Smelting is a critical process in metallurgy, and the choice of furnace depends on the type of metal being processed, the scale of production, and the desired quality of the final product. The most common types of furnaces used for smelting include blast furnaces, induction furnaces, crucible furnaces, and electric arc furnaces. Each type has its unique advantages and is suited for specific applications. For instance, blast furnaces are ideal for large-scale production of pig iron, while induction furnaces offer precise temperature control and are environmentally friendly. Understanding the strengths and limitations of each furnace type is essential for selecting the right equipment for smelting operations.
Key Points Explained:
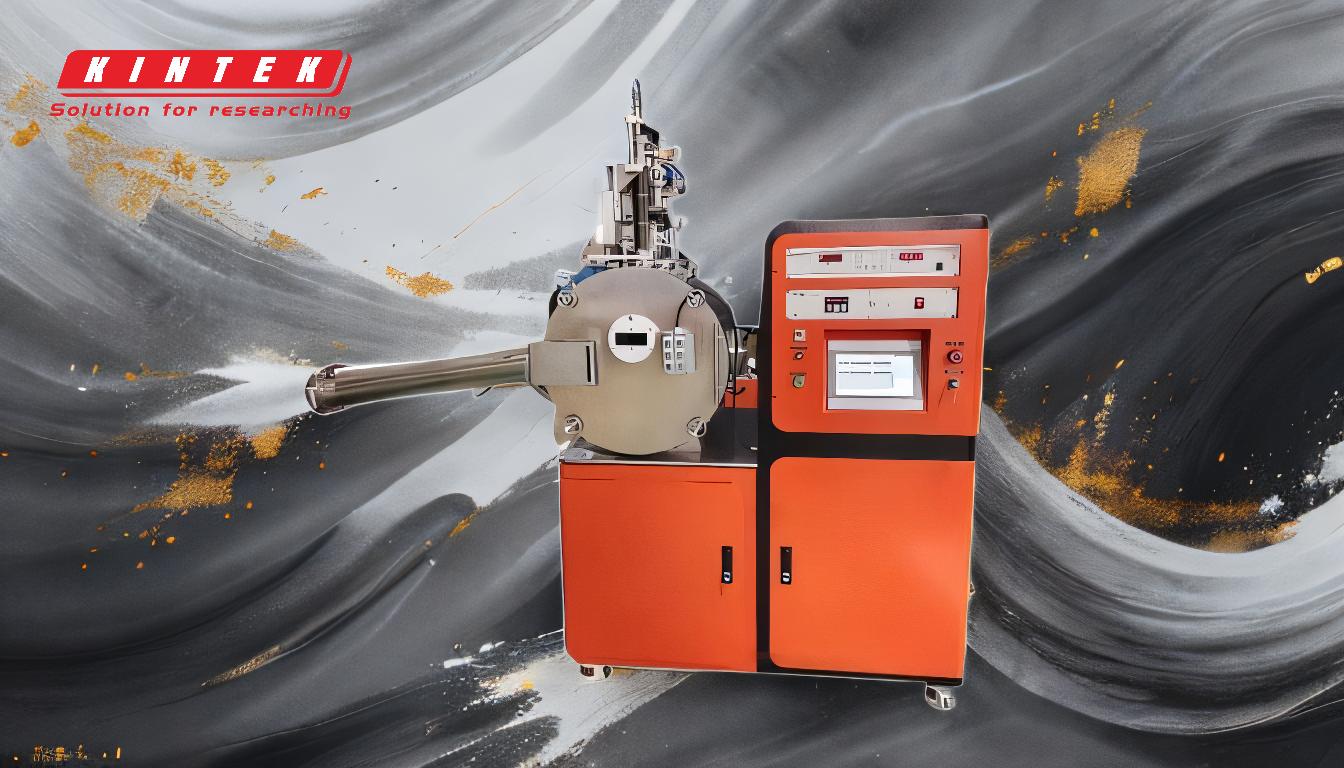
-
Blast Furnace:
- A blast furnace is primarily used for smelting industrial metals such as pig iron, lead, or copper.
- It operates by supplying combustion air above atmospheric pressure, which facilitates the reduction of metal ores.
- This type of furnace is ideal for large-scale production due to its high efficiency and ability to handle significant volumes of raw materials.
- However, blast furnaces are less suitable for smaller-scale operations or when precise temperature control is required.
-
Induction Furnace:
- Induction furnaces use alternating electric currents to generate heat and melt metals.
- They are known for their lower system impedance compared to electric arc furnaces, which translates to better energy efficiency.
- Induction furnaces have minimal environmental impact, producing less noise and emissions, making them a more eco-friendly option.
- They offer uniform steel composition and temperature, which is crucial for producing high-quality metal.
- These furnaces are also easier to automate, reducing the need for manual intervention and improving operational efficiency.
-
Crucible Furnace:
- Crucible furnaces use refractory materials to withstand the high temperatures required for smelting.
- They are typically used for small-scale operations or for melting metals that require precise temperature control.
- Crucible furnaces are versatile and can handle a variety of metals, but they are not suitable for large-scale production due to their limited capacity.
-
Electric Arc Furnace:
- Electric arc furnaces use electrodes to generate heat for melting metals.
- They are highly efficient and can reach very high temperatures, making them suitable for melting a wide range of metals, including steel.
- Electric arc furnaces are often used in recycling operations, as they can melt scrap metal efficiently.
- However, they can be more expensive to operate due to the high energy consumption and the need for regular maintenance of the electrodes.
In summary, the choice of furnace for smelting depends on the specific requirements of the operation, including the type of metal, the scale of production, and environmental considerations. Blast furnaces are ideal for large-scale production of pig iron, while induction furnaces offer precise temperature control and are environmentally friendly. Crucible furnaces are suitable for small-scale operations, and electric arc furnaces are highly efficient for melting a wide range of metals, including steel.
Summary Table:
Furnace Type | Best For | Key Advantages | Limitations |
---|---|---|---|
Blast Furnace | Large-scale pig iron production | High efficiency, handles large volumes | Less precise temperature control |
Induction Furnace | Precise temperature control | Eco-friendly, uniform steel composition | Higher initial cost |
Crucible Furnace | Small-scale, precise operations | Versatile, precise temperature control | Limited capacity for large-scale use |
Electric Arc Furnace | Melting a wide range of metals | Highly efficient, suitable for recycling | High energy consumption, maintenance |
Need help choosing the right furnace for your smelting needs? Contact our experts today for personalized advice!