The five basic heat treatment processes for metals are annealing, quenching, tempering, case hardening, and normalizing. These processes are used to alter the physical and mechanical properties of metals, such as hardness, ductility, toughness, and surface strength, to make them suitable for specific applications. Each process involves controlled heating and cooling cycles, which modify the microstructure of the metal to achieve desired properties. Below, we explore these processes in detail, focusing on their purpose, methodology, and outcomes.
Key Points Explained:
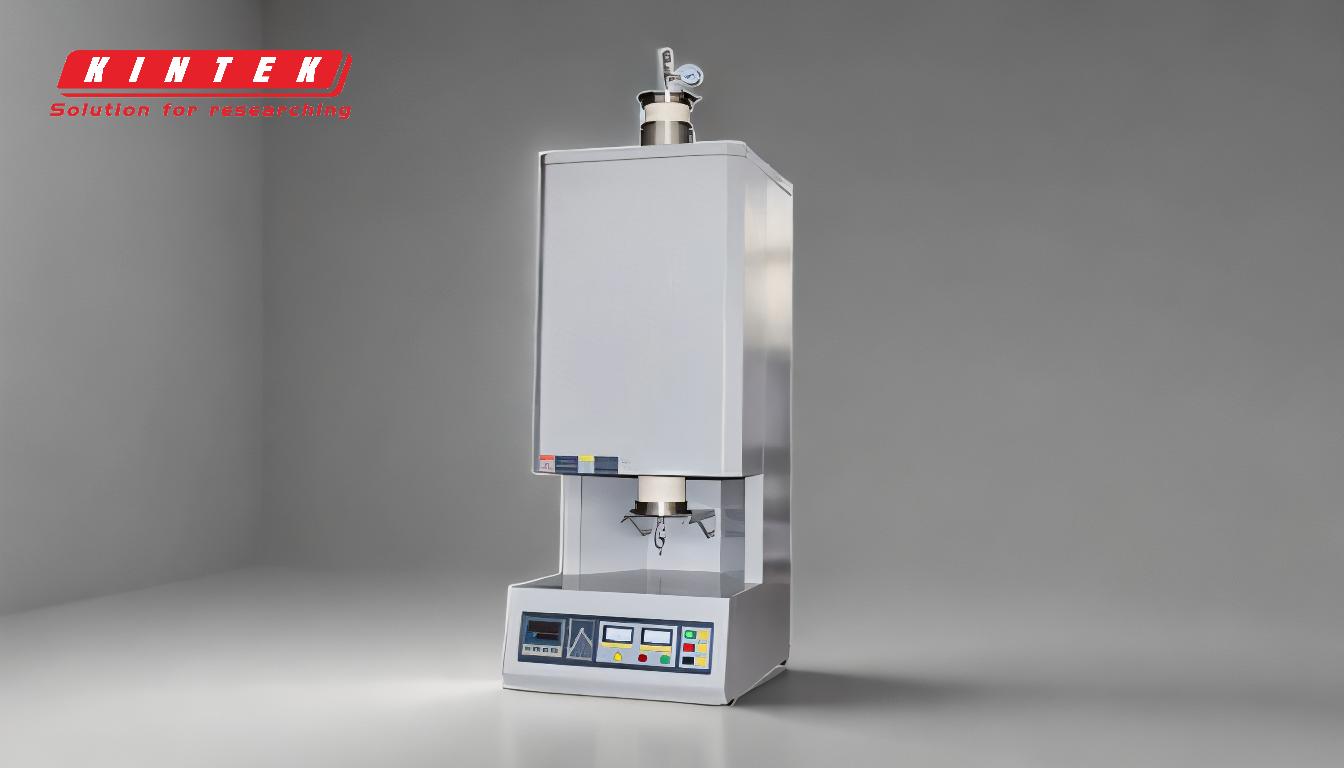
-
Annealing
- Purpose: Annealing is primarily used to soften metals, improve ductility, and reduce internal stresses. It is often performed to make metals easier to machine or form.
- Process: The metal is heated to a specific temperature (above its recrystallization temperature) and held there for a period of time. It is then slowly cooled, usually in the furnace itself, to achieve a refined grain structure.
- Outcome: Increased ductility, reduced hardness, and improved machinability.
-
Quenching
- Purpose: Quenching is used to rapidly cool metals to achieve high hardness and strength. It is commonly applied to steel to form martensite, a hard and brittle microstructure.
- Process: The metal is heated to a high temperature and then rapidly cooled by immersing it in a quenching medium such as water, oil, or air.
- Outcome: Increased hardness and strength, but reduced ductility and toughness.
-
Tempering
- Purpose: Tempering is performed after quenching to reduce brittleness and improve toughness. It balances the hardness achieved through quenching with the need for ductility.
- Process: The quenched metal is reheated to a temperature below its critical point and then cooled at a controlled rate.
- Outcome: Improved toughness and ductility while retaining some hardness.
-
Case Hardening
- Purpose: Case hardening is used to create a hard, wear-resistant surface while maintaining a tough and ductile core. It is ideal for components that require both surface hardness and internal strength, such as gears and shafts.
- Process: The metal is exposed to a carbon-rich environment (carburizing) or nitrogen (nitriding) at high temperatures, followed by quenching. This diffuses carbon or nitrogen into the surface layer.
- Outcome: A hard surface layer with a softer, tougher core.
-
Normalizing
- Purpose: Normalizing is used to refine the grain structure of metals, improve mechanical properties, and reduce internal stresses. It is often performed to prepare metals for further processing.
- Process: The metal is heated to a temperature above its critical range and then cooled in still air. This results in a more uniform and fine-grained microstructure.
- Outcome: Improved mechanical properties, reduced internal stresses, and a more uniform structure.
These five heat treatment processes are fundamental in metallurgy and are chosen based on the desired properties of the metal and its intended application. Understanding their principles and outcomes is essential for selecting the right process for specific manufacturing needs.
Summary Table:
Process | Purpose | Methodology | Outcome |
---|---|---|---|
Annealing | Soften metals, improve ductility, reduce internal stresses | Heat above recrystallization temperature, hold, then slowly cool | Increased ductility, reduced hardness, improved machinability |
Quenching | Achieve high hardness and strength | Heat to high temperature, then rapidly cool in water, oil, or air | Increased hardness and strength, reduced ductility and toughness |
Tempering | Reduce brittleness, improve toughness | Reheat quenched metal below critical point, cool at controlled rate | Improved toughness and ductility, retained hardness |
Case Hardening | Create a hard surface with a tough core | Expose to carbon/nitrogen at high temperatures, then quench | Hard surface layer, softer and tougher core |
Normalizing | Refine grain structure, reduce internal stresses | Heat above critical range, cool in still air | Improved mechanical properties, reduced stresses, uniform structure |
Need help selecting the right heat treatment process for your metals? Contact our experts today!