Choosing the right calcination temperature is a critical step in ensuring the desired material properties and performance. The calcination temperature directly influences the chemical and physical transformations of the material, such as decomposition, phase transitions, and crystallization. To determine the appropriate calcination temperature, one must consider the material's thermal stability, the desired phase or structure, and the equipment's capabilities. Below is a detailed explanation of the key factors to consider when selecting the calcination temperature.
Key Points Explained:
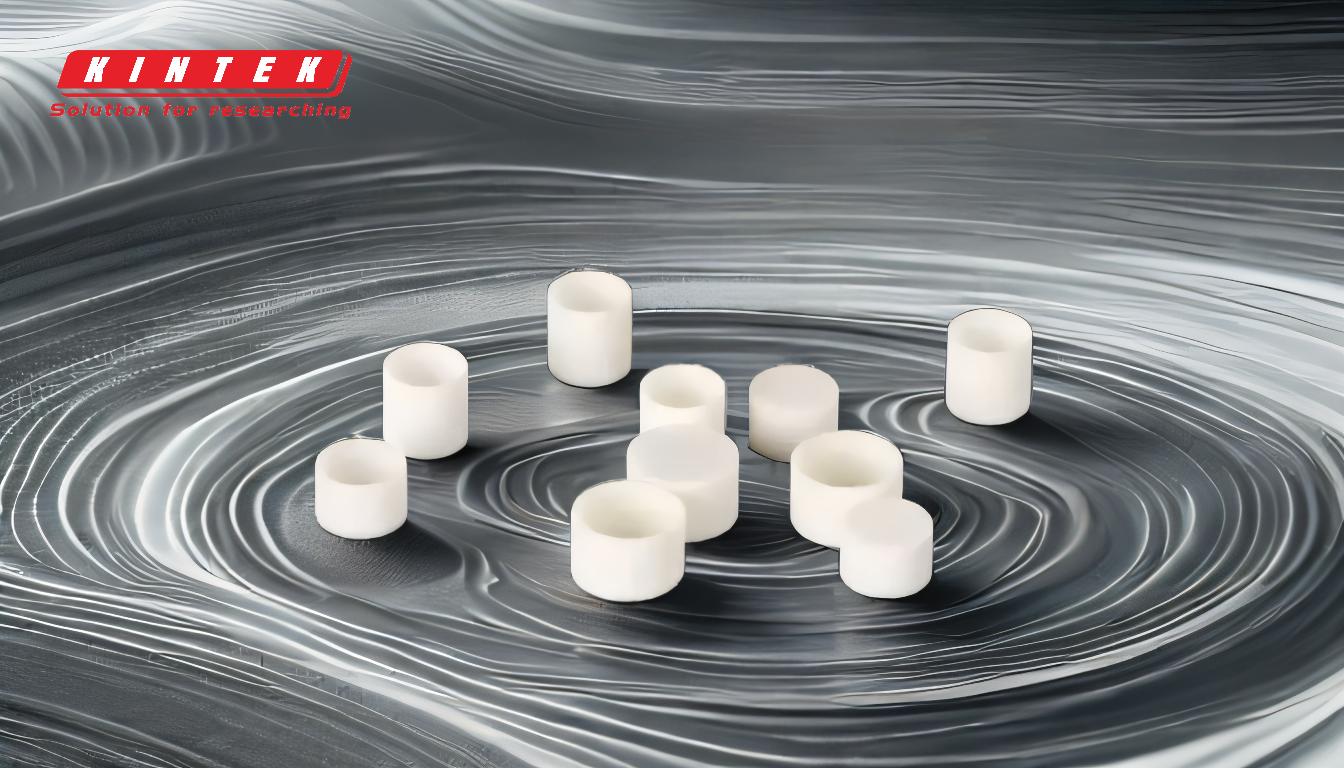
-
Understand the Material's Thermal Behavior
- Thermal Decomposition Temperature: Determine the temperature at which the material undergoes decomposition or phase changes. This can be identified through techniques like Thermogravimetric Analysis (TGA) or Differential Scanning Calorimetry (DSC).
- Phase Transition Temperature: Identify the temperature range where the material transitions into the desired crystalline or amorphous phase.
- Thermal Stability: Ensure the material does not degrade or lose its intended properties at the chosen calcination temperature.
-
Define the Desired Outcome
- Phase Purity: If the goal is to achieve a specific crystalline phase, the calcination temperature must align with the phase formation temperature.
- Particle Size and Morphology: Higher temperatures may lead to grain growth or sintering, while lower temperatures may result in incomplete reactions.
- Chemical Composition: Ensure the calcination temperature does not cause unwanted reactions or loss of volatile components.
-
Consider Equipment Limitations
- Furnace Temperature Range: The maximum temperature of the furnace should exceed the required calcination temperature by 100–200°C to ensure consistent performance and avoid operating at the furnace's upper limit.
- Heating Rate and Uniformity: The furnace should provide uniform heating and precise temperature control to avoid thermal gradients that could affect the material's properties.
- Atmosphere Control: If the calcination requires a specific atmosphere (e.g., inert, oxidizing, or reducing), ensure the furnace can maintain the required conditions.
-
Optimize Through Experimental Trials
- Pilot Experiments: Conduct small-scale experiments to test different calcination temperatures and durations. Analyze the resulting material properties to identify the optimal temperature.
- Iterative Refinement: Adjust the temperature based on experimental results, considering factors like yield, phase purity, and particle size.
- Characterization: Use techniques like X-ray Diffraction (XRD), Scanning Electron Microscopy (SEM), and Fourier Transform Infrared Spectroscopy (FTIR) to evaluate the material after calcination.
-
Account for Practical Constraints
- Energy Efficiency: Higher temperatures may increase energy consumption and operational costs. Balance the desired material properties with energy efficiency.
- Safety Considerations: Ensure the chosen temperature is within the safe operating range of the equipment and does not pose risks such as overheating or material degradation.
- Scalability: Consider whether the chosen temperature can be consistently achieved in larger-scale production.
-
Reference Industry Standards and Literature
- Published Research: Review studies on similar materials to identify commonly used calcination temperatures and their outcomes.
- Manufacturer Recommendations: Consult equipment manufacturers for guidance on optimal operating temperatures for specific materials.
- Historical Data: If applicable, use data from previous experiments or production runs to inform the decision.
By carefully considering these factors, you can select a calcination temperature that achieves the desired material properties while ensuring efficient and safe operation. The process involves a combination of theoretical understanding, experimental validation, and practical considerations to optimize the calcination conditions.
Summary Table:
Key Factor | Description |
---|---|
Material's Thermal Behavior | Identify decomposition, phase transition, and thermal stability temperatures. |
Desired Outcome | Define phase purity, particle size, morphology, and chemical composition goals. |
Equipment Limitations | Consider furnace temperature range, heating rate, uniformity, and atmosphere. |
Experimental Trials | Conduct pilot experiments and refine temperature iteratively. |
Practical Constraints | Balance energy efficiency, safety, and scalability. |
Industry Standards | Reference research, manufacturer recommendations, and historical data. |
Need help selecting the perfect calcination temperature? Contact our experts today for tailored guidance!