Tensile strength, a critical mechanical property of materials, can be enhanced through various methods, including the introduction of alloying elements, heat treatment, and material processing techniques. Alloying, in particular, is a highly effective approach, as it modifies the material's microstructure and chemical composition, leading to improved mechanical properties. For instance, adding carbon to iron creates steel, which has significantly higher tensile strength than pure iron. Similarly, alloying copper with elements like beryllium or phosphorus results in high-strength copper alloys. These modifications can be tailored to meet specific performance requirements, making alloying a versatile and widely used method for increasing tensile strength.
Key Points Explained:
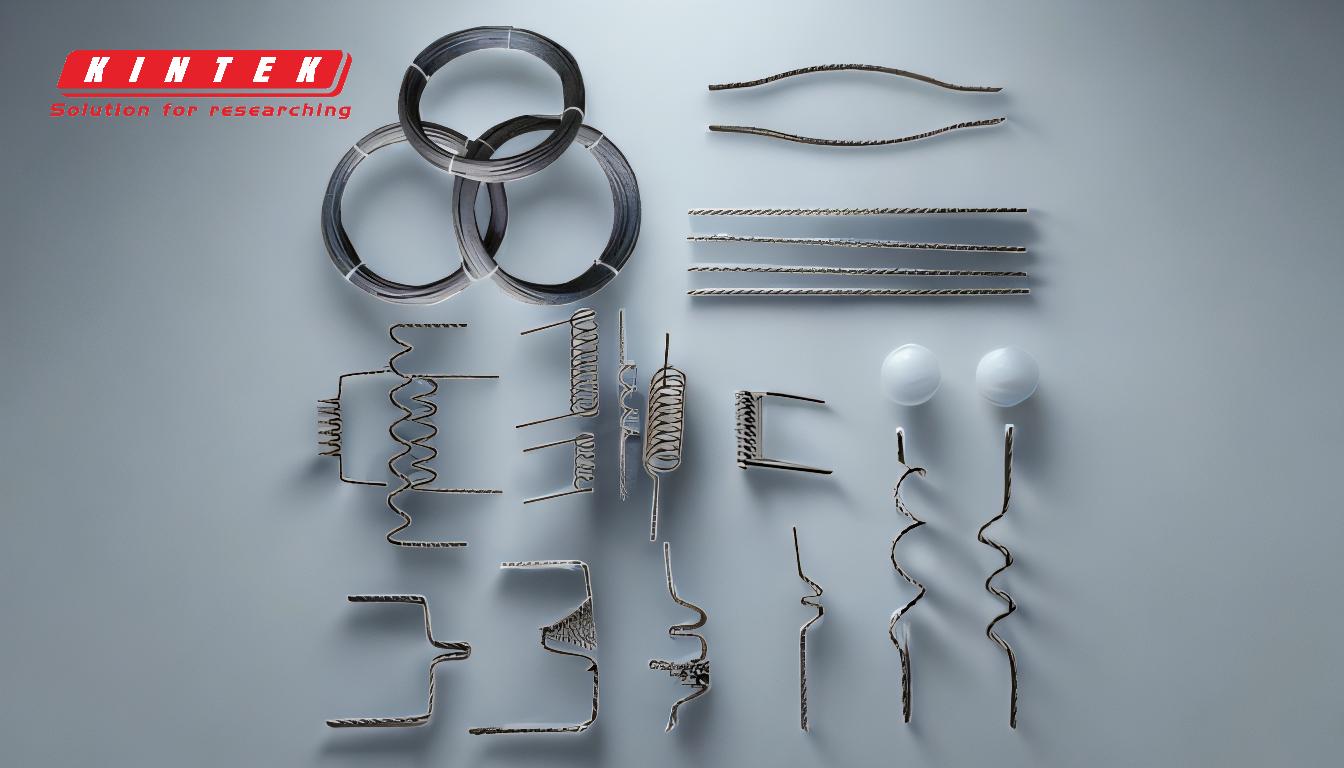
-
Introduction of Alloying Elements:
- Alloying involves adding specific elements to a base metal to enhance its properties.
- Example 1: Adding carbon to iron forms steel, which has a much higher tensile strength than pure iron. The carbon atoms disrupt the iron's crystal lattice, creating a stronger and more rigid structure.
- Example 2: Alloying copper with beryllium or phosphorus creates high-strength copper alloys. These alloys are used in applications requiring both strength and conductivity, such as electrical connectors and springs.
- The choice of alloying elements depends on the desired properties and the base material.
-
Mechanism of Strength Enhancement:
- Alloying elements alter the material's microstructure, often by forming solid solutions or precipitates.
- Solid solutions occur when alloying atoms occupy positions in the base metal's crystal lattice, causing lattice strain. This strain makes dislocation movement (a key factor in deformation) more difficult, thereby increasing strength.
- Precipitates are small particles of a second phase that form within the material. These particles act as obstacles to dislocation motion, further enhancing strength.
-
Heat Treatment:
- Heat treatment processes, such as quenching and tempering, can significantly increase tensile strength.
- Quenching: Rapidly cooling a material from a high temperature can create a hardened structure, such as martensite in steel, which is very strong but brittle.
- Tempering: Reheating the quenched material to a lower temperature reduces brittleness while maintaining high strength. This process balances strength and toughness.
-
Material Processing Techniques:
- Techniques like cold working (e.g., rolling, drawing) increase tensile strength by introducing dislocations and grain refinement.
- Cold working deforms the material at room temperature, increasing dislocation density and creating a finer grain structure. Both effects contribute to higher strength.
- However, excessive cold working can reduce ductility, so a balance must be struck between strength and formability.
-
Importance of Tensile Strength in Applications:
- High tensile strength is crucial in industries such as construction, automotive, aerospace, and electronics.
- In construction, high-strength materials like steel and reinforced concrete are used to build durable structures.
- In automotive and aerospace, lightweight yet strong materials, such as aluminum and titanium alloys, improve fuel efficiency and performance.
- In electronics, high-strength copper alloys ensure reliable performance in connectors and other components.
By understanding and applying these principles, material scientists and engineers can design and produce materials with tailored tensile strength to meet specific application requirements.
Summary Table:
Method | Key Mechanism | Examples |
---|---|---|
Alloying Elements | Modifies microstructure and chemical composition, creating solid solutions or precipitates. | Steel (carbon + iron), high-strength copper alloys (beryllium or phosphorus) |
Heat Treatment | Processes like quenching and tempering increase strength while balancing toughness. | Quenching steel to form martensite, tempering to reduce brittleness |
Material Processing | Cold working introduces dislocations and grain refinement, enhancing strength. | Rolling, drawing, and other cold-working techniques |
Need materials with enhanced tensile strength? Contact our experts today for tailored solutions!