RF sputtering is a thin-film deposition technique that operates under specific pressure conditions to ensure efficient ionization of the gas and effective sputtering of the target material. The chamber pressure typically ranges between 0.5 to 10 mTorr, which is a critical parameter for controlling the energy distribution and motion of sputtered ions. This pressure range allows for a balance between high-energy ballistic impacts and low-energy thermalized motion, depending on the desired deposition characteristics. RF sputtering is particularly suited for dielectric materials and involves alternating cycles of positive and negative bias to prevent ion buildup on insulating targets. The process is driven by an RF power source operating at 13.56 MHz, with a peak-to-peak voltage of 1000 V, ensuring consistent ionization and deposition rates.
Key Points Explained:
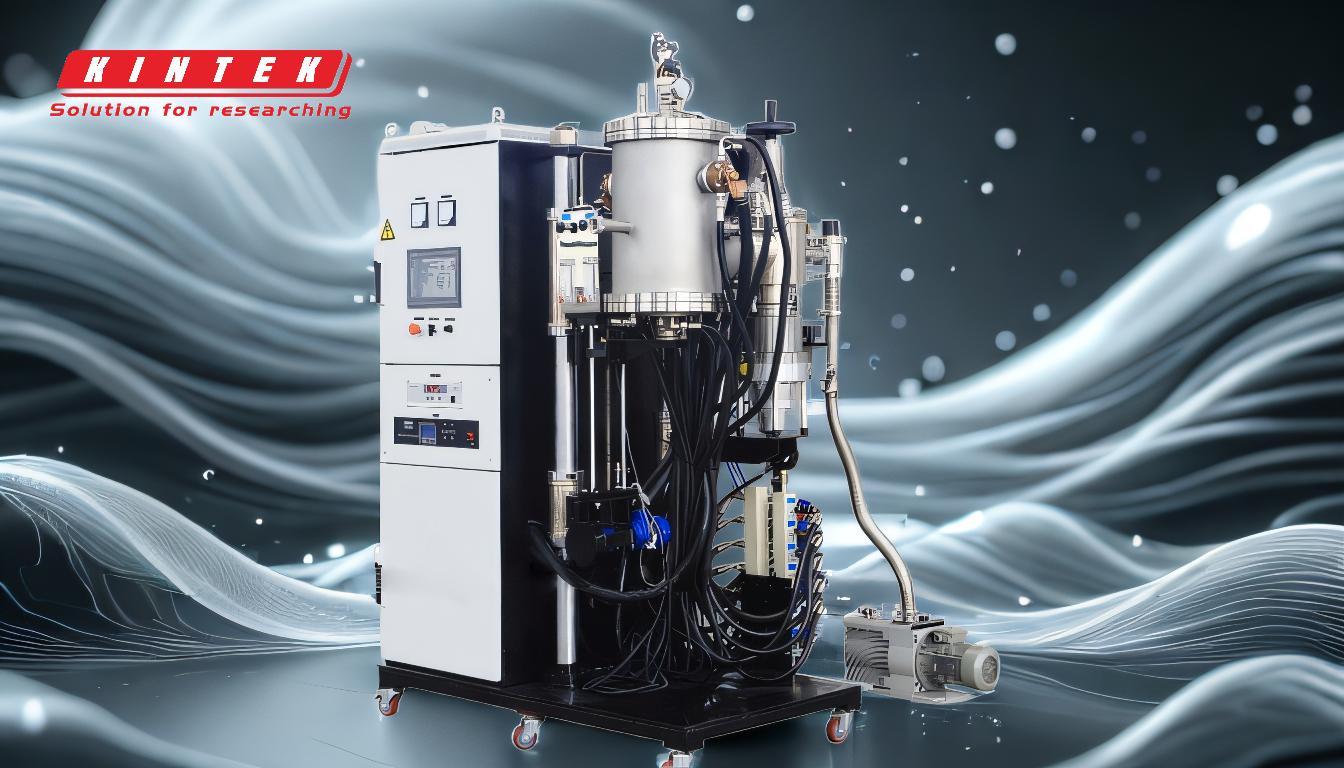
-
Pressure Range in RF Sputtering
- The chamber pressure in RF sputtering typically ranges from 0.5 to 10 mTorr.
- This pressure range is crucial for maintaining the ionization of the sputtering gas (usually argon) and ensuring efficient sputtering of the target material.
- At lower pressures (closer to 0.5 mTorr), sputtered ions travel ballistically with high energy, leading to direct and energetic deposition on the substrate.
- At higher pressures (closer to 10 mTorr), ions collide more frequently with gas atoms, resulting in a diffusive, random-walk motion before deposition. This moderates the energy of the ions, leading to a more thermalized deposition process.
-
Role of Pressure in Energy Distribution
- Pressure directly influences the mean free path of sputtered ions, which determines how far an ion can travel before colliding with another gas atom.
- A lower mean free path (at higher pressures) increases the likelihood of collisions, reducing the energy of ions and promoting a more uniform, low-energy deposition.
- A higher mean free path (at lower pressures) allows ions to retain their energy, resulting in high-energy impacts that can improve film density and adhesion.
-
Impact on Deposition Characteristics
- The choice of pressure affects the deposition rate, film quality, and uniformity.
- Higher pressures (e.g., 10 mTorr) are often used for depositing delicate or insulating materials, as the moderated ion energy reduces the risk of damage to the substrate or target.
- Lower pressures (e.g., 0.5 mTorr) are preferred for applications requiring dense, high-quality films, as the high-energy ions enhance film adhesion and reduce porosity.
-
Pressure and RF Sputtering Mechanism
- RF sputtering relies on alternating cycles of positive and negative bias to prevent ion buildup on insulating targets.
- The pressure must be carefully controlled to ensure that the sputtering gas remains ionized and that the target material is evenly sputtered.
- At the optimal pressure range (0.5–10 mTorr), the RF power source (13.56 MHz) effectively ionizes the gas, creating a stable plasma that facilitates consistent sputtering.
-
Comparison with Other Sputtering Techniques
- RF sputtering operates at lower pressures compared to some other techniques, such as DC sputtering, which may use higher pressures for conductive targets.
- The lower pressure range in RF sputtering is particularly advantageous for dielectric materials, as it minimizes arcing and ensures uniform deposition.
-
Practical Considerations for Equipment Purchasers
- When selecting equipment for RF sputtering, ensure that the vacuum system can maintain the required pressure range (0.5–10 mTorr) with high precision.
- Consider the compatibility of the chamber design with the desired pressure range, as this will impact the efficiency of the sputtering process.
- Evaluate the cost implications of operating at lower pressures, as achieving and maintaining high vacuum levels may require more advanced pumping systems.
-
Pressure and Substrate Size
- RF sputtering is typically used for smaller substrates due to the higher costs associated with maintaining the required pressure and RF power levels.
- The pressure range must be carefully optimized for the substrate size to ensure uniform deposition and avoid edge effects or non-uniform film thickness.
-
Pressure and Deposition Rate
- The deposition rate in RF sputtering is generally lower than in DC sputtering, partly due to the lower pressure range and the alternating bias cycles.
- However, the controlled pressure ensures high-quality films, making RF sputtering ideal for applications requiring precise and uniform coatings.
By understanding the role of pressure in RF sputtering, equipment and consumable purchasers can make informed decisions about system specifications and process parameters to achieve optimal results for their specific applications.
Summary Table:
Aspect | Details |
---|---|
Pressure Range | 0.5–10 mTorr |
Key Role | Controls ionization, energy distribution, and deposition characteristics |
Low Pressure (0.5 mTorr) | High-energy ballistic impacts for dense, high-quality films |
High Pressure (10 mTorr) | Low-energy thermalized motion for delicate or insulating materials |
RF Power Source | 13.56 MHz, 1000 V peak-to-peak |
Applications | Ideal for dielectric materials and precise, uniform coatings |
Ready to optimize your RF sputtering process? Contact our experts today for tailored solutions!