The time it takes to solder depends on several factors, including the type of solder, the materials being joined, the soldering method, and the skill level of the person performing the task. Soldering typically involves heating the solder to its melting point, applying it to the joint, and allowing it to cool and solidify. For small electronics, soldering a single joint might take just a few seconds, while more complex projects could take several minutes or longer. Proper preparation, such as cleaning the surfaces and using flux, can significantly reduce soldering time. Additionally, the choice of soldering iron and its temperature settings play a crucial role in achieving efficient and reliable solder joints.
Key Points Explained:
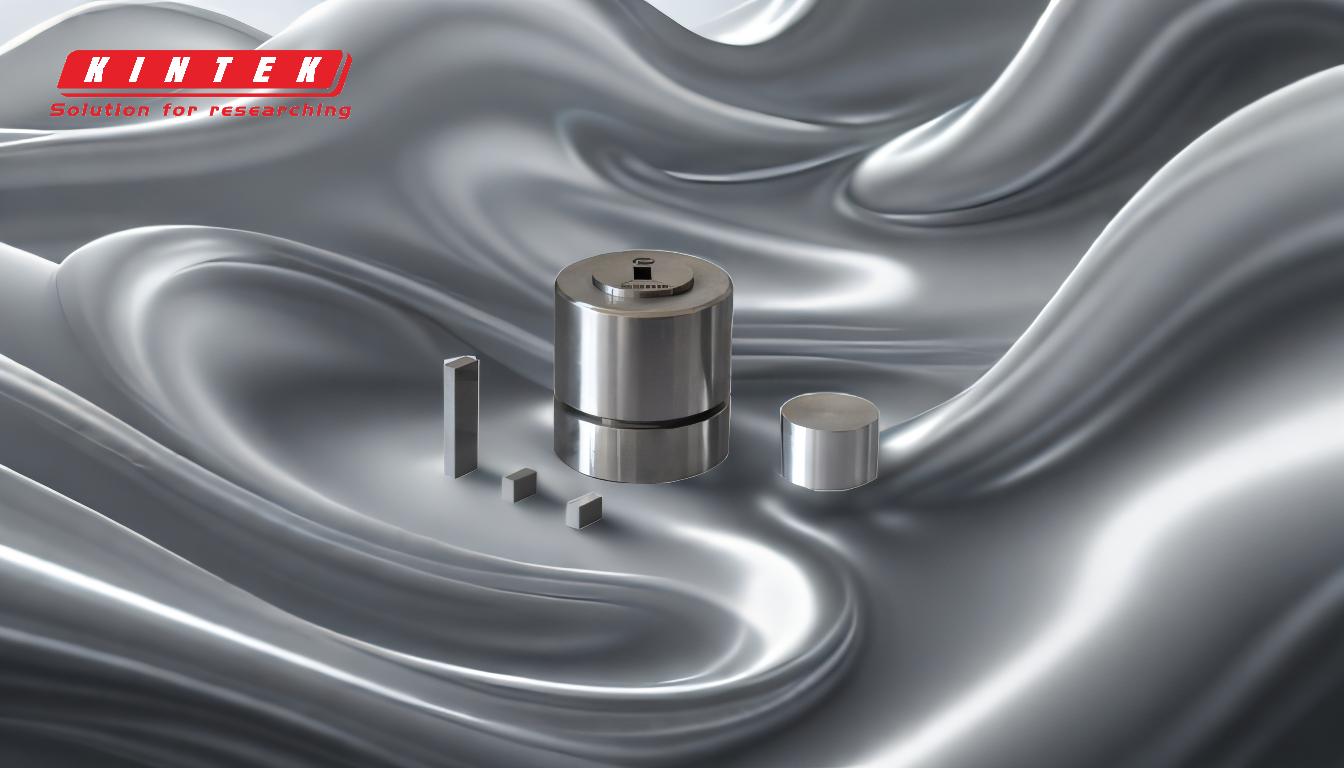
-
Factors Influencing Soldering Time:
- Type of Solder: Different solders have varying melting points and flow characteristics. For example, lead-based solders melt at lower temperatures than lead-free alternatives, which can affect how quickly the solder melts and flows.
- Materials Being Joined: The thermal conductivity of the materials being soldered can influence the time required. Metals with higher thermal conductivity, like copper, may require more heat and time to reach the soldering temperature.
- Soldering Method: The method used (e.g., hand soldering, reflow soldering, or wave soldering) can significantly impact the time. Hand soldering is typically slower but offers more control, while automated methods like reflow soldering are faster for mass production.
- Skill Level: Experienced solderers can complete tasks more quickly and efficiently than beginners, as they are more adept at controlling the heat and applying the solder accurately.
-
Preparation and Its Impact on Time:
- Cleaning Surfaces: Properly cleaning the surfaces to be soldered removes oxidation and contaminants, which can hinder the solder's ability to flow and bond. This step can reduce the overall soldering time by ensuring a better connection on the first attempt.
- Using Flux: Flux helps to clean the metal surfaces and improve the wetting of the solder, allowing it to flow more easily and create a stronger bond. This can speed up the soldering process and reduce the need for rework.
-
Role of Soldering Equipment:
- Soldering Iron Temperature: The temperature setting of the soldering iron is crucial. If the iron is too cool, the solder may not melt properly, leading to longer soldering times and potential joint failures. Conversely, if the iron is too hot, it can damage components or cause the solder to flow too quickly, leading to poor joints.
- Tip Size and Shape: The size and shape of the soldering iron tip should match the task. A larger tip can transfer more heat, which is useful for bigger joints, while a smaller tip is better for precision work on small components.
-
Typical Timeframes for Different Soldering Tasks:
- Small Electronics: Soldering a single joint on a small electronic component, such as a resistor or capacitor, typically takes just a few seconds. However, assembling an entire circuit board with multiple components can take several minutes to an hour, depending on complexity.
- Plumbing: Soldering copper pipes in plumbing applications usually takes longer due to the larger size of the joints and the need for more heat. Each joint might take a few minutes to heat, apply solder, and cool.
- Jewelry Making: Soldering in jewelry making can vary widely depending on the size and complexity of the piece. Simple joints might take a few seconds, while intricate designs could require several minutes per joint.
-
Tips for Reducing Soldering Time:
- Pre-tinning: Applying a small amount of solder to the tip of the soldering iron (pre-tinning) can help transfer heat more efficiently to the joint, reducing the time needed to melt the solder.
- Using the Right Tools: Investing in high-quality soldering irons, tips, and accessories can make the process faster and more reliable. For example, a temperature-controlled soldering station allows for precise heat management.
- Practice and Experience: As with any skill, practice improves efficiency. Over time, solderers develop a feel for the right amount of heat and solder to apply, which can significantly reduce the time needed for each joint.
By understanding these factors and implementing best practices, the time required for soldering can be optimized, leading to faster and more reliable results.
Summary Table:
Factor | Impact on Soldering Time |
---|---|
Type of Solder | Lead-based solders melt faster than lead-free alternatives. |
Materials Being Joined | High thermal conductivity materials (e.g., copper) require more time to heat. |
Soldering Method | Hand soldering is slower but offers control; automated methods (e.g., reflow) are faster. |
Skill Level | Experienced solderers work faster and more efficiently than beginners. |
Preparation | Cleaning surfaces and using flux reduces time by improving solder flow and bond quality. |
Equipment | Proper temperature settings and tip size/type optimize heat transfer and speed up soldering. |
Task Complexity | Small electronics take seconds per joint; plumbing or jewelry can take minutes per joint. |
Need help optimizing your soldering process? Contact our experts today for personalized advice!