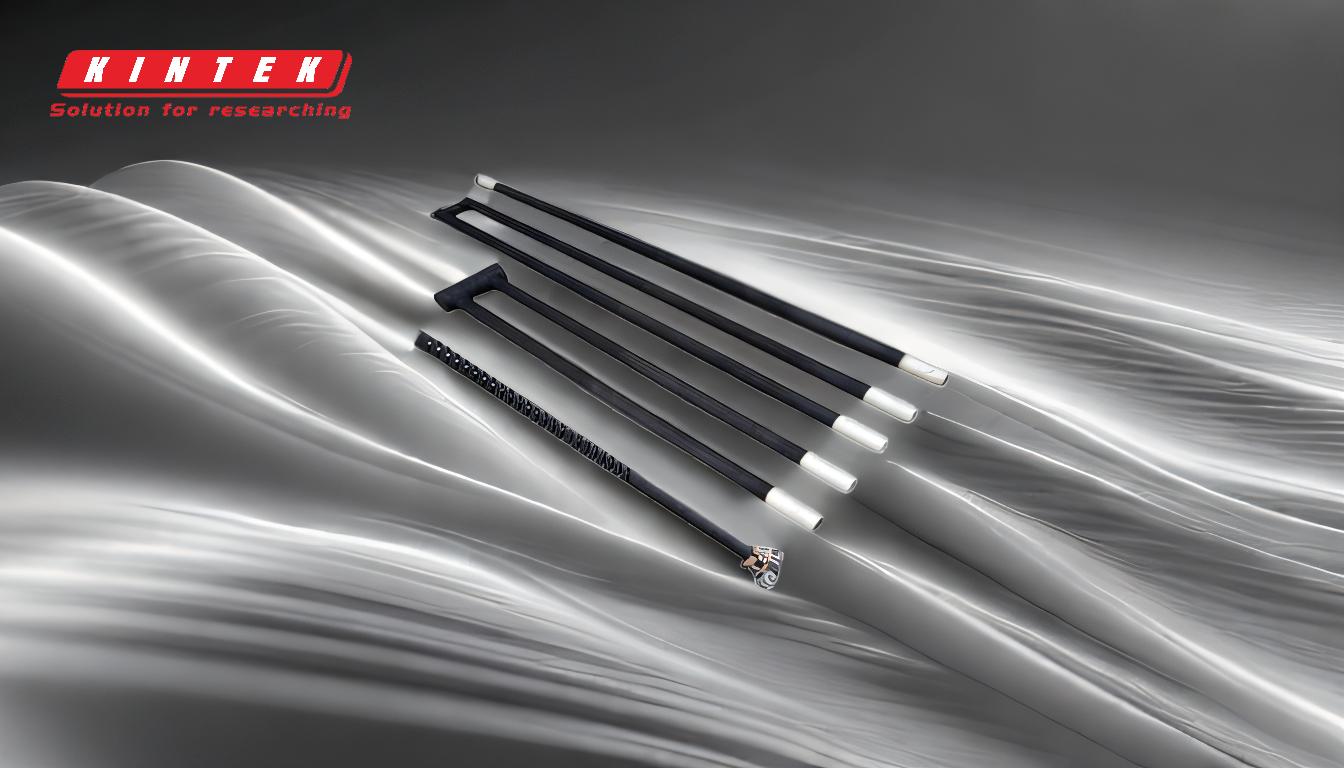
-
Nickel-Chrome (NiCr) Alloys:
- Properties: High resistivity, relatively high melting point, and resistance to oxidation in air.
- Applications: Widely used in household appliances like toasters, hair dryers, and industrial applications such as floor heating and pathway heating.
- Advantages: Cost-effective, durable, and suitable for a wide range of temperatures.
-
Exotic Materials for High-Temperature Applications:
- Materials: Platinum, tungsten disilicide, molybdenum disilicide, molybdenum, and silicon carbide.
- Properties: Extremely high melting points and excellent oxidation resistance.
- Applications: Used in high-temperature industrial furnaces where standard materials would fail.
- Advantages: Can withstand very high temperatures, making them ideal for specialized industrial processes.
-
Iron-Chrome Aluminum Alloys:
- Properties: High resistivity, good oxidation resistance, and high melting point.
- Applications: Commonly used in industrial furnaces, often shaped into cylindrical, semi-circular, or flat panels.
- Advantages: Cost-effective and durable, suitable for high-temperature environments.
-
Graphite and Molybdenum:
- Properties: High thermal conductivity, high melting point, and resistance to thermal shock.
- Applications: Used in lightweight curved heating elements and high-temperature furnaces.
- Advantages: Lightweight and efficient, with options for pure or lanthanated molybdenum strips.
-
General Requirements for Heating Element Materials:
- High Resistivity: Ensures that a small length of wire can produce the required heat.
- High Melting Point: Allows the material to withstand high temperatures without melting.
- Low Temperature Coefficient: Ensures that the resistance does not vary significantly with temperature changes.
- Oxidation Resistance: Ensures the material can withstand high temperatures without frequent replacement.
-
Non-Metallic Materials:
- Materials: Graphite, silicon carbide, and molybdenum dioxide.
- Properties: High resistivity, high melting points, and resistance to oxidation.
- Applications: Used in specialized high-temperature applications where metallic materials may not be suitable.
- Advantages: Can operate at very high temperatures and are resistant to thermal shock.
By understanding the properties and applications of these materials, one can select the appropriate metal for heating elements based on the specific requirements of the application.
Summary Table:
Material | Properties | Applications | Advantages |
---|---|---|---|
Nickel-Chrome (NiCr) | High resistivity, high melting point, oxidation resistance | Household appliances (toasters, hair dryers), industrial heating | Cost-effective, durable, wide temperature range |
Exotic Materials | Extremely high melting points, excellent oxidation resistance | High-temperature industrial furnaces | Ideal for specialized high-temperature processes |
Iron-Chrome Aluminum | High resistivity, good oxidation resistance, high melting point | Industrial furnaces (cylindrical, semi-circular, flat panels) | Cost-effective, durable, high-temperature suitability |
Graphite & Molybdenum | High thermal conductivity, high melting point, resistance to thermal shock | Lightweight curved heating elements, high-temperature furnaces | Lightweight, efficient, pure or lanthanated options |
Non-Metallic Materials | High resistivity, high melting points, oxidation resistance | Specialized high-temperature applications | Operate at very high temperatures, resistant to thermal shock |
Need help choosing the right heating element material? Contact our experts today for tailored solutions!