Cold working metal is a process that involves shaping or deforming metal at room temperature, which enhances its mechanical properties without the need for heating. This method is widely used in industries due to its ability to improve strength, hardness, and dimensional accuracy while maintaining the metal's ductility and toughness. It also allows for precise control over the final product's shape and surface finish, making it ideal for applications requiring high precision and durability. Additionally, cold working is cost-effective and energy-efficient since it avoids the high temperatures required in hot working processes.
Key Points Explained:
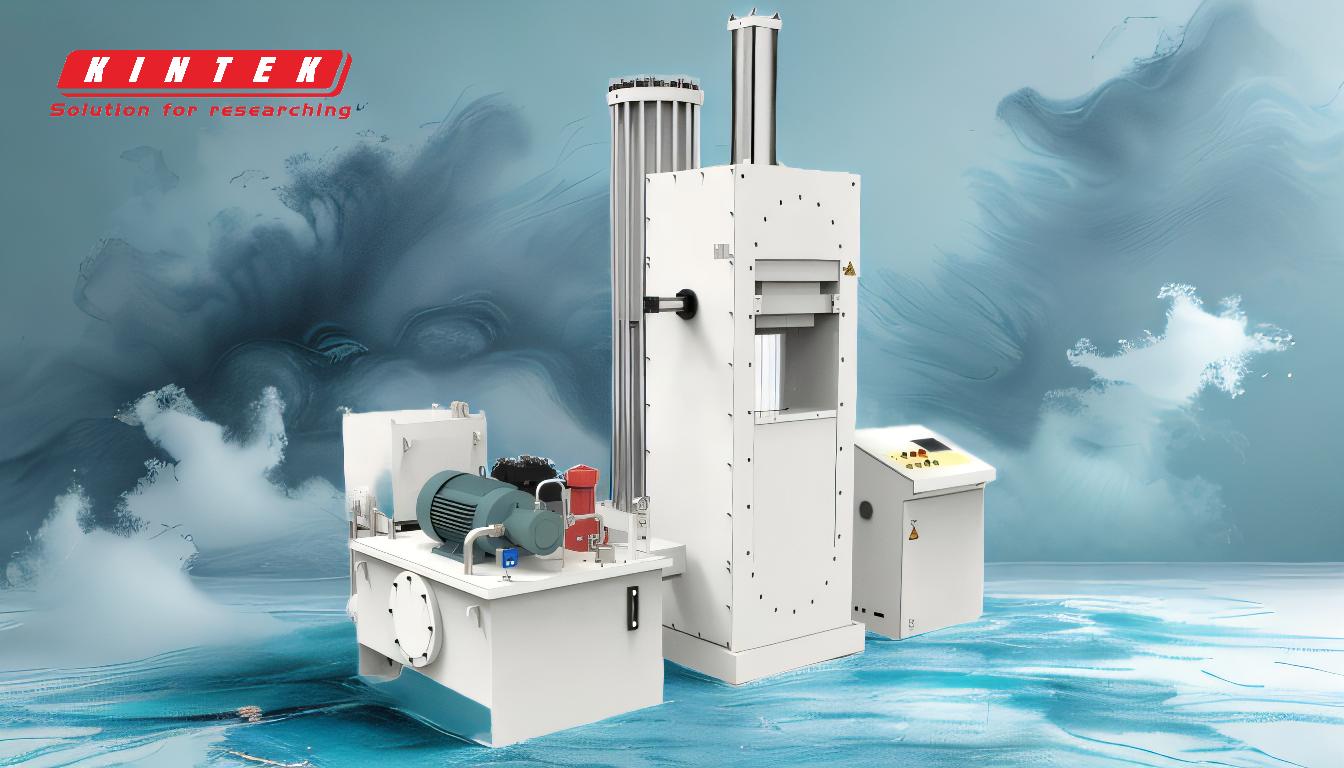
-
Increased Strength and Hardness:
- Cold working alters the metal's grain structure, causing dislocations and increasing its strength and hardness. This is due to the phenomenon known as strain hardening or work hardening, where the metal becomes more resistant to deformation as it is worked.
- This makes cold-worked metals ideal for applications requiring high strength, such as automotive components, aerospace parts, and construction materials.
-
Improved Dimensional Accuracy:
- Since cold working is performed at room temperature, there is minimal thermal expansion or contraction, ensuring tighter tolerances and better dimensional control.
- This precision is crucial for manufacturing parts that require exact specifications, such as gears, fasteners, and medical devices.
-
Enhanced Surface Finish:
- Cold working processes, such as rolling, drawing, or extrusion, produce smoother and more refined surface finishes compared to hot working.
- A superior surface finish not only improves the aesthetic appeal but also enhances the metal's resistance to wear and corrosion.
-
Retention of Ductility and Toughness:
- While cold working increases strength, it also retains a significant level of ductility and toughness, allowing the metal to withstand impact and deformation without fracturing.
- This balance of properties is essential for materials used in dynamic or high-stress environments.
-
Cost-Effectiveness and Energy Efficiency:
- Cold working eliminates the need for heating, reducing energy consumption and operational costs.
- It also minimizes material waste, as the process is highly controlled and precise, leading to cost savings in large-scale production.
-
Versatility in Applications:
- Cold working can be applied to a wide range of metals, including steel, aluminum, copper, and titanium, making it suitable for diverse industries.
- Common cold working techniques include cold rolling, cold drawing, cold forging, and cold extrusion, each tailored to specific product requirements.
-
Environmental Benefits:
- By avoiding high-temperature processes, cold working reduces greenhouse gas emissions and energy usage, contributing to more sustainable manufacturing practices.
In summary, cold working metal offers a combination of improved mechanical properties, precision, and cost efficiency, making it a preferred method for producing high-quality metal components across various industries.
Summary Table:
Benefit | Description |
---|---|
Increased Strength | Alters grain structure, enhancing hardness and resistance to deformation. |
Dimensional Accuracy | Minimal thermal expansion ensures tight tolerances and precise control. |
Enhanced Surface Finish | Produces smoother, more refined surfaces, improving wear and corrosion resistance. |
Ductility & Toughness | Retains flexibility and impact resistance despite increased strength. |
Cost-Effectiveness | Eliminates heating, reducing energy costs and material waste. |
Versatility | Applicable to steel, aluminum, copper, and titanium for diverse industries. |
Environmental Benefits | Reduces greenhouse gas emissions and energy usage, promoting sustainability. |
Learn how cold working can optimize your metal production—contact our experts today!