Heat treatment is a controlled process that involves heating and cooling metals or alloys to alter their physical and mechanical properties. This process is essential for enhancing characteristics such as hardness, strength, toughness, and resilience, making materials suitable for various industrial applications. The process typically involves three key steps: heating the material to a specific temperature, holding it at that temperature for a predetermined time, and then cooling it according to specific methods. The temperatures and durations vary depending on the desired outcomes, with temperatures potentially reaching up to 2,400°F and holding times ranging from seconds to over 60 hours. Heat treatment can be used for a variety of purposes, including softening or hardening materials, stress relief, and improving magnetic properties.
Key Points Explained:
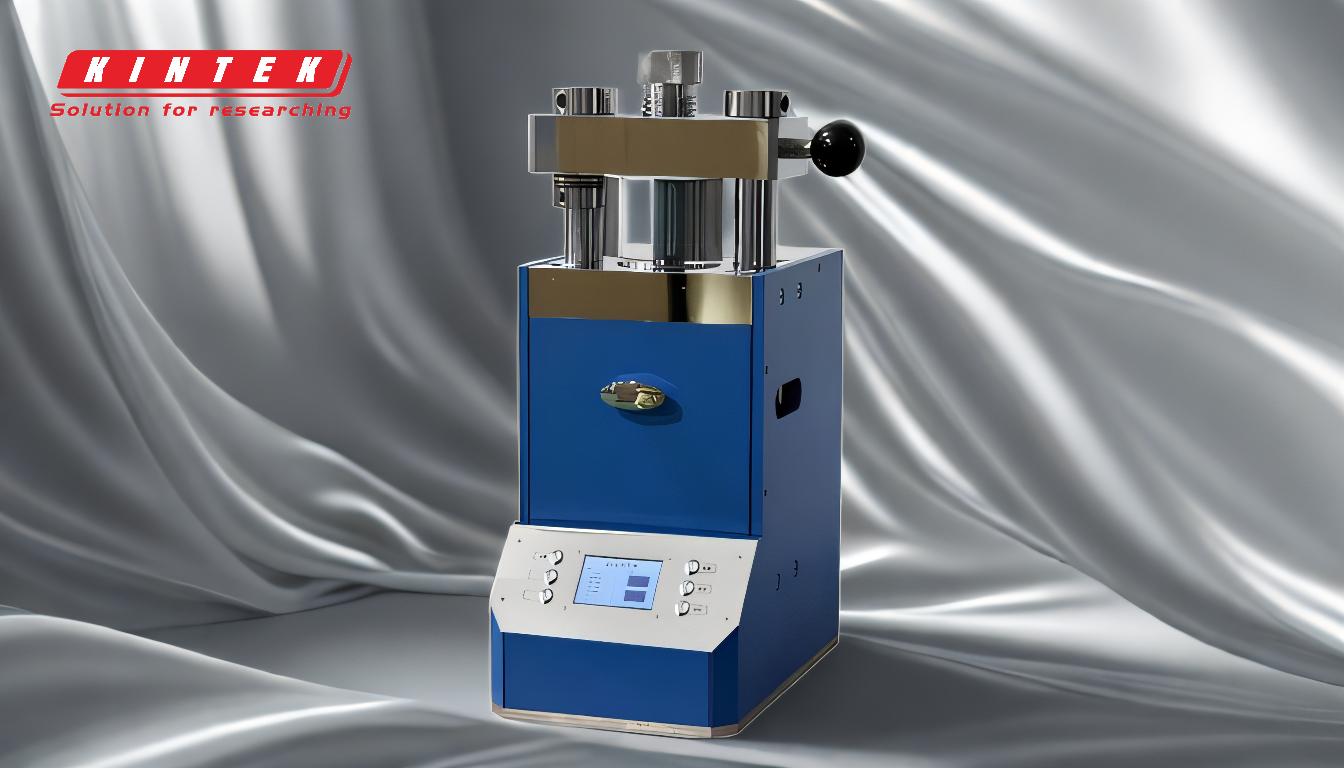
-
Purpose of Heat Treatment:
- Heat treatment is primarily used to alter the physical and mechanical properties of metals and alloys. This includes enhancing hardness, strength, toughness, and other essential characteristics.
- It can also be used to relieve stress in materials, improve resilience, and modify magnetic properties.
-
Basic Steps of Heat Treatment:
- Heating: The material is heated to a specific temperature, which can range up to 2,400°F depending on the material and desired outcome.
- Holding: The material is held at the specified temperature for a predetermined amount of time. This duration can vary from a few seconds to over 60 hours.
- Cooling: The material is cooled according to prescribed methods. The cooling rate is crucial as it affects the final properties of the material.
-
Types of Heat Treatment Processes:
- Annealing: This process involves heating the material to a specific temperature and then allowing it to cool slowly. It is used to soften metals, improve ductility, and relieve internal stresses.
- Hardening: This involves heating the material to a high temperature and then cooling it rapidly (quenching) to increase hardness and strength.
- Tempering: After hardening, tempering is often used to reduce brittleness by reheating the material to a lower temperature and then cooling it.
- Case Hardening: This process hardens the surface of the material while keeping the core soft and tough. Techniques include carburizing and nitriding.
- Stress Relief: This process involves heating the material to a temperature below the critical range to relieve internal stresses without significantly altering the microstructure.
- Austempering and Marquenching: These are specialized processes used to improve the resilience and toughness of materials, particularly steels.
-
Importance of Controlled Heating and Cooling:
- The precise control of heating and cooling rates is crucial in heat treatment. The rate at which a material is heated and cooled can significantly impact its final properties.
- Rapid cooling (quenching) can lead to increased hardness and strength, while slow cooling (as in annealing) can result in softer, more ductile materials.
-
Applications of Heat Treatment:
- Heat treatment is widely used in industries such as automotive, aerospace, construction, and manufacturing. It is essential for producing components that require specific mechanical properties, such as gears, shafts, and cutting tools.
- It is also used in the production of plastic injection molded parts to homogenize the material and relieve internal stresses.
-
Material Considerations:
- Different materials require different heat treatment processes. For example, steels are commonly subjected to hardening and tempering, while aluminum alloys may undergo solution heat treatment and aging.
- The composition and microstructure of the material play a significant role in determining the appropriate heat treatment process.
-
Benefits of Heat Treatment:
- Enhanced Mechanical Properties: Heat treatment can significantly improve the hardness, strength, and toughness of materials.
- Improved Durability: Treated materials are more resistant to wear, fatigue, and deformation.
- Versatility: Heat treatment processes can be tailored to achieve a wide range of properties, making them suitable for various applications.
In summary, heat treatment is a vital process in materials science and engineering, enabling the customization of material properties to meet specific industrial requirements. By carefully controlling the heating and cooling processes, manufacturers can produce materials with enhanced mechanical properties, improved durability, and greater versatility.
Summary Table:
Key Aspect | Details |
---|---|
Purpose | Alters physical and mechanical properties of metals and alloys. |
Key Steps | Heating, holding at temperature, and controlled cooling. |
Common Processes | Annealing, hardening, tempering, case hardening, stress relief. |
Applications | Automotive, aerospace, construction, and manufacturing industries. |
Benefits | Enhanced hardness, strength, toughness, and durability. |
Temperature Range | Up to 2,400°F, with holding times from seconds to over 60 hours. |
Optimize your materials with expert heat treatment solutions—contact us today!