Resistive heating elements work by converting electrical energy into heat through a process known as Joule heating. When an electric current passes through the heating element, the material's resistance to the flow of electrons causes collisions between electrons and atoms, transferring kinetic energy as heat. The efficiency and effectiveness of this process depend on the material's resistivity, cross-sectional area, and length. Materials used in resistive heating elements are carefully chosen to balance resistance and durability, ensuring they generate sufficient heat without degrading quickly. This principle is widely applied in appliances like electric stoves, space heaters, and industrial furnaces.
Key Points Explained:
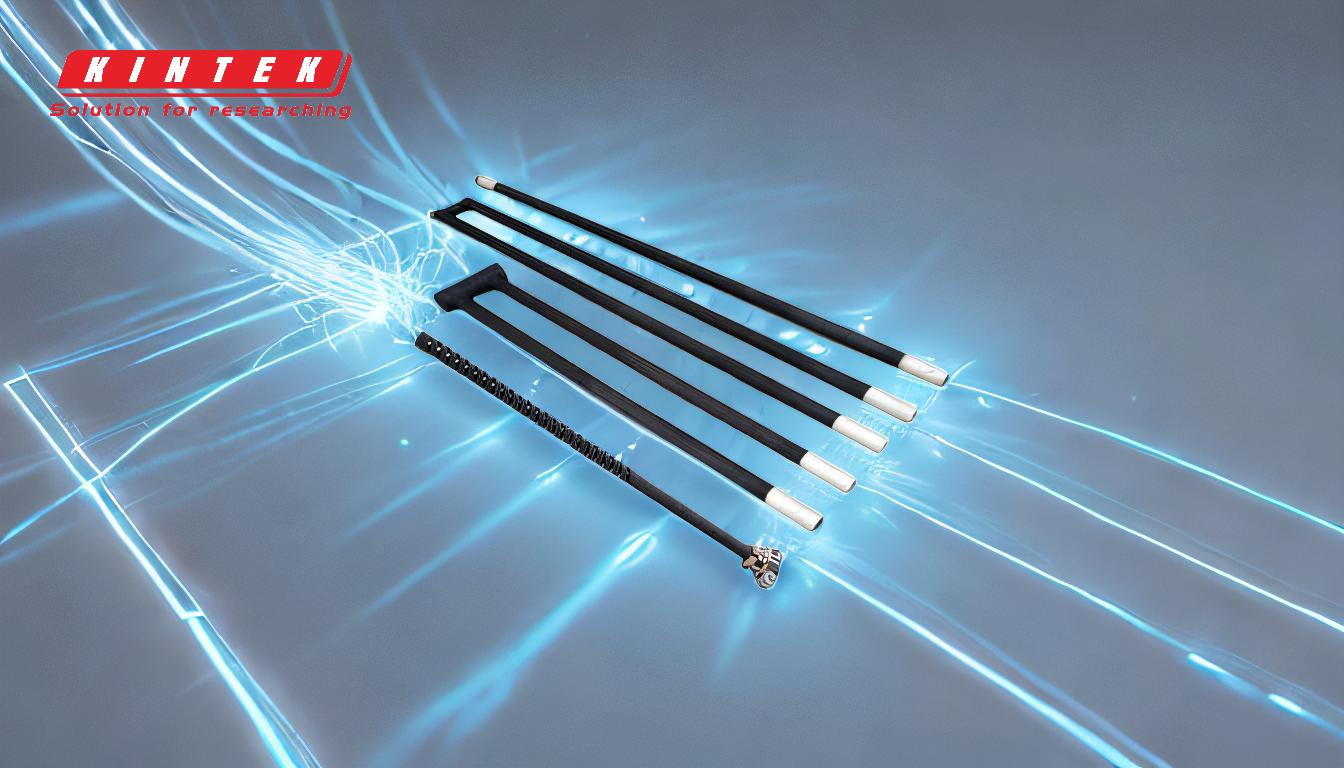
-
Principle of Joule Heating:
- Resistive heating elements operate on the principle of Joule heating, where electrical energy is converted into heat.
- When an electric current flows through the element, the resistance of the material causes electrons to collide with atoms, transferring kinetic energy as heat.
- This process is described by the formula ( P = I^2R ), where ( P ) is the power (heat) generated, ( I ) is the current, and ( R ) is the resistance of the material.
-
Role of Resistance:
- The resistance of the heating element material is crucial for heat generation.
- Materials with too low resistance (conductors) allow current to flow easily without generating significant heat.
- Materials with too high resistance (insulators) block current flow entirely, preventing heat generation.
- The ideal material has a balance of resistance to produce the required heat without excessive energy loss.
-
Material Selection:
- Resistive heating elements are typically made from metallic alloys, ceramic materials, or ceramic metals.
- Common materials include nichrome (an alloy of nickel and chromium), Kanthal (iron-chromium-aluminum alloy), and silicon carbide.
- These materials are chosen for their high resistivity, durability at high temperatures, and resistance to oxidation.
-
Design Considerations:
- The cross-sectional area and length of the heating element influence its resistance and heat output.
- A thinner or longer element will have higher resistance, generating more heat for a given current.
- Engineers design heating elements with specific dimensions and materials to achieve the desired heat output for a particular application.
-
Applications:
- Resistive heating elements are used in a wide range of applications, from household appliances to industrial equipment.
- Examples include electric stoves, toasters, space heaters, water heaters, and industrial furnaces.
- The ability to precisely control heat output makes them suitable for applications requiring consistent and adjustable temperatures.
-
Advantages and Limitations:
-
Advantages:
- Simple and reliable design.
- Efficient conversion of electrical energy to heat.
- Can achieve high temperatures with appropriate materials.
-
Limitations:
- Energy loss due to resistance can reduce efficiency.
- Materials may degrade over time at high temperatures.
- Requires careful material selection and design to balance heat output and durability.
-
Advantages:
-
Comparison with Other Heating Methods:
- Unlike the Peltier effect, which depends on the direction of current flow, Joule heating is independent of current direction.
- Resistive heating is more straightforward and cost-effective for many applications compared to other methods like induction heating or radiant heating.
By understanding these key points, one can appreciate the simplicity and effectiveness of resistive heating elements in converting electrical energy into heat for a wide range of applications.
Summary Table:
Aspect | Details |
---|---|
Principle | Joule heating: Electrical energy converts to heat via resistance. |
Key Formula | ( P = I^2R ): Power (heat) depends on current and resistance. |
Material Selection | Nichrome, Kanthal, silicon carbide: High resistivity, durability, oxidation resistance. |
Design Factors | Cross-sectional area, length: Influence resistance and heat output. |
Applications | Electric stoves, space heaters, industrial furnaces, water heaters. |
Advantages | Simple design, efficient energy conversion, high-temperature capability. |
Limitations | Energy loss, material degradation, requires careful design. |
Need help selecting the right heating element for your application? Contact our experts today!