Heat treatment and mechanical processes significantly influence the material properties of metals, particularly metallic alloys, by altering their microstructure. Heat treatment manipulates properties such as hardness, strength, toughness, ductility, and elasticity through controlled heating and cooling rates, which affect diffusion and phase transformations within the material. Mechanical processes, such as forging or rolling, also modify these properties by inducing plastic deformation, refining grain structure, and redistributing internal stresses. Together, these processes enable tailored material performance for specific applications.
Key Points Explained:
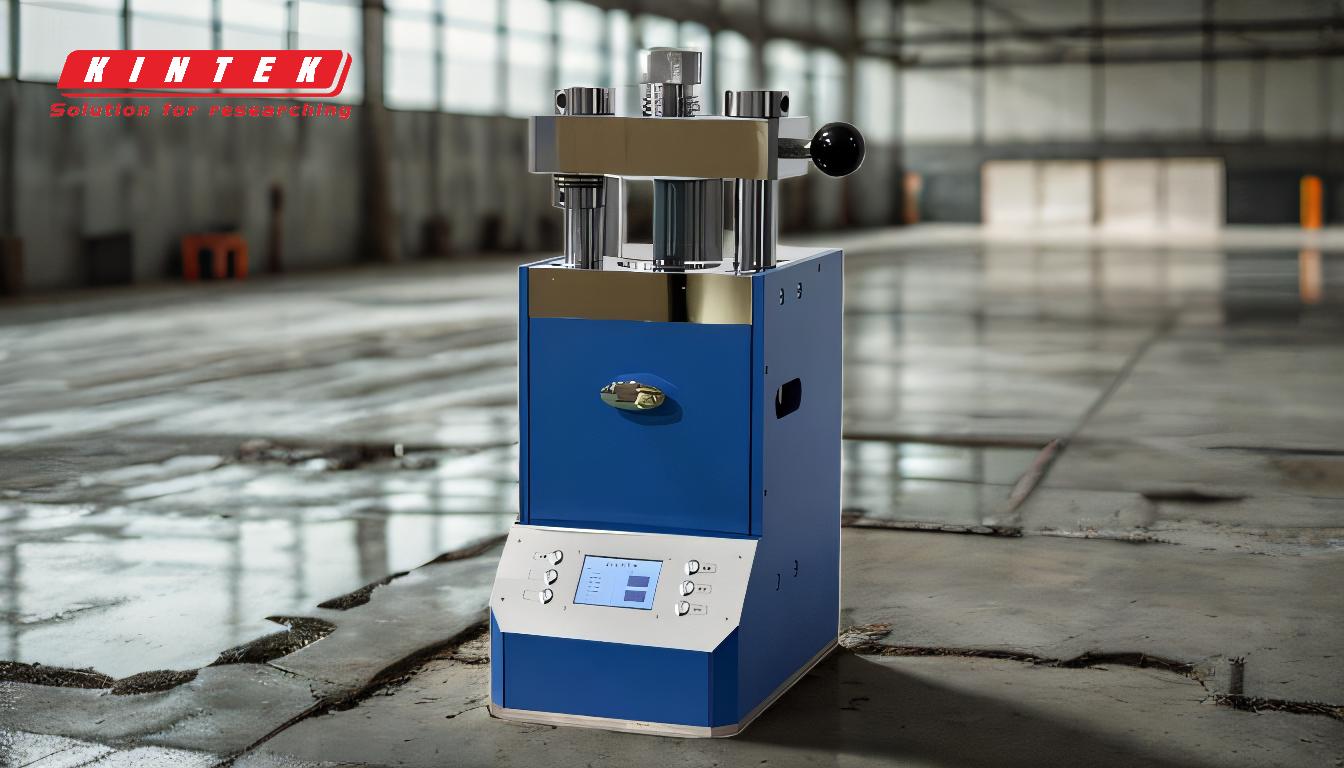
-
Heat Treatment and Its Impact on Material Properties:
- Hardness and Strength: Heat treatment increases hardness and strength by forming harder phases like martensite in steels through rapid cooling (quenching). This process locks atoms into a strained structure, enhancing resistance to deformation.
- Toughness and Ductility: Processes like annealing or tempering reduce brittleness by allowing controlled diffusion and grain growth, improving toughness and ductility. These treatments relieve internal stresses and refine the microstructure.
- Elasticity: Heat treatment can optimize elasticity by balancing hardness and ductility, ensuring the material can return to its original shape after deformation.
-
Mechanical Processes and Their Effects:
- Grain Refinement: Mechanical processes like rolling or forging refine the grain structure, enhancing strength and toughness. Smaller grains impede dislocation movement, increasing resistance to deformation.
- Work Hardening: Plastic deformation during mechanical processing increases dislocation density, leading to work hardening. This improves hardness and strength but may reduce ductility.
- Residual Stress Management: Mechanical processes can introduce residual stresses, which can be beneficial (e.g., compressive surface stresses improving fatigue resistance) or detrimental (e.g., cracking under tensile stresses).
-
Interplay Between Heat Treatment and Mechanical Processes:
- Synergistic Effects: Combining heat treatment with mechanical processes (e.g., thermomechanical treatment) can optimize properties. For example, controlled rolling followed by quenching can produce ultra-high-strength steels.
- Microstructural Control: Both processes influence microstructure, with heat treatment altering phase composition and mechanical processes refining grain size and orientation.
-
Practical Applications:
- Aerospace and Automotive Industries: Heat-treated and mechanically processed alloys are used in critical components like engine parts, landing gear, and chassis, where high strength-to-weight ratios are essential.
- Tooling and Machinery: Tools and dies benefit from enhanced hardness and wear resistance achieved through heat treatment and mechanical processing.
- Construction: Structural steels are often heat-treated and mechanically processed to ensure durability and safety under load.
By understanding the effects of heat treatment and mechanical processes, material engineers can tailor properties to meet specific performance requirements, ensuring reliability and efficiency in various applications.
Summary Table:
Process | Key Effects | Applications |
---|---|---|
Heat Treatment | Increases hardness, strength, toughness, ductility, and elasticity. | Aerospace, automotive, tooling, and construction industries. |
Mechanical Processes | Refines grain structure, induces work hardening, and manages residual stresses. | High-strength components, machinery, and structural materials. |
Combined Effects | Optimizes properties through synergistic microstructural control. | Ultra-high-strength steels and tailored performance materials. |
Optimize your material properties with expert heat treatment and mechanical processing solutions—contact us today!