The working frequency of an induction furnace varies significantly depending on the application, material being melted, furnace capacity, and desired melting speed. It typically ranges from utility frequency (50 or 60 Hz) to 400 kHz or higher. Higher frequencies are used for smaller volumes of melts due to the skin depth effect, which ensures shallow penetration of alternating current, while lower frequencies are suitable for larger volumes and can induce stirring or turbulence in the metal. The choice of frequency is critical for achieving efficient heating, uniform temperature distribution, and optimal melting performance.
Key Points Explained:
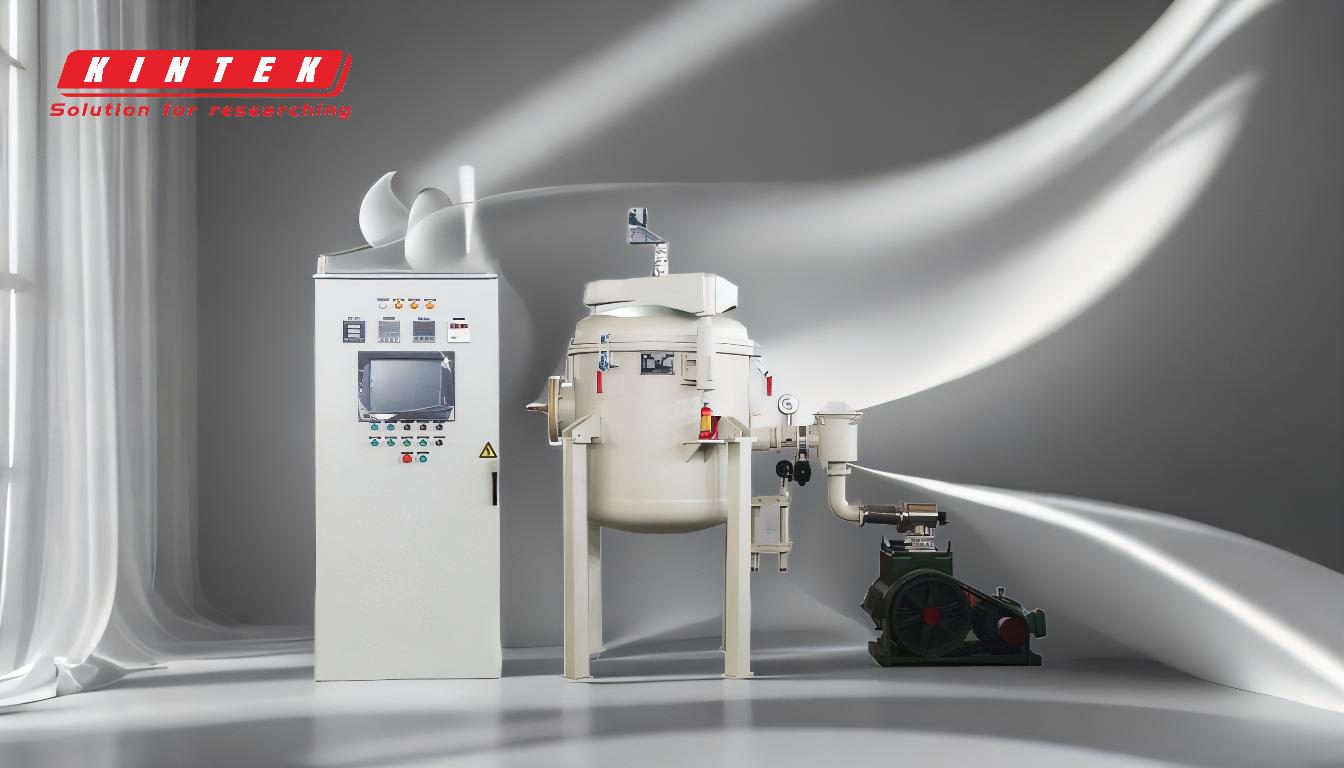
-
Frequency Range of Induction Furnaces:
- Induction furnaces operate across a wide frequency range, from 50 or 60 Hz (utility frequency) to 400 kHz or higher.
- The specific frequency chosen depends on factors such as the material being melted, furnace capacity, and required melting speed.
-
Role of Frequency in Melting:
- Higher Frequencies: Used for smaller volumes of melts. Higher frequencies result in shallower penetration of alternating current (skin depth effect), which is ideal for precise and efficient heating of small quantities.
- Lower Frequencies: Suitable for larger volumes. Lower frequencies can generate stirring or turbulence in the metal, ensuring uniform composition and temperature distribution.
-
Skin Depth Effect:
- The skin depth effect refers to how deeply an alternating current can penetrate a conductor.
- Higher frequencies lead to shallower penetration, making them ideal for smaller melts and applications requiring precise heating.
- Lower frequencies allow deeper penetration, which is beneficial for larger melts and processes that require stirring or turbulence.
-
Factors Influencing Frequency Selection:
- Material Being Melted: Different materials have varying electrical and thermal properties, influencing the choice of frequency.
- Furnace Capacity: Smaller furnaces typically use higher frequencies, while larger furnaces operate at lower frequencies.
- Melting Speed: Higher frequencies enable faster heating and melting, which is advantageous for small-scale or high-speed operations.
-
Applications of Different Frequencies:
- Utility Frequency (50 or 60 Hz): Commonly used for large-scale industrial melting processes, such as steel or iron production.
- Medium Frequencies (1-10 kHz): Ideal for medium-sized furnaces and applications requiring a balance between penetration depth and heating efficiency.
- High Frequencies (10-400 kHz or higher): Used for small-scale melting, precision heating, and applications requiring rapid temperature changes.
-
Advantages of Variable Frequency Operation:
- Flexibility: The power supply of an induction furnace can be adjusted to work at different frequencies, allowing it to handle various materials and melt sizes.
- Efficiency: Proper frequency selection ensures optimal energy use, reducing power consumption and operational costs.
- Uniform Heating: The ability to control frequency helps achieve uniform temperature distribution and composition in the melted material.
-
Technical Considerations:
- Power Supply: Induction furnaces use solid-state IGBT frequency conversion and power regulation systems, enabling smooth and stable operation across a wide frequency range.
- Protection Systems: Comprehensive protection functions, such as overcurrent, overvoltage, and overheating protection, ensure safe and reliable operation at all frequencies.
- Control Systems: Advanced control systems allow for automatic frequency scanning and adjustment, ensuring optimal performance for different applications.
-
Practical Implications for Purchasers:
- Material-Specific Requirements: When selecting an induction furnace, consider the materials you intend to melt and their specific frequency requirements.
- Furnace Capacity: Choose a furnace with a frequency range that matches your production needs, whether for small-scale precision work or large-scale industrial melting.
- Energy Efficiency: Opt for a furnace with adjustable frequency and power regulation to maximize energy efficiency and reduce operational costs.
- Maintenance and Operation: Ensure the furnace has user-friendly controls and comprehensive protection systems for easy maintenance and reliable operation.
By understanding the relationship between frequency, material properties, and furnace capacity, purchasers can make informed decisions to select the most suitable induction furnace for their specific needs.
Summary Table:
Frequency Range | Applications | Key Benefits |
---|---|---|
50-60 Hz | Large-scale industrial melting (steel, iron) | Deep penetration, stirring effect |
1-10 kHz | Medium-sized furnaces | Balanced penetration and efficiency |
10-400 kHz+ | Small-scale, precision heating | Shallow penetration, rapid heating |
Need help selecting the right induction furnace frequency for your application? Contact our experts today for personalized guidance!