Resistance furnaces, while highly efficient and versatile, come with several disadvantages that users should consider. These include high power consumption, increased costs related to power distribution and electricity, and challenges with insulation at high temperatures. Additionally, the need for careful material placement and the potential for refractory materials to conduct electricity at elevated temperatures are notable drawbacks. These factors can impact the overall cost and efficiency of using resistance furnaces in various industrial applications.
Key Points Explained:
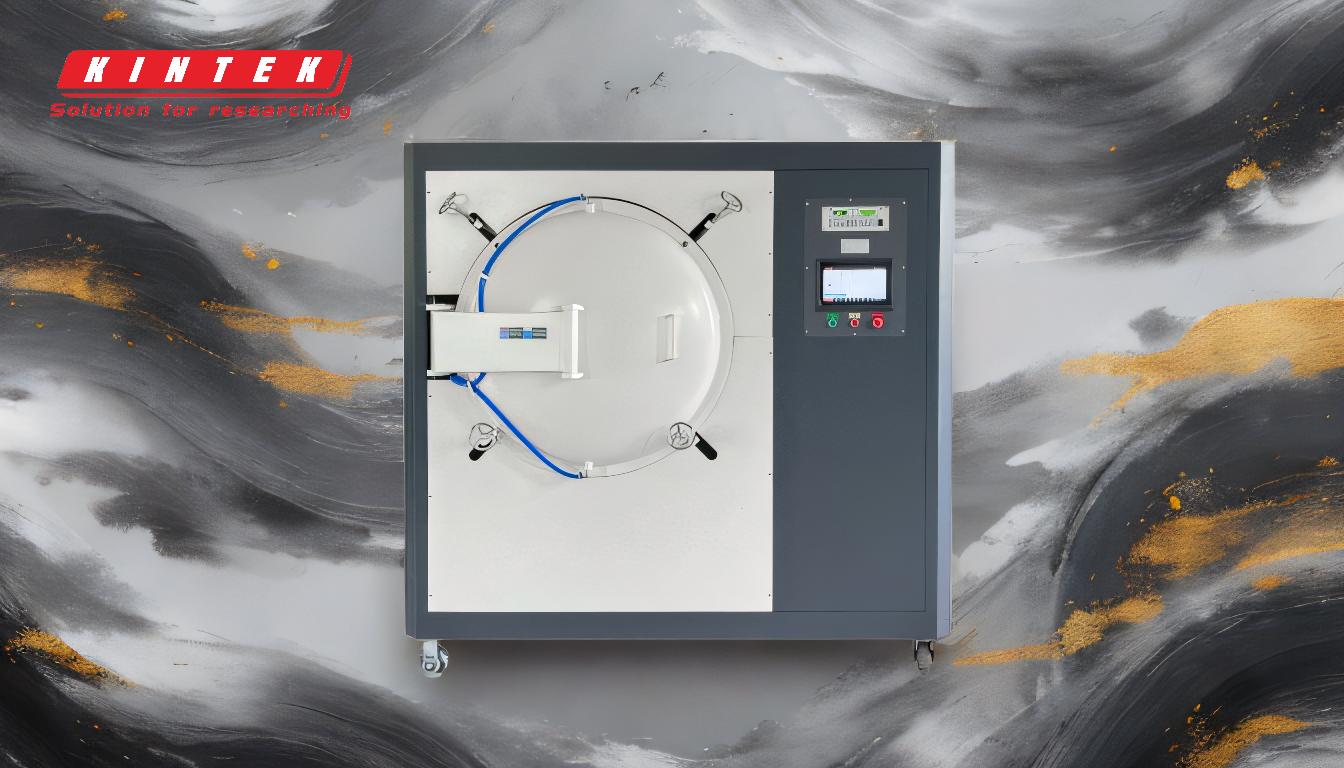
-
High Power Consumption:
- Resistance furnaces are known for their high power consumption. This can lead to increased operational costs, especially in facilities where the furnace is used extensively. The high power demand may also necessitate upgrades to existing power distribution systems, adding to the initial setup costs.
-
Increased Costs:
- Power Distribution Equipment: The need to increase the capacity of power distribution equipment to handle the high power demand of resistance furnaces can significantly increase initial setup costs.
- Electricity Costs: The ongoing cost of electricity can be substantial, particularly in regions where electricity prices are high. This can make resistance furnaces less economical compared to other heating methods over the long term.
-
Insulation Challenges at High Temperatures:
- When the heating temperature exceeds 1000°C, the refractory materials used in resistance furnaces may start to conduct electricity. This necessitates careful attention to insulation to prevent safety hazards and ensure efficient operation. The need for specialized insulation materials can further increase costs.
-
Material Placement and Accessibility:
- Similar to muffle furnaces, resistance furnaces can present challenges in terms of material placement and accessibility. The design of the furnace may make it harder to access the interior, requiring careful placement of materials to ensure even heating and prevent damage.
-
Comparison with Other Furnace Types:
- Muffle Furnaces: While muffle furnaces also have their own set of disadvantages, such as longer warm-up times and accessibility issues, they may be more suitable for certain applications where quick warm-ups are not required.
- Induction Furnaces: Induction furnaces, on the other hand, lack refining capacity and require charge materials to be free of oxides and of known composition. This can limit their use in applications where refining is necessary.
In summary, while resistance furnaces offer high thermal efficiency and good working conditions, their high power consumption, increased costs, and insulation challenges at high temperatures are significant disadvantages that need to be carefully considered. These factors can impact the overall cost and efficiency of using resistance furnaces in various industrial applications.
Summary Table:
Disadvantage | Details |
---|---|
High Power Consumption | Leads to increased operational costs and may require power system upgrades. |
Increased Costs | Higher initial setup and ongoing electricity costs. |
Insulation Challenges | Refractory materials may conduct electricity at temperatures above 1000°C. |
Material Placement | Requires careful placement for even heating and accessibility. |
Comparison with Other Furnaces | Muffle and induction furnaces have different pros and cons. |
Need help choosing the right furnace for your needs? Contact our experts today for personalized advice!