Heat treatment is a critical process in metallurgy and materials science, used to alter the physical and sometimes chemical properties of metals and alloys. The process involves heating the material to a specific temperature, holding it at that temperature for a predetermined time, and then cooling it in a controlled manner. This sequence of steps can enhance properties such as hardness, strength, ductility, and toughness, or relieve internal stresses. Different heat treatment methods, such as annealing, hardening, tempering, and case hardening, are employed depending on the desired outcome. Vacuum heat treatment, a specialized form, uses a controlled atmosphere to prevent oxidation and achieve superior results. The process is widely used in manufacturing to improve the performance and longevity of metal components.
Key Points Explained:
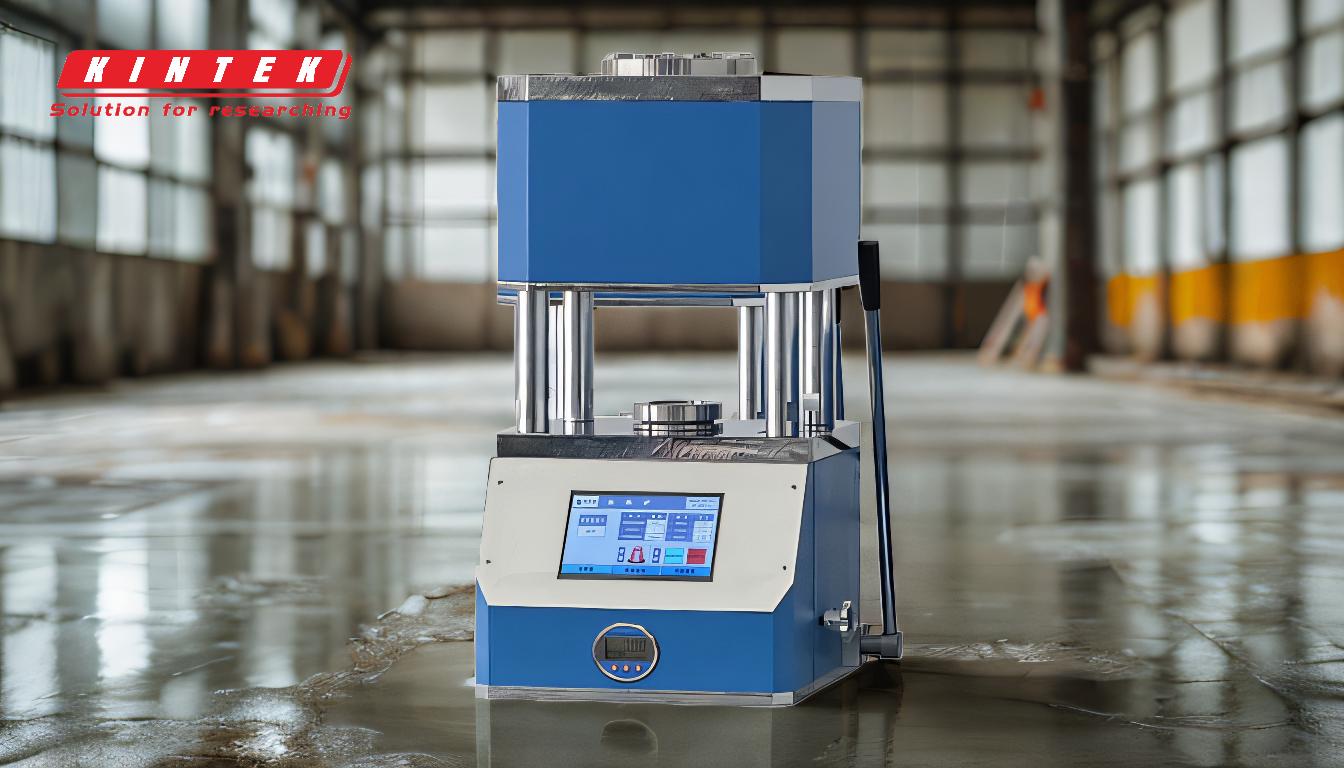
-
Definition and Purpose of Heat Treatment:
- Heat treatment is a process that involves heating and cooling metals or alloys in the solid state to achieve desired properties.
- It is used to modify properties such as hardness, strength, ductility, toughness, and stress relief.
- The process excludes heating solely for hot working purposes.
-
Basic Steps of Heat Treatment:
- Heating: The material is heated to a specific temperature, which can range up to 2,400°F (1,316°C), depending on the material and the desired outcome.
- Holding: The material is held at the target temperature for a specified duration, which can vary from a few seconds to over 60 hours.
- Cooling: The material is cooled according to a prescribed method, which can involve air cooling, oil quenching, or other techniques, depending on the desired properties.
-
Common Heat Treatment Processes:
- Annealing: Softens the metal, improves ductility, and relieves internal stresses. It involves heating the material to a specific temperature and then slowly cooling it.
- Hardening: Increases the hardness and strength of the metal by heating it to a high temperature and then rapidly cooling (quenching) it.
- Tempering: Follows hardening to reduce brittleness and improve toughness. It involves reheating the hardened metal to a lower temperature and then cooling it.
- Case Hardening: Hardens only the surface of the metal while keeping the core soft and tough. Techniques include carburizing, nitriding, and induction hardening.
- Stress Relief: Removes internal stresses caused by machining, welding, or forming, typically by heating the material to a moderate temperature and then slowly cooling it.
-
Specialized Heat Treatment Methods:
- Vacuum Heat Treatment: Conducted in a vacuum environment to prevent oxidation and contamination. The metal is heated to high temperatures in a sealed chamber with air removed by a vacuum pump. This method ensures superior and predictable results.
- Bright Annealing: Minimizes oxidation by using pure hydrogen, nitrogen, or argon atmospheres, resulting in a bright, clean surface finish.
- Brazing: Joins metals using a filler material at high temperatures in a controlled atmosphere, such as pure hydrogen or dissociated ammonia.
-
Applications of Heat Treatment:
- Softening or Hardening Metals: Depending on the process, heat treatment can either soften metals (annealing) or harden them (hardening, case hardening).
- Localized Hardening: Techniques like induction and flame hardening allow for selective hardening of specific areas on a part.
- Stress Relief: Used to remove stresses from materials after machining, forming, or cutting.
- Improving Resilience: Processes like austempering and marquenching add resilience to metals, making them suitable for applications requiring spring-like properties.
- Magnetic Properties: Heat treatment can alter magnetic permeability, as seen in magnetic annealing or mu metal annealing.
-
Importance of Controlled Atmosphere:
- In processes like vacuum heat treatment and bright annealing, the absence of oxygen or the use of inert gases prevents oxidation and contamination, leading to higher quality and more consistent results.
- Controlled atmospheres are crucial for achieving specific material properties and surface finishes.
-
Temperature and Time Control:
- The success of heat treatment depends on precise control of temperature and time. The temperature must be carefully monitored to ensure the material reaches the desired state, and the holding time must be sufficient to achieve uniform heating.
- Cooling rates are equally important, as they determine the final microstructure and properties of the material.
-
Industrial Applications:
- Heat treatment is widely used in industries such as automotive, aerospace, tool manufacturing, and construction to enhance the performance and durability of metal components.
- It is essential for producing parts that can withstand high stress, wear, and corrosion.
By understanding the principles and processes of heat treatment, manufacturers can tailor the properties of metals and alloys to meet specific application requirements, ensuring optimal performance and longevity of components.
Summary Table:
Aspect | Details |
---|---|
Purpose | Alters physical/chemical properties of metals for improved performance. |
Key Steps | Heating, holding at temperature, controlled cooling. |
Common Processes | Annealing, hardening, tempering, case hardening, stress relief. |
Specialized Methods | Vacuum heat treatment, bright annealing, brazing. |
Applications | Automotive, aerospace, tool manufacturing, construction. |
Benefits | Enhanced hardness, strength, ductility, and stress relief. |
Optimize your metal components with advanced heat treatment—contact our experts today!