Ashing is a critical process in food science and analytical chemistry used to determine the mineral content and composition of food samples. The two primary methods of ashing are dry ashing and wet ashing, each with specific applications, procedures, and advantages. Dry ashing involves heating the sample in a high-temperature furnace to burn off organic matter, leaving behind inorganic residues (ash) for analysis. Wet ashing, on the other hand, uses chemical digestion with strong acids to break down organic material. Additionally, low-temperature ashing is a specialized method used for sensitive samples. The choice of method depends on the sample type, the required precision, and the specific minerals or elements being analyzed.
Key Points Explained:
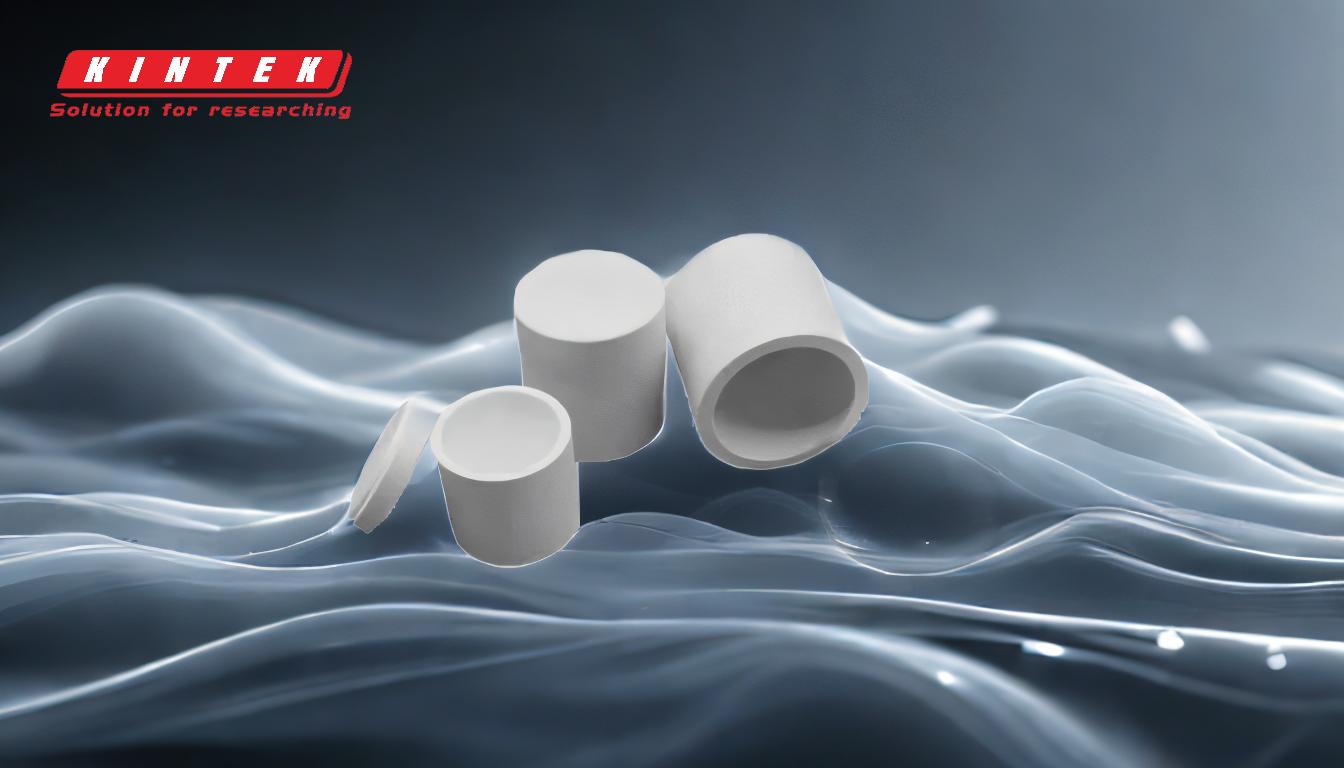
-
Dry Ashing
- Process: Dry ashing involves heating a food sample in a muffle furnace at temperatures around 500-600°C (932-1112°F) in the presence of oxygen. This process burns off organic matter, leaving behind inorganic residues such as oxides, sulfates, phosphates, chlorides, and silicates.
- Applications: It is commonly used to estimate the mineral composition of food samples, as it provides a preliminary step for further elemental analysis. It is particularly useful for samples that can withstand high temperatures.
-
Advantages:
- Simple and cost-effective.
- Suitable for large sample volumes.
- Provides a good approximation of mineral content based on dry-weight ash content.
-
Limitations:
- Not suitable for volatile elements (e.g., selenium, mercury) that may be lost at high temperatures.
- Requires careful temperature control to avoid sample degradation.
-
Wet Ashing
- Process: Wet ashing involves digesting the food sample with strong acids (e.g., nitric acid, sulfuric acid, or perchloric acid) at lower temperatures compared to dry ashing. The acids break down organic matter, leaving behind inorganic residues for analysis.
- Applications: This method is ideal for samples that are sensitive to high temperatures or contain volatile elements that could be lost during dry ashing. It is often used in trace element analysis.
-
Advantages:
- Preserves volatile elements that might be lost in dry ashing.
- Faster than dry ashing for some samples.
- Suitable for a wide range of sample types.
-
Limitations:
- Requires hazardous chemicals and specialized equipment.
- More labor-intensive and time-consuming compared to dry ashing.
- Risk of contamination from reagents.
-
Low-Temperature Ashing
- Process: Low-temperature ashing uses plasma or oxygen radicals at lower temperatures (typically below 200°C) to oxidize organic matter. This method is gentler and avoids the high temperatures used in dry ashing.
- Applications: It is used for heat-sensitive samples or those containing volatile compounds that could be lost at higher temperatures.
-
Advantages:
- Preserves the integrity of heat-sensitive samples.
- Reduces the risk of losing volatile elements.
-
Limitations:
- Requires specialized equipment.
- Slower than traditional dry ashing.
-
Calculation of Ash Content
- The ash content is calculated using the formula: [ \text{Ash content (%)} = \frac{M(\text{ash})}{M(\text{dry})} \times 100 ] where ( M(\text{ash}) ) is the weight of the sample after ashing, and ( M(\text{dry}) ) is the weight of the sample before ashing.
- This calculation provides a quantitative measure of the inorganic mineral content in the sample.
-
Applications of Ashing in Food Science
- Mineral Analysis: Ashing is used to determine the concentration of essential minerals (e.g., calcium, magnesium, potassium) in food products.
- Quality Control: It helps assess the purity and composition of food ingredients.
- Regulatory Compliance: Ashing is often required to meet food safety and labeling regulations.
- Research and Development: It aids in the development of fortified foods and nutritional studies.
-
Factors Influencing Method Selection
- Sample Type: Dry ashing is suitable for stable, non-volatile samples, while wet ashing is better for heat-sensitive or volatile samples.
- Precision Requirements: Wet ashing is preferred for trace element analysis due to its ability to preserve volatile elements.
- Equipment Availability: Dry ashing requires a muffle furnace, while wet ashing requires acid digestion equipment.
- Safety Considerations: Wet ashing involves hazardous chemicals, requiring proper safety protocols.
-
Comparison of Dry and Wet Ashing
- Temperature: Dry ashing uses high temperatures (500-600°C), while wet ashing uses lower temperatures with chemical digestion.
- Time: Dry ashing is slower due to the heating process, while wet ashing can be faster but requires more hands-on time.
- Sample Integrity: Dry ashing may degrade heat-sensitive samples, while wet ashing preserves them better.
- Cost: Dry ashing is generally more cost-effective, while wet ashing involves higher reagent costs.
By understanding these methods, food scientists and analysts can choose the most appropriate ashing technique based on the sample type, analytical requirements, and desired outcomes. Each method has its strengths and limitations, making them suitable for different applications in food analysis and quality control.
Summary Table:
Method | Process | Applications | Advantages | Limitations |
---|---|---|---|---|
Dry Ashing | Heats sample in a muffle furnace (500-600°C) to burn organic matter. | Mineral composition estimation, suitable for high-temperature-resistant samples. | Simple, cost-effective, good for large samples. | Unsuitable for volatile elements, requires precise temperature control. |
Wet Ashing | Uses strong acids to digest organic matter at lower temperatures. | Trace element analysis, ideal for heat-sensitive or volatile samples. | Preserves volatile elements, faster for some samples. | Requires hazardous chemicals, labor-intensive, risk of contamination. |
Low-Temperature Ashing | Uses plasma or oxygen radicals at <200°C to oxidize organic matter. | Heat-sensitive or volatile samples. | Preserves sample integrity, reduces loss of volatile elements. | Requires specialized equipment, slower than dry ashing. |
Need help choosing the right ashing method for your analysis? Contact our experts today for personalized guidance!