Hot Isostatic Pressing (HIP) is a versatile and advanced manufacturing process with a wide range of applications across various industries. It is primarily used for consolidating powders, healing defects in castings, and enhancing the properties of materials. HIP is particularly valuable in industries that require high-performance materials, such as aerospace, automotive, medical, and energy sectors. The process involves applying high temperature and pressure uniformly to materials, resulting in improved density, strength, and structural integrity. HIP is also essential in additive manufacturing, where it helps eliminate porosity and improve the mechanical properties of 3D-printed components. Overall, HIP plays a critical role in producing high-quality, defect-free materials and components.
Key Points Explained:
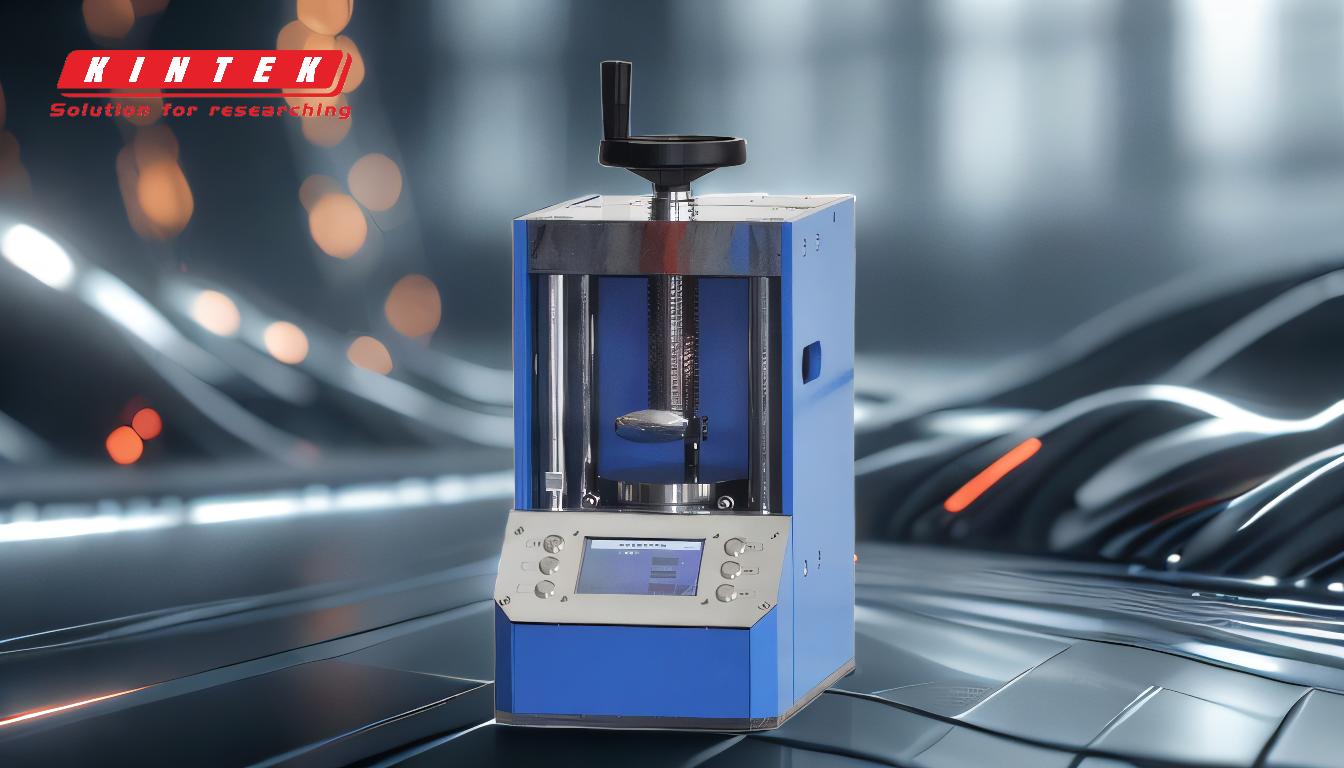
-
Consolidation of Powders:
- HIP is widely used to consolidate metal, ceramic, and composite powders into fully dense components. This is particularly important in powder metallurgy, where achieving 100% theoretical density is crucial for high-performance applications.
- The process is ideal for producing complex shapes and near-net-shape components, reducing the need for extensive machining and material waste.
-
Defect Healing in Castings:
- HIP is extensively used to eliminate internal defects such as porosity, voids, and cracks in castings. This improves the mechanical properties and reliability of components, making them suitable for critical applications in industries like aerospace and automotive.
- By subjecting castings to high temperature and pressure, HIP ensures uniform density and enhances fatigue resistance, which is vital for components subjected to cyclic loading.
-
Diffusion Bonding:
- HIP is employed in diffusion bonding, where two or more materials are joined together without the use of adhesives or fillers. This technique is used to create metal-clad parts, such as bimetallic components, which combine the properties of different materials.
- Diffusion bonding is particularly useful in the production of components for the nuclear and chemical industries, where material integrity and resistance to harsh environments are critical.
-
Additive Manufacturing (AM):
- HIP is a key post-processing step in additive manufacturing, especially for metal 3D-printed parts. It helps eliminate residual porosity and improves the mechanical properties of AM components, making them comparable to traditionally manufactured parts.
- This application is increasingly important in industries like aerospace and medical, where 3D-printed components must meet stringent quality and performance standards.
-
Production of Advanced Alloys and Ceramics:
- HIP is used to produce advanced alloy products that are difficult or impossible to manufacture using traditional casting methods. This includes high-strength, high-temperature alloys used in turbine engines and other demanding applications.
- The process is also ideal for manufacturing high-performance ceramic products, such as zirconia and alumina ceramics, which require exceptional strength and durability.
-
Applications in Various Industries:
- HIP is utilized in a wide range of industries, including pharmaceuticals, explosives, chemicals, food, and nuclear fuel ferrites. Its ability to produce dense, defect-free materials makes it indispensable for applications requiring high reliability and performance.
- In the nuclear industry, HIP is used to produce fuel pellets and other components that must withstand extreme conditions.
-
Environmental and Economic Benefits:
- HIP reduces material waste by enabling the production of near-net-shape components, minimizing the need for machining and finishing processes.
- The process also enhances the sustainability of manufacturing by improving the lifespan and performance of components, reducing the need for replacements and repairs.
In summary, Hot Isostatic Pressing (HIP) is a critical technology for producing high-quality, defect-free materials and components across a wide range of industries. Its applications in powder consolidation, defect healing, diffusion bonding, additive manufacturing, and advanced material production make it an indispensable tool for modern manufacturing.
Summary Table:
Application | Key Benefits |
---|---|
Powder Consolidation | Produces fully dense components, reduces material waste, ideal for complex shapes |
Defect Healing in Castings | Eliminates porosity and cracks, enhances fatigue resistance and reliability |
Diffusion Bonding | Joins materials without adhesives, critical for nuclear and chemical industries |
Additive Manufacturing | Eliminates porosity in 3D-printed parts, improves mechanical properties |
Advanced Alloys & Ceramics | Produces high-strength, high-temperature alloys and durable ceramics |
Industry Applications | Aerospace, automotive, medical, nuclear, and more |
Environmental Benefits | Reduces waste, improves sustainability, and extends component lifespan |
Discover how HIP can revolutionize your manufacturing process—contact our experts today!