The HIP (Hot Isostatic Pressing) process of casting is a technique used to enhance the density and mechanical properties of materials, particularly metals and ceramics. By applying high temperature and pressure, HIP reduces porosity and improves the material's strength, durability, and resistance to fractures. The process involves loading the material into a flexible mold, sealing it, and subjecting it to high-pressure argon gas in a specialized vessel. After a specific duration, the vessel is cooled, and the treated material is removed. This method not only strengthens the final product but also minimizes scrap material, making it a valuable process in manufacturing.
Key Points Explained:
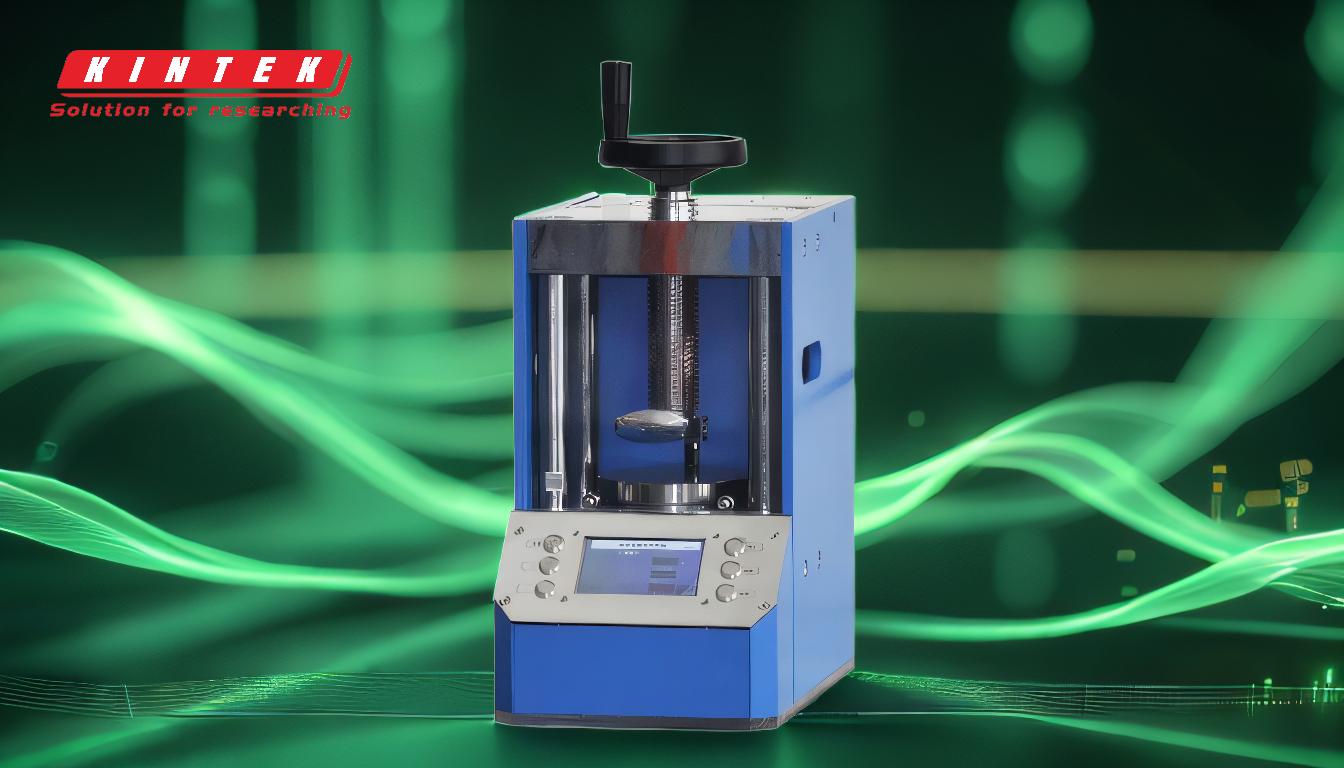
-
Purpose of HIP in Casting:
- The primary goal of the HIP process in casting is to increase the density of components, whether they are obtained from casting or metal powders. By reducing porosity, HIP enhances the mechanical properties of the material, such as resistance to fractures, fatigue, and traction. This makes the final product stronger and more durable.
-
Process Overview:
- The HIP process involves several key steps:
- Loading the Material: The material, often in powder form, is loaded into a flexible mold.
- Sealing the Mold: The mold is sealed to ensure that the material is contained during the pressing process.
- Applying Pressure and Heat: The sealed mold is placed in a pressure vessel where high-pressure argon gas is introduced. This gas increases both the temperature and pressure within the vessel, creating the necessary conditions for the material to undergo physical changes.
- Cooling and Removal: After a specific duration, the vessel is cooled, and the treated material is removed from the mold.
- The HIP process involves several key steps:
-
Role of Argon Gas:
- Argon gas plays a crucial role in the HIP process. It is forced into the HIP machine to increase the temperature and pressure within the vessel. This inert gas helps create the necessary conditions for the material to undergo changes in its physical properties, such as increased density and reduced porosity.
-
Benefits of HIP:
- Enhanced Strength and Durability: By reducing porosity and improving density, HIP creates stronger and more durable products.
- Minimized Scrap Material: The process helps minimize scrap material production by treating materials with heat and pressure before they are used in other manufacturing processes.
- Conversion of Metal Powders: HIP can convert metal powders into solid materials under high pressure, making it a versatile process in material manufacturing.
-
Applications in Manufacturing:
- The HIP process is widely used in industries that require high-strength and durable materials, such as aerospace, automotive, and medical device manufacturing. It is particularly valuable for components that need to withstand extreme conditions and stresses.
In summary, the HIP process of casting is a sophisticated technique that significantly enhances the properties of materials by reducing porosity and increasing density. Through the application of high temperature and pressure, particularly using argon gas, the process creates stronger, more durable products with minimized scrap material, making it an essential method in modern manufacturing.
Summary Table:
Aspect | Details |
---|---|
Purpose | Increases material density, reduces porosity, enhances strength and durability. |
Key Steps | 1. Load material into a mold. 2. Seal the mold. 3. Apply heat and pressure. 4. Cool and remove. |
Role of Argon Gas | Increases temperature and pressure, enabling material transformation. |
Benefits | - Enhanced strength and durability. - Minimized scrap material. - Converts metal powders into solid materials. |
Applications | Aerospace, automotive, medical device manufacturing. |
Discover how the HIP process can optimize your manufacturing—contact us today!