Liquid phase sintering and reaction sintering are advanced techniques in material processing that offer significant advantages over traditional solid-state sintering. The primary attractive feature of these methods is the formation of a liquid phase, which enhances mass transport and significantly lowers the sintering temperature. This leads to improved densification, better particle rearrangement, and more efficient bonding, making it particularly useful for materials that are difficult to sinter through conventional methods. The liquid phase acts as a binder or flux, facilitating the process and enabling the production of dense, strong materials from powders. These techniques are especially beneficial for materials with high melting points or complex compositions, as they reduce energy consumption and processing time.
Key Points Explained:
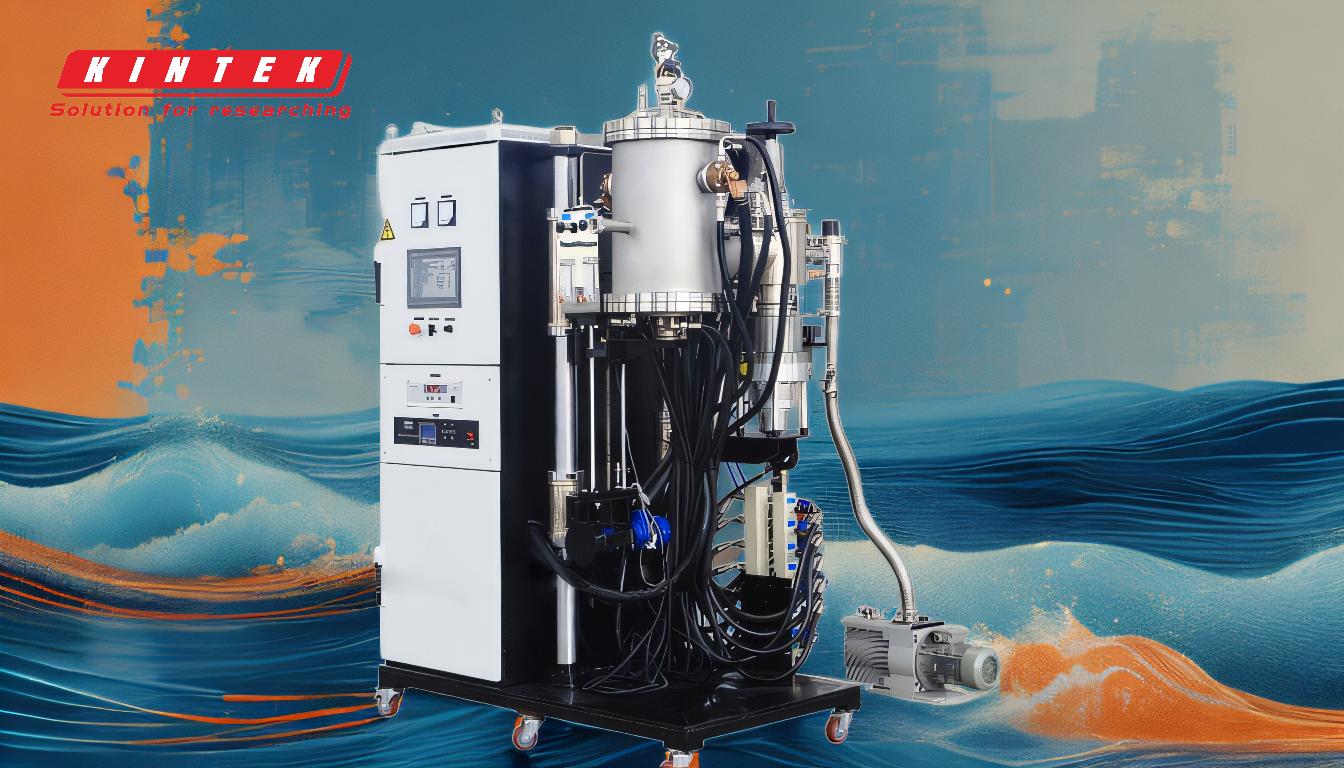
-
Enhanced Mass Transport:
- The formation of a liquid phase during sintering significantly enhances mass transport compared to solid-state diffusion. This is because atoms and molecules move more freely in a liquid, allowing for faster and more efficient rearrangement of particles.
- Enhanced mass transport leads to better densification and stronger bonds between particles, resulting in materials with improved mechanical properties.
-
Lower Sintering Temperature:
- Liquid phase sintering involves adding a trace amount of a sintering aid, which forms a transient liquid phase at the particle contact surfaces. This liquid phase greatly reduces the required sintering temperature.
- Lowering the sintering temperature is particularly advantageous for materials with high melting points, as it reduces energy consumption and makes the process more cost-effective.
-
Improved Densification:
- The liquid phase acts as a binder or flux, filling pores and facilitating the rearrangement of grains into a more favorable packing arrangement. This leads to higher densification and fewer defects in the final product.
- Improved densification is crucial for producing materials with high strength and durability, which are essential for various industrial applications.
-
Versatility in Material Processing:
- Liquid phase sintering is particularly useful for materials that are difficult to sinter through traditional methods, such as those with high melting points or complex compositions.
- This versatility allows for the processing of a wide range of materials, including ceramics, metals, and composites, making it a valuable technique in material manufacturing.
-
Reduced Processing Time and Cost:
- The enhanced mass transport and lower sintering temperature result in a shorter sintering time, which reduces overall processing time and cost.
- Additionally, the simplicity and low cost of the equipment required for liquid phase sintering make it an attractive option for industrial applications.
-
Non-Equilibrium Sintering:
- Liquid phase sintering enables non-equilibrium sintering, which allows for the production of materials with unique microstructures and properties that are not achievable through traditional methods.
- This capability opens up new possibilities for material design and innovation, leading to the development of advanced materials with tailored properties.
In summary, the attractive features of liquid phase sintering and reaction sintering lie in their ability to enhance mass transport, lower sintering temperatures, improve densification, and offer versatility in material processing. These advantages make them highly effective techniques for producing dense, strong materials from powders, particularly for those that are difficult to sinter through conventional methods.
Summary Table:
Feature | Description |
---|---|
Enhanced Mass Transport | Liquid phase improves particle movement, leading to better densification. |
Lower Sintering Temperature | Reduces energy consumption and costs, ideal for high-melting-point materials. |
Improved Densification | Liquid phase fills pores, creating stronger, defect-free materials. |
Versatility | Suitable for ceramics, metals, and composites with complex compositions. |
Reduced Time & Cost | Faster processing and lower equipment costs make it cost-effective. |
Non-Equilibrium Sintering | Enables unique microstructures and tailored material properties. |
Explore how liquid phase sintering can transform your material processing—contact us today!