Induction coils are widely used in various industrial and laboratory applications for heating, melting, and thermal processing of materials. Controlling the temperature of an induction coil is critical to ensure precise and efficient operation. This involves understanding the principles of induction heating, selecting appropriate control mechanisms, and implementing feedback systems to maintain desired temperatures. The process typically includes adjusting the power supply, monitoring coil conditions, and using sensors to regulate temperature dynamically. This answer explores the key methods and technologies used to control the temperature of an induction coil effectively.
Key Points Explained:
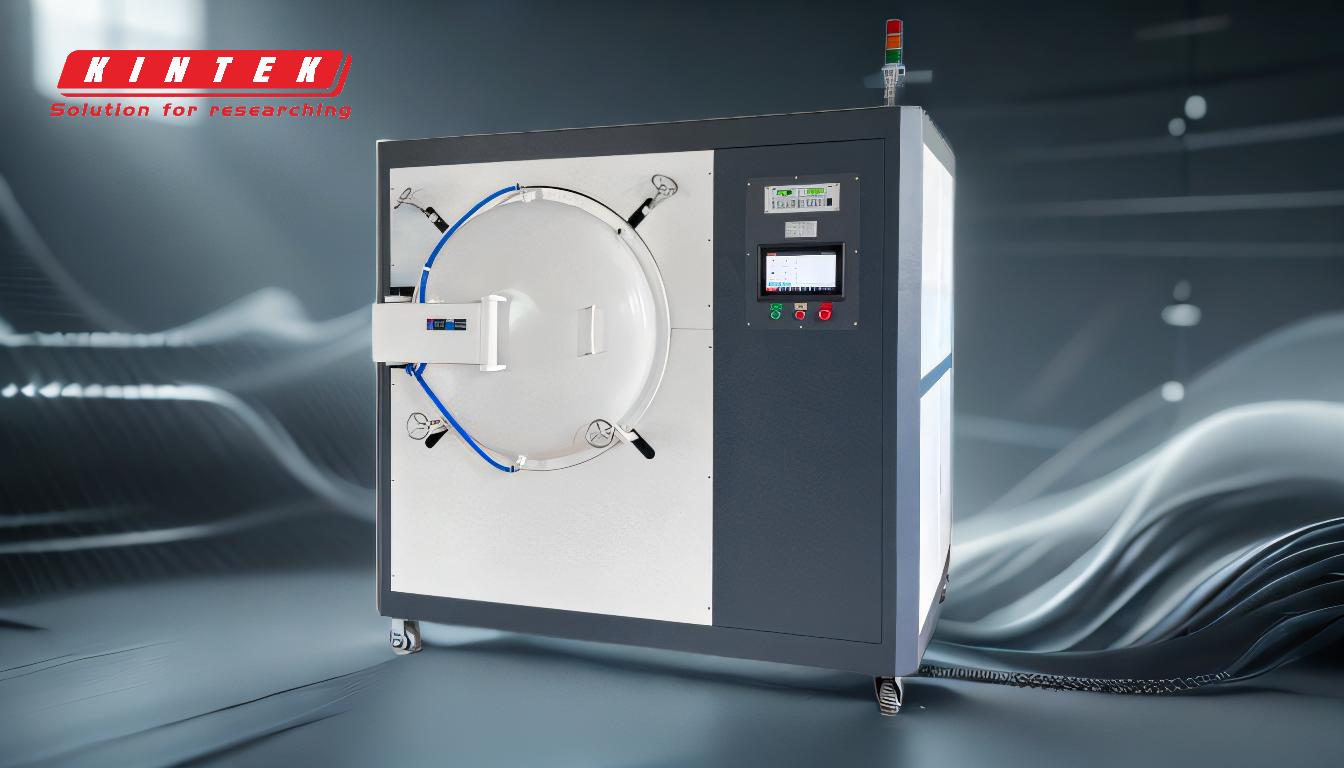
-
Understanding Induction Heating Principles
- Induction heating relies on electromagnetic induction to generate heat within a conductive material. The induction coil creates an alternating magnetic field, which induces eddy currents in the workpiece, causing it to heat up.
- The temperature of the coil itself depends on factors like the frequency of the alternating current, the material of the workpiece, and the power supplied to the coil.
- To control the coil's temperature, it is essential to manage the power input and ensure efficient heat transfer.
-
Power Supply Regulation
- The temperature of the induction coil is directly influenced by the power supplied to it. By adjusting the voltage, current, or frequency of the power supply, the heat generated can be controlled.
- Modern induction heating systems use solid-state inverters and power controllers to precisely regulate the power output. These devices allow for real-time adjustments based on the desired temperature and heating rate.
- Advanced systems may incorporate pulse-width modulation (PWM) or phase-angle control to fine-tune the power delivery.
-
Temperature Monitoring and Feedback Systems
- Accurate temperature control requires real-time monitoring of the coil and workpiece temperatures. This is typically achieved using sensors such as thermocouples, infrared pyrometers, or optical sensors.
- Feedback from these sensors is sent to a control unit, which adjusts the power supply to maintain the target temperature. Closed-loop control systems are commonly used to ensure stability and precision.
- In some cases, multiple sensors are employed to monitor different zones of the workpiece or coil, enabling uniform heating.
-
Cooling Mechanisms for Induction Coils
- Induction coils can overheat if not properly cooled, leading to reduced efficiency and potential damage. Water or air cooling systems are often integrated to dissipate excess heat.
- Cooling channels are built into the coil design, allowing coolant to circulate and maintain a stable temperature. The flow rate and temperature of the coolant can be adjusted to optimize cooling performance.
- Monitoring the coolant temperature and flow rate is essential to prevent overheating and ensure consistent operation.
-
Material and Design Considerations
- The material of the induction coil and workpiece plays a significant role in temperature control. High-conductivity materials like copper are commonly used for coils to minimize energy losses and improve efficiency.
- The design of the coil, including its shape, size, and number of turns, affects the distribution of the magnetic field and heat generation. Optimized designs can enhance temperature uniformity and control.
- Insulation materials may be used to reduce heat loss and improve the efficiency of the heating process.
-
Advanced Control Techniques
- Modern induction heating systems often incorporate programmable logic controllers (PLCs) or computer-based control systems. These allow for automated temperature control, pre-programmed heating cycles, and data logging.
- Machine learning algorithms and predictive modeling are increasingly being used to optimize temperature control, especially in complex or high-precision applications.
- Remote monitoring and control capabilities enable operators to adjust settings and monitor performance from a distance, improving safety and efficiency.
-
Safety and Maintenance Practices
- Regular maintenance of the induction coil and associated equipment is essential to ensure reliable temperature control. This includes inspecting for wear, cleaning cooling systems, and calibrating sensors.
- Safety measures, such as temperature alarms and emergency shutdown systems, should be in place to prevent overheating and protect both equipment and personnel.
- Proper training for operators is crucial to ensure safe and effective operation of the induction heating system.
By combining these methods and technologies, the temperature of an induction coil can be controlled with high precision, ensuring optimal performance and longevity of the equipment.
Summary Table:
Key Aspect | Description |
---|---|
Induction Heating Principles | Electromagnetic induction generates heat; power input and heat transfer are key. |
Power Supply Regulation | Adjust voltage, current, or frequency for precise heat control. |
Temperature Monitoring | Use sensors like thermocouples and feedback systems for real-time adjustments. |
Cooling Mechanisms | Water or air cooling systems prevent overheating and maintain efficiency. |
Material & Design | High-conductivity materials and optimized designs enhance temperature control. |
Advanced Control Techniques | PLCs, machine learning, and remote monitoring improve precision and safety. |
Safety & Maintenance | Regular inspections, cooling system cleaning, and operator training are vital. |
Need help optimizing your induction coil temperature control? Contact our experts today!