Heat treatment involves controlled heating and cooling processes to alter the physical and mechanical properties of materials. The time and temperature of heat treatment are critical factors that determine the outcome, such as hardness, strength, and durability. The specific time and temperature depend on the material type, desired properties, and the heat treatment method used. For instance, sintering temperatures for materials like PTFE typically range between 300-400°C, with sintering times varying from 2 to 6 hours. Additionally, factors like room temperature and the heating environment (e.g., vacuum or controlled atmosphere) can influence the effectiveness of the heat treatment process.
Key Points Explained:
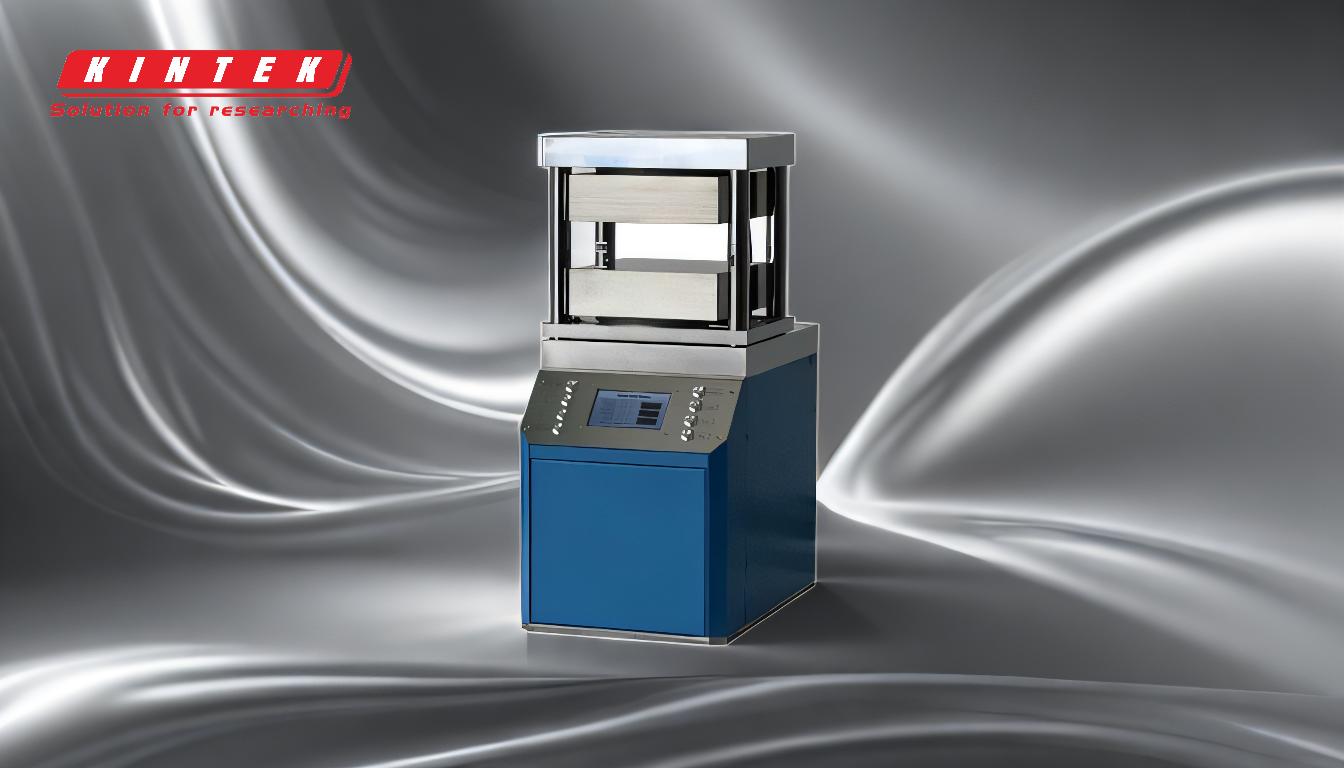
-
Heat Treatment Basics:
- Heat treatment involves heating materials to specific temperatures and holding them for a set time before cooling. This process alters the material's microstructure, improving properties like hardness, strength, and durability.
- The time and temperature are tailored to the material and desired outcome. For example, sintering PTFE requires temperatures between 300-400°C and durations of 2-6 hours.
-
Material-Specific Requirements:
- Different materials have unique heat treatment requirements. For instance, metals may require higher temperatures and shorter times compared to polymers like PTFE.
- The sintering temperature and time for PTFE depend on the powder properties and the desired final characteristics.
-
Influence of External Factors:
- Room temperature can affect heat treatment processes. For example, sintering ovens perform better in environments above 50°C, as lower temperatures may hinder proper heating.
- The heating environment, such as vacuum heat treatment, minimizes thermal stress and deformation, resulting in higher-quality products.
-
Process Control and Precision:
- Precise control over heating depth and temperature is crucial. Techniques like high-frequency heating allow for targeted surface heating, reducing the risk of internal thermal stress.
- The choice of equipment, such as vacuum pumps, is influenced by the heating bath temperature and the need to manage vapor pressures effectively.
-
Multi-Step Processes:
- Some heat treatment methods, like Physical Vapor Deposition (PVD), involve multiple steps, including vaporization, transportation, reaction, and deposition. Each step requires specific temperature and time controls to ensure proper coating formation.
- For example, during PVD, metal atoms react with gases at high temperatures to form coatings like oxides or nitrides, which are then deposited onto substrates.
-
Optimization for Quality:
- Slow heating in vacuum heat treatment minimizes internal temperature differences and thermal stress, leading to reduced deformation and improved product quality.
- Proper optimization of time and temperature ensures consistent and reliable results, meeting the desired material properties.
By understanding these key points, equipment and consumable purchasers can make informed decisions about heat treatment processes, ensuring they select the right tools and conditions for their specific applications.
Summary Table:
Factor | Details |
---|---|
Heat Treatment Basics | Heating materials to specific temperatures and holding for set times. |
Material-Specific | Metals: Higher temps, shorter times. Polymers (e.g., PTFE): 300-400°C, 2-6h. |
External Influences | Room temp, heating environment (e.g., vacuum) impact effectiveness. |
Process Control | Precise heating depth and temp control reduce thermal stress. |
Multi-Step Processes | PVD: Vaporization, reaction, deposition at controlled temps and times. |
Optimization | Slow heating minimizes deformation, improves quality. |
Need help optimizing your heat treatment process? Contact our experts today for tailored solutions!